Fibre or fibre is a natural or man-made substance that is significantly longer than it is wide. It is defined as one of the delicate, hair portions of the tissues of a plant or animal or other substances that are very small in diameter in relation to their length. A fibre is a material which is several hundred times as long as its thick.
Natural fibre
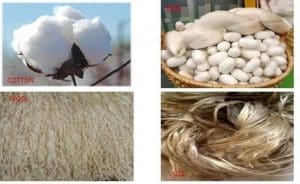
source: https://fashion2apparel.blogspot.com/2016/12/important-textile-fibers-densities.html
Natural fibre, any hair like raw material directly obtainable from an animal, vegetable, or mineral source and convertible into nonwoven fabrics such as felt or paper or, after spinning into yarns, into woven cloth. A natural fibre may be further defined as an agglomeration of cells in which the diameter is negligible in comparison with the length. Although nature abounds in fibrous materials, especially cellulosic types such as cotton, wood, grains, and straw, only a small number can be used for textile products or other industrial purposes. Apart from economic considerations, the usefulness of a fibre for commercial purposes is determined by such properties as length, strength, pliability, elasticity, abrasion resistance, absorbency, and various surface properties. Most textile fibres are slender, flexible, and relatively strong. They are elastic in that they stretch when put under tension and then partially or completely return to their original length when the tension is removed.
Types of Natural fibre
Cotton
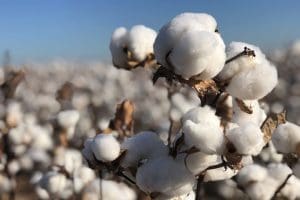
source: https://www.abc.net.au/news/2019-12-18/top-end-and-ord-valley-cotton-strengthens-as-production-plummets/11796742
Cotton is a soft, fluffy staple fiber that grows in a boll, or protective case, around the seeds of the cotton plants of the genus Gossypium in the mallow family Malvaceae. The fiber is almost pure cellulose. Under natural conditions, the cotton bolls will increase the dispersal of the seeds.
The plant is a shrub native to tropical and subtropical regions around the world, including the Americas, Africa, Egypt and India. The greatest diversity of wild cotton species is found in Mexico, followed by Australia and Africa. Cotton was independently domesticated in the Old and New Worlds.
The fiber is most often spun into yarn or thread and used to make a soft, breathable textile. The use of cotton for fabric is known to date to prehistoric times; fragments of cotton fabric dated to the fifth millennium BC have been found in the Indus Valley Civilization, as well as fabric remnants dated back to 6000 BC in Peru.
Although cultivated since antiquity, it was the invention of the cotton gin that lowered the cost of production that led to its widespread use, and it is the most widely used natural fiber cloth in clothing today. Cotton is one of the most popular natural fabrics and is often used for clothing and bedding. The fabric is comfortable on skin and adjusts to temperatures that make it suitable for all seasons and climates. Cotton will absorb sweat during hot weather and cool the body and retains heat during the winter. Your sure to have multiple items made with cotton in your closet and throughout your décor.
Manufacturing process of Cotton
Cultivation:
Cotton requires about two hundred days of continuous warm weather with adequate moisture and sunlight; frost is harmful to the plant. Usually in March or April selected cottonseeds are planted. The flowers in cotton plants appear in June or July and the cotton is usually ripe for gathering between August and October. The seasons may differ in the different places of the world. As the flower withers it is succeeded by a closed pod. This contains seeds, which are wrapped up in young actively growing hairs. Each cottonseed may produce as many as 20,000 fibres. When the seeds are nearly ripe the pod burst open and the cotton hairs project, forming a white fluffy mass called a boll. During this period, the plant is subject to attack by many insects (e.g. Boll weevil, Boll worm, Caterpillar). Insecticides are sprayed to protect the plants at this stage. The fibers are now exposed to the sun when they complete their ripening, and the cell gradually dries up, leaving the cotton in fit state for harvesting.
Harvesting:
The ripe bolls having matured fibers are picked by machines in developed countries and by hand in developing countries. Mechanical picking, a faster and cost-effective method of harvesting, has some disadvantages as machine picks the immature bolls, as well as leaves, stem fragments with the matured bolls. On the other hand higher grade of cotton is obtained by a selective and good hand picking. An expert picker can easily trace out the matured bolls and does not pick leaves or stem fragments with it. This method is slower and the most expensive in developed countries but better for developing countries.
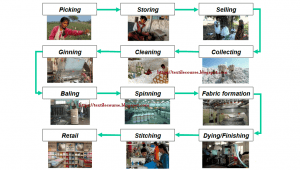
source: https://textilecourse.blogspot.com/2018/02/cotton-fiber-king-natural-fiber.html
Ginning:
After the crop has been gathered the fibers are separated from the seeds by a process known as ginning. Gins (i.e. ginning machines) may be classified into two types the saw gin and the roller gin. A saw gin consists of a series of circular saws having specially shaped teeth and used mainly for short and medium staple cottons.
Modern gins have 80-120 saws mounted on a long, horizontal shaft at suitable intervals. Seed cotton is fed through a hopper and the saws operate against it as the fibres known as lints become separated from the seed. In a roller gin, a knife jerks the seed from the fibre while the latter is pulled away between a roller and a fixed knife. McCarthy gin is a special type of roller gin. Roller ginning which is often preferred for longer fibres is slower and more costly process.
Cotton linters are the short, fuzzy hair-like fibres that remain on the seeds after ginning has been done. The cotton linters are removed by a second ginning process. They are used in the manufacture of viscose (or rayons) and acetates, plastics, shatter proof glass, photographic film and for other purposes.
Baling:
After ginning, the lints are compressed into rectangular bales, which are covered with jute or polypropylene bagging and bound with iron bands. The bales generally weigh about 480 or 500 pounds each. These bales are then sent to the yarn manufacturing mills
Grading:
The assessment of cotton is carried out traditionally by the cotton classer, who depends upon personal skill and long experience in judging cotton quality by inspection and feel. The assessment is based on (1) the staple length, (2) the colour and (3) the amount of impurity in the cotton. The classer works usually by a hand-examination of the cotton. Staple length is judged by taking a sample and pulling it to display a filmy web of fibre.
Silk
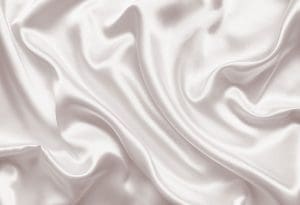
source: https://heiq.com/2016/03/09/heiq-real-silk-finish-brings-a-touch-of-luxury-to-everyone/
Silk is an elegant fibre and the most durable of all of the natural fabrics. The fabric has a rich history and is used for elegant dresses and fine clothing as well as for bedding. Silk is very comfortable on the skin and is very popular throughout the world.
Manufacturing process of silk
- Sericulture
- Sorting cocoons
- Softening and sericin
- Reeling
- Throwing
Sericulture:
The cultivation of silkworms for the purpose of producing silk is called sericulture. The best raw silk is obtained from the species of moth called Bombyx Mori. Breeding of silkworm occurs once in a year but under scientific conditions, they may be hatched three times a year. Larvae of about 3mm are hatched from the eggs. For about 20 to 30 days they are carefully nurtured and are fed five times a day on chopped mulberry leaves. In the meantime, the larvae charge their skin for four times and are formed into caterpillar of about 9cm long. Now they are ready to spin cocoon for which racks, clusters of twigs or straw are provided.
The caterpillar have small openings under their jaws called spinnerets through which they secret a protein like substance. This substance solidifies when it comes in contact with air and the filament thus formed is spun around the silkworm in the figure resembling the digit 8.
Sorting cocoon:
The cocoon is sorted according to color, shape and texture, as all these affect the final quality of the silk. Cocoons may range from white or yellow to grayish, depending on the source abd the type of food consumed during the worm stage.Cocoon from China are white, Japanese cocoons are creamy white and yellow, Italian cocoons are yellow.
Softening the sericin:
After the cocoons have been sorted, they are put through a series of hot and cold immersions, as the sericin must be softened to permit the unwinding of the filament as one continuous thread.
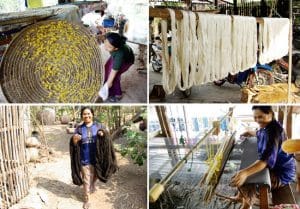
source: https://fashionmktsp16.wordpress.com/2016/03/31/silk-production-process/
Reeling:
Reeling may be achieved manually or automatically. The cocoon is brushed to locate the end of the fiber. The method is as simple as it is laborious. It is threaded through a porcelain eyelet, and the fiber is reeled onto a wheel. Meanwhile, diligent operators check for flaws in the filaments as they are being reeled. As each filament is nearly finished being reeled, a new fiber is twisted onto it, thereby forming one long, continuous thread. Sericin contributes to the adhesion of the fibers to each other’s. The average cocoon reels off about three hundred yards in a single thread.
Throwing:
The production of yarn from reeled silk known as throwing consists of adding twist or of doubling and further twisting these strands in to desired size.
Linen
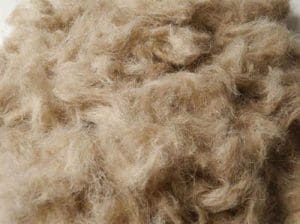
source: https://www.fibre2fashion.com/fibres/linen-fibre-suppliers-16116054
Linen fiber is a cellulose fiber derived from the flax plant trunk. Linen yarn is woven from the long fibers found behind the bark in a multi-layered stalk of the flax plant. In order to restore cellulose fibers from the plant, the wooden trunk and the inner pith (pectin), which binds the fibers together in a clump, must be eliminated away. Cellulose fibers are then ready for spinning. Linen fiber is one of the most strength of natural fibers. It is also comfortable and still widely used.
Manufacturing Process of Lenin
Planting
Flax plants are ready for harvesting after about 100 days of growth. Since flax plants do not tolerate heat, they must be planted in the cooler part of the year to avoid crop death.
Growth
These days, flax seeds are usually sown with machines. Since flax plants don’t effectively prevent the incursion of weeds, herbicides and tilling are generally used to prevent reduced yields in flax crops.
Harvesting
Once flax stems are yellow and their seeds are brown, these plants are ready to be harvested. While it’s possible to harvest flax by hand, machines are usually used for this process.
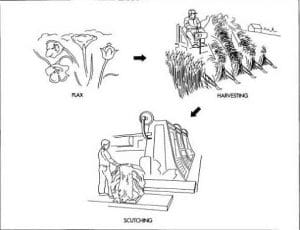
source: http://www.madehow.com/Volume-4/Linen.html
Fiber Separation
After flax stalks are harvested, they are processed through a machine that removes leaves and seeds. Then, manufacturers separate flax’s fibrous outer stalk from its soft, woody interior. This process is called retting, and unless it is expertly accomplished, the delicate flax fibers used for textile production could be damaged.
Breaking
Next, the decomposed stalks are broken up, which separates the unusable outer fibers of flax stalks from their usable inner fibers. To accomplish this step, the flax stalks are sent through rollers that crush them, and then rotating paddles remove the outer fibers from the stalks.
Combing
Now that the inner fibers are separated from the other fibers, they can be combed into thin strands. Once the fibers have been combed, they will be ready for spinning.

source: http://www.madehow.com/Volume-4/Linen.html
Spinning
Spinning of flax yarn used to be accomplished with a foot-powered flax wheel, but these days, flax producers use industrial machines for this process. To spin flax fibers, these short, combed fibers are connected with devices called spreaders, and the resulting strings, called rovings, are then ready to be spun.
Reeling
After being spun on a spinning frame, the resulting yarn is reeled onto a bobbin. To ensure that flax yarn won’t fall apart, it’s necessary to perform this reeling process in wet, humid conditions, and the spun yarn is run through a hot water bath to further ensure yarn cohesion.
Drying
Finally, flax manufacturers dry the finished yarn and reel it onto bobbins. The yarn is then ready to be dyed, treated, and made into apparel, homewares, or other types of textile products.
Wool

source: https://www.farmonline.com.au/story/6656507/abares-tips-steady-rise-for-wool-prices-and-production/
Wool is extremely durable and resists wrinkles. The fabric is very popular for winter clothing, sweaters and outerwear and is seen in homes as rugs, carpet and blankets. Wool is flame-resistant and very comfortable. The most famous and luxurious type of wool fabric is cashmere which is often used for scarves and sweaters.
Manufacturing Process of Wool
The major steps necessary to process wool from the sheep to the fabric are: shearing, cleaning and scouring, grading and sorting, carding, spinning, weaving, and finishing.
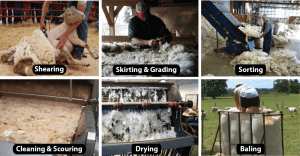
source: https://in.pinterest.com/pin/314477986481223349/
Shearing
1 Sheep are sheared once a year—usually in the springtime. A veteran shearer can shear up to two hundred sheep per day. The fleece recovered from a sheep can weigh between 6 and 18 pounds (2.7 and 8.1 kilograms); as much as possible, the fleece is kept in one piece. While most sheep are still sheared by hand, new technologies have been developed that use computers and sensitive, robot-controlled arms to do the clipping.
Grading and sorting
2 Grading is the breaking up of the fleece based on overall quality. In sorting, the wool is broken up into sections of different quality fibers, from different parts of the body. The best quality of wool comes from the shoulders and sides of the sheep and is used for clothing; the lesser quality comes from the lower legs and is used to make rugs. In wool grading, high quality does not always mean high durability.
Cleaning and scouring
3 Wool taken directly from the sheep is called “raw” or “grease wool.” It contains sand, dirt, grease, and dried sweat (called suint); the weight of contaminants accounts for about 30 to 70 percent of the fleece’s total weight. To remove these contaminants, the wool is scoured in a series of alkaline baths containing water, soap, and soda ash or a similar alkali. The byproducts from this process (such as lanolin) are saved and used in a variety of household products. Rollers in the scouring machines squeeze excess water from the fleece, but the fleece is not allowed to dry completely. Following this process, the wool is often treated with oil to give it increased manageability.
Carding
4 Next, the fibers are passed through a series of metal teeth that straighten and blend them into slivers. Carding also removes residual dirt and other matter left in the fibers. Carded wool intended for worsted yarn is put through gilling and combing, two procedures that remove short fibers and place the longer fibers parallel to each other. From there, the sleeker slivers are compacted and thinned through a process called drawing. Carded wool to be used for woolen yarn is sent directly for spinning.
Spinning
5 Thread is formed by spinning the fibers together to form one strand of yarn; the strand is spun with two, three, or four other strands. Since the fibers cling and stick to one another, it is fairly easy to join, extend, and spin wool into yarn. Spinning for woolen yarns is typically done on a mule spinning machine, while worsted yarns can be spun on any number of spinning machines. After the yarn is spun, it is wrapped around bobbins, cones, or commercial drums.
Weaving
6 Next, the wool yarn is woven into fabric. Wool manufacturers use two basic weaves: the plain weave and the twill. Woolen yarns are made into fabric using a plain weave (rarely a twill), which produces a fabric of a somewhat looser weave and a soft surface (due to napping) with little or no luster. The napping often conceals flaws in construction.
Worsted yarns can create fine fabrics with exquisite patterns using a twill weave. The result is a more tightly woven, smooth fabric. Better constructed, worsteds are more durable than woolens and therefore more costly.
Finishing
7 After weaving, both worsteds and woolens undergo a series of finishing procedures including: fulling (immersing the fabric in water to make the fibers interlock); crabbing (permanently setting the interlock); decating (shrink-proofing); and, occasionally, dyeing. Although wool fibers can be dyed before the carding process, dyeing can also be done after the wool has been woven into fabric.
Jute
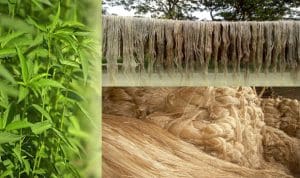
source: https://textilelearner.blogspot.com/2012/03/features-oa-jute-fiber-properties-of.html
Jute is reserved for carpet, rugs and floors in a home. The woven natural fabric is extremely durable although it can be difficult to clean and maintain.
Look around your home and see if you can identify the items made from the natural fibres above. Decide which items you love the most and consider purchasing more décor and accessories made of that natural fabric.
Manufacturing Process of Jute
Jute is a rainy season crop, sown from March to May according to rainfall and type of land. It is harvested from June to September depending upon whether the sowings are early or late.
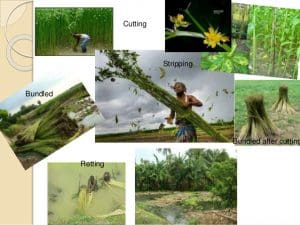
source: https://pt.slideshare.net/biniyaa1/natural-fiber-jute/8
Climate and Soils
Jute requires a warm and humid climate with temperature between 24° C to 37° C. Constant rain or water-logging is harmful. The new gray alluvial soil of good depth, receiving salt from annual floods, is best for jute. Flow ever jute is grown widely in sandy loams and clay loams.
Sowing of jute
Sowing of jute in midlands and high lands starts with showers in March or April and continues till early June in the western part of the jute belt. Compost or firm yard manure, Phosphorus and Potash, Nitrogen fertilizers are used as a fertilizer. Interculturing is essential in the early stage. Pasts are also require for plant protection.
Harvesting
Jute is harvested any time between 120 days to 150 days when the flowers have been shed, early harvesting gives good healthy fibers. The plant from 8 to 12 feet high are cut with stickles at or close the ground level. In flooded land, plants are up rooted. The harvested plants are left in field for 3 days for the leaves to shed.
The stems are then made up into bundles for steeping in water. Steeping is carried out immediately after harvest.
The Fibre Extraction
The jute plant’s fibres lie beneath the bark and surrounded the woody central part of the stem. To extract the fibres from the stem, the process is carried out in the following stages :
Retting
Retting is a process in which the tied bundles of jute stalks are taken to the tank by which fibres get loosened and separated from the woody stalk. The bundles are steeped in water at least 60 cm to 100 cm depth. The retting process is completed in 8 to 30 days, when the barks separate out easily from the stick or wood and the fibres are ready for extraction. A development in recent years is adoption of ribbon retting technology in jute growing trade of the country.
Stripping (Fibre Extraction)
Stripping is the process of removing the fibres from the stalk after the completion of retting. Fibres are removed from the stalk by any one of the following methods :
(i) Single plants are taken and their fibers are taken off.
(ii) Taken off a handful of stalks,breaking it in a to and fro motion in water.
(iii) Washing the stalks first by standing in waist deep water and then stripping afterwards.
When there is a plenty of water, bundles of stalks are laid in the pond ditches or slow moving streams and left for 5-15 days under water. The bunch of stem is held in one hand and the root end tapped lightly with a mallet. After loosens the rest of fibres, fibres are extracted and washed.
Washing and Drying
Extracted fibres are washed in clean water. The dark colour of fibres can be removed by dipping them in tamarind water for 15 to 20 minutes and again washed in clean water. After squeezing excess water the fibres are hang on bamboo railing for sun drying for 2-3 days.
Bailing and Packing
The jute fibre is graded into tops, middles, B, C and X-bottoms. Packing into Kutcha bales about 250 pounds for use in the home trade. they are transported to jute market or direct to jute mills.
Manmade Fibers
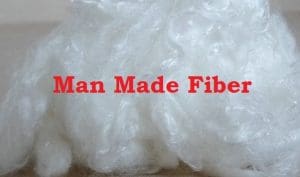
source: https://fashion2apparel.blogspot.com/2017/06/production-classification-man-made-fiber.html
Man-made fibre, fibre whose chemical composition, structure, and properties are significantly modified during the manufacturing process. Man-made fibres are spun and woven into a huge number of consumer and industrial products, including garments such as shirts, scarves, and hosiery; home furnishings such as upholstery, carpets, and drapes; and industrial parts such as tire cord, flame-proof linings, and drive belts. The chemical compounds from which man-made fibres are produced are known as polymers, a class of compounds characterized by long, chainlike molecules of great size and molecular weight. Many of the polymers that constitute man-made fibres are the same as or similar to compounds that make up plastics, rubbers, adhesives, and surface coatings. Indeed, polymers such as regenerated cellulose, polycaprolactam, and polyethylene terephthalate, which have become familiar household materials under the trade names rayon, nylon, and Dacron (trademark), respectively, are also made into numerous no fibre products, ranging from cellophane envelope windows to clear plastic soft-drink bottles. As fibres, these materials are prized for their strength, toughness, resistance to heat and mildew, and ability to hold a pressed form.
Types of Manmade fiber
Nylon
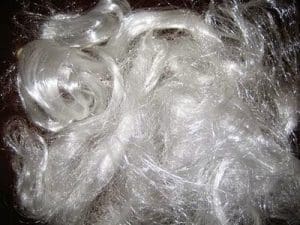
source: https://textilelearner.blogspot.com/2011/08/nylon-fiber-nylon-fiber-production_6866.html
It is an artificial fibre made of polyamide which contains carbon, oxygen, nitrogen, and hydrogen. The material is also resistant to wrinkling, does not absorb water, and it dries quickly, Exceptionally strong, Elastic, Lustrous, Easy to wash, Resistant to damage from oil and many chemicals, Can be precolored or dyed in wide range of colours, Resilient, Filament yarns provide smooth, soft, long-lasting fabrics.
Manufacturing Process of Nylon:
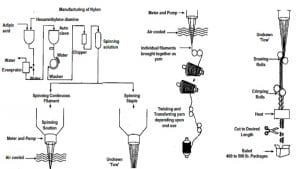
source: http://www.brainkart.com/article/Nylon—Manufacturing-Process-and-Properties_1769/
Nylon is a linear condensation polymer made from hexamethylene diamine and adipic acid. Specific amounts of the two chemicals are combined in solution to form nylon salt. This salt is purified, polymerized, extruded in ribbon form, and chipped into small flakes or pellets. These flakes or pellets are melted and extruded through a spinneret into cool air and the nylon filaments are formed.
The polymer chips are melted by heat in an autoclave and pumped to the spinneret. The hot syrupy solution is pumped through the spinneret. It emerges in strands which can be stretched like warm taffy. The size of the fiber is determined by the size of the holes and the speed with which the fiber is withdrawn from the spinneret. The fibers are cooled by air blown across them. By the drawing process either filament or staple fibers are prepared.
Polyester

source: https://www.indiamart.com/proddetail/polyester-fiber-11692597791.html
The most important synthetic fibre. They contain at least 85% of polymericester of a substituted aromatic carboxylic acid including, but not restricted to, terephthalic acid and f-hydroxybenzoic acid. The manufacturing process uses melt-spinning so the size and shape can be adjusted for specific applications.
The Manufacturing Process of Polyester
Polyester is manufactured by one of several methods. The one used depends on the form the finished polyester will take. The four basic forms are filament, staple, tow, and fiberfill. In the filament form, each individual strand of polyester fiber is continuous in length, producing smooth-surfaced fabrics. In staple form, filaments are cut to short, predetermined lengths. In this form polyester is easier to blend with other fibers. Tow is a form in which continuous filaments are drawn loosely together. Fiberfill is the voluminous form used in the manufacture of quilts, pillows, and outerwear. The two forms used most frequently are filament and staple.

source: http://www.madehow.com/Volume-2/Polyester.html
Manufacturing Filament Yarn
Polymerization
To form polyester, dimethyl terephthalate is first reacted with ethylene glycol in the presence of a catalyst at a temperature of 302-410°F (150-210°C).
The resulting chemical, a monomer (single, non-repeating molecule) alcohol, is combined with terephthalic acid and raised to a temperature of 472°F (280°C). Newly-formed polyester, which is clear and molten, is extruded through a slot to form long ribbons.
Drying
After the polyester emerges from polymerization, the long molten ribbons are allowed to cool until they become brittle. The material is cut into tiny chips and completely dried to prevent irregularities in consistency.
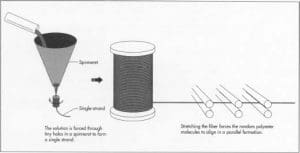
source: http://www.madehow.com/Volume-2/Polyester.html
Melt spinning
Polymer chips are melted at 500-518°F (260-270°C) to form a syrup-like solution. The solution is put in a metal container called a spinneret and forced through its tiny holes, which are usually round, but may be pentagonal or any other shape to produce special fibers. The number of holes in the spinneret determines the size of the yarn, as the emerging fibers are brought together to form a single strand.
At the spinning stage, other chemicals may be added to the solution to make the resulting material flame retardant, antistatic, or easier to dye.
Drawing the fiber
When polyester emerges from the spinneret, it is soft and easily elongated up to five times its original length. The stretching forces the random polyester molecules to align in a parallel formation. This increases the strength, tenacity, and resilience of the fiber. This time, when the filaments dry, the fibers become solid and strong instead of brittle.
Drawn fibers may vary greatly in diameter and length, depending on the characteristics desired of the finished material. Also, as the fibers are drawn, they may be textured or twisted to create softer or duller fabrics.
Winding
After the polyester yarn is drawn, it is wound on large bobbins or flat-wound packages, ready to be woven into material.
Manufacturing Staple Fiber
In making polyester staple fiber, polymerization, drying, and melt spinning (steps 1-4 above) are much the same as in the manufacture of filament yarn. However, in the melt spinning process, the spinneret has many more holes when the product is staple fiber. The rope-like bundles of polyester that emerge are called tow.
Drawing tow
Newly-formed tow is quickly cooled in cans that gather the thick fibers. Several lengths of tow are gathered and then drawn on heated rollers to three or four times their original length.
Crimping
Drawn tow is then fed into compression boxes, which force the fibers to fold like an accordion, at a rate of 9-15 crimps per inch (3-6 per cm). This process helps the fiber hold together during the later manufacturing stages.
Setting
After the tow is crimped, it is heated at 212-302°F (100-150°C) to completely dry the fibers and set the crimp. Some of the crimp will unavoidably be pulled out of the fibers during the following processes.
Cutting
Following heat setting, tow is cut into shorter lengths. Polyester that will be blended with cotton is cut in 1.25-1.50 inch (3.2-3.8 cm) pieces; for rayon blends, 2 inch (5 cm) lengths are cut. For heavier fabrics, such as carpet, polyester filaments are cut into 6 inch (15 cm) lengths.
Rayon
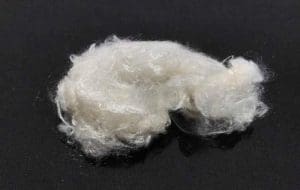
source: https://www.fibre2fashion.com/news/textile-news/nanollose-develops-plant-free-viscose-rayon-fibre-229412-newsdetails.htm
Rayon is a semi-synthetic or artificial fibre. Rayon is recognized by the name viscose rayon and art silk in the textile industry. This includes textile fibres and filaments composed of regenerated cellulose, excluding acetate. It is produced from naturally occurring polymers. The fibre is sold as artificial silk and it has a serrated round shape with a smooth surface.
The Manufacturing Process
While there are many variations in the manufacturing process that exploit the versatility of the fiber, the following is a description of the procedure that is used in making regular or viscose rayon.
Regardless of whether wood pulp or cotton linters are used, the basic raw material for making rayon must be processed in order to extract and purify the cellulose. The resulting sheets of white, purified cellulose are then treated to form regenerated cellulose filaments. In turn, these filaments are spun into yarns and eventually made into the desired fabric.
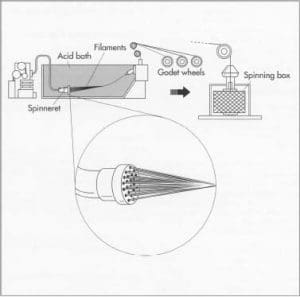
source: https://www.lord.gr/en/module/stblog/article?id_blog=2&rewrite=micromodal-is-the-king
Processing purified cellulose
Sheets of purified cellulose are steeped in sodium hydroxide (caustic soda), which produces sheets of alkali cellulose. These sheets are dried, shredded into crumbs, and then aged in metal containers for 2 to 3 days. The temperature and humidity in the metal containers are carefully controlled.
After ageing, the crumbs are combined and churned with liquid carbon disulfide, which turns the mix into orange-colored crumbs known as sodium cellulose xanthate. The cellulose xanthate is bathed in caustic soda, resulting in a viscose solution that looks and feels much like honey. Any dyes or delusterants in the design are then added. The syrupy solution is filtered for impurities and stored in vats to age, this time between 4 and 5 days.
Producing filaments
The viscose solution is next turned into strings of fibers. This is done by forcing the liquid through a spinneret, which works like a shower-head, into an acid bath. If staple fiber is to be produced, a large spinneret with large holes is used. If filament fiber is being produced, then a spinneret with smaller holes is used. In the acid bath, the acid coagulates and solidifies the filaments, now known as regenerated cellulose filaments.
Spinning
After being bathed in acid, the filaments are ready to be spun into yarn. Depending on the type of yarn desired, several spinning methods can be used, including Pot Spinning, Spool Spinning, and Continuous Spinning. In Pot Spinning, the filaments are first stretched under controlled tension onto a series of offsetting rollers called godet wheels. This stretching reduces the diameter of the filaments and makes them more uniform in size, and it also gives the filaments more strength. The filaments are then put into a rapidly spinning cylinder called a Topham Box, resulting in a cake-like strings that stick to the sides of the Topham Box. The strings are then washed, bleached, rinsed, dried, and wound on cones or spools.
Spool Spinning is very similar to Pot Spinning. The filaments are passed through rollers and wound on spools, where they are washed, bleached, rinsed, dried, and wound again on spools or cones.
In Continuous Spinning, the filaments are washed, bleached, dried, twisted, and wound at the same time that they are stretched over godet wheels.
Once the fibers are sufficiently cured, they are ready for post-treatment chemicals and the various weaving processes necessary to produce the fabric. The resulting fabric can then be given any of a number of finishing treatments. These include calendaring, to control smoothness; fire resistance; pre-shrinking; water resistance; and wrinkle resistance.
References
https://en.wikipedia.org/wiki/Fiber
https://textilelearner.blogspot.com/2012/02/what-is-textile-fiber-types-of-textile.html
https://textilelearner.blogspot.com/2012/07/production-of-cotton-fiber-from-field.html
https://www.britannica.com/topic/natural-fiber
https://sewport.com/fabrics-directory/linen-fabric
http://textileengg.blogspot.com/2015/11/manufacturing-process-of-silk.html
http://www.melrosedrapery.com/typs-natural-fabric-fibers/
http://www.madehow.com/Volume-1/Wool.html
http://www.madehow.com/Volume-2/Polyester.html
https://www.britannica.com/technology/man-made-fiber
https://textilelearner.blogspot.com/2016/04/different-types-of-man-made-fiber-with.html
http://www.brainkart.com/article/Nylon—Manufacturing-Process-and-Properties_1769/
http://www.madehow.com/Volume-1/Rayon.html