Vilas Gharat
M.D. (Gharat & Associates.)
President (Textile Association India -Mumbai)
It has been observed that day by day Loom technology is improving at rapid speed resulting into very high-speed machines. There are many units installing such highspeed machines & unable to get desire production due to high machine down time.
Please find below Loom downtime analysis which has been carried out in one of modern weaving unit. The highest downtime is due to BEAM GAITTIG & hence I would like to present my paper on simple method of reduction of down time known as SMED.
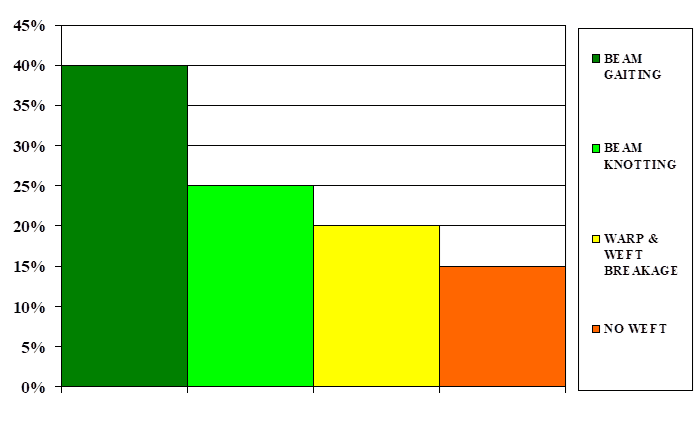
What is S.M.D.
It is known as SINGLE MINUTE EXCHANGE OF DIES & its Japanese technology developed by Mr. Shigeo Shingo. It is one of the lean methods for drastic reduction in changing time in production process.
It provides a rapid & efficient way of converting current product to next product in shortest time. It is “REVOLUTIONIZES BASIC CONCEPT OF ‘SET-UP CHANGE’.
Before explaining how it can be used in Beam Gaiting activities to reduce downtime, I would like to give you very common example of above method.
Generally, we require 5 to 10 mins to change car flat tire but in car race such as Formula One we observe all four tires & other activities are carried out by group of experts in few seconds. It is same method they are adopting known as SMED.
• From the above it is very clear that we cannot afford to waste the time in a race. The operations are fast, tools are in its place and also man power
• Replacing the Flat Tyre of Car
• Find Jack, Tommy bar, spanner, in short tools.
• Place & locate Jack below the car and lift the jack.
• Loosen the nuts.
• Remove the wheel
• Bring another wheel
• Locate & insert new wheel
• Tighten the nuts.
• Remove the jack & collect the tools.
• Place it back in the car
• Final tightening of the nuts
• ABILITY TO DISTINGUISH: –
It is very important to master the distinction between Internal & External activities. Please find chart of Internal & External activities of tire changing activities.

If you observe above chart you will notice that 50% activities are external which can be carried out earlier & kept ready to complete in actual changing time. The same method can be adopted in case of Beam Gaiting as mentioned below.
SMED FOR BEAM GAITING
Please find below case study taken in one of modern textile unit having rapier looms with 20 shafts. Initially beam gaiting actual operations recorded in Video -noting step by step timings. Then the chart is prepared as mentioned below.
ACTIVITIES RECORDED OF FILM –
no. | START | END | TOTAL | activity |
1 | LOOM STOP | |||
2 | TENSION RELEASE/PKG REMOVAL/COVER OPENING | |||
3 | BEAM CUT/CLOTH WINDING/ TEMPLE LIFTING | |||
4 | REED REMOVAL | |||
5 | EMPTYING BEAM | |||
6 | BEAM UNLOADED | |||
7 | HEALD FRAME SUPPORT REMOVAL | |||
8 | REMOVING LENO AND MOUNTING ON STAND | |||
9 | TAKING AWAY EMPTY BEAM | |||
10 | TAKING OUT DROP PIN BARS | |||
11 | HEALD FRAME REMOVAL | |||
12 | SUCTION CLEANING STARTS | |||
13 | TAKING AWAYHEALD FRAME/ DROP PIN BAR AND REED | |||
14 | BRINGING CURTAIN | |||
15 | AIR CLEANING | |||
16 | WIDTH SETTING | |||
17 | FIXING REED PIECES | |||
18 | TAKING OUT OPENER | |||
19 | MAINTENANCE | |||
20 | SETTING TAPE GUIDE | |||
21 | REMOVING CURTAIN | |||
22 | MEASURING REED LENGTH / GREASING | |||
23 | TEMPLE PLATE SETTING / RAPIER HOOK FIXING | |||
24 | STROKE SETTING | |||
25 | CHECKING ALIGNMENT | |||
26 | BRINGING BEAM TROLLEY |
27 | BEAM LOADING STARTS | |||
28 | RAPIER FIXING(RH) | |||
29 | DROP-PIN FIXING / COVER FIXING(RH RAPIER STROKE), FIXING BOTTOM H/F SUPPORT | |||
30 | ENDS STRAIGHTENING / TRANSFER TROLLEY OUT FROM LOOM | |||
31 | FIXING OF BEAM BARREL SUPPORT ROLLERS | |||
32 | PARALLELISING OF ENDS | |||
33 | BEAM LOCKED | |||
34 | REED FIXING | |||
35 | THREADING OF BEAM GAITING CLOTH | |||
36 | TYING OF KNOTS | |||
37 | HEALD FRAME TOP SUPPORT FIXING | |||
38 | PULLING OF WARP SHEET | |||
39 | RELOCKING OF BEAM | |||
40 | TEMPLE SETTING / THUMB ENDS FIXING / FEEDER THREADING | |||
41 | COVER FIXING (RH OPENER)/ BOTTOM H/F SUPPORT / SUCTION PIPE FIXING | |||
42 | MAIN MOTOR START / DESIGN FEEDING(PLAIN) | |||
43 | ENDS DRAWING STARTED | |||
44 | LOOM STARTED (PICKS INSERTED) | |||
45 | LENO FIXING (SPOOL) | |||
46 | LENO DEVICE FIXING | |||
47 | LENO SETTING | |||
48 | ENDS DRAWING STARTED IN HEALD WIRE | |||
49 | SPOOL ENDS DRAWING / DESIGN FEEDING / WEFT APPLIED AS PER PATTERN | |||
50 | THREADING OF FALSE SEVEDGE | |||
51 | MISSING HEALD WIRE FIXING | |||
52 | LOOM STARTED / DROP PIN SUPPORT FIXING | |||
53 | DOUBLE END AND PATTERN CHECKING (HEALD FRAME LIFTED IN SEQUENCE ) | |||
54 | LOOM STARTED | |||
55 | CLOTH TORN | |||
56 | WRONG DRAWN ATTENDED | |||
57 | SAMPLE WORKED (FOR STOP MARKS ) | |||
58 | CONTRAST COLOUR SAMPLE WORKED | |||
59 | LOOM RUNNING IN | |||
60 | SAMPLE CHECKING 0N SCREEN | |||
61 | LOOM STARTED FOR PRODUCTION |
Then all above activities are separated as Internal & External with time taken to complete those activities. The recorded film is shown in slow motion to team of loom shed beam gaiters’, fitters & supervisors. We had very long session of brain storming for how to carry out external activities in advance & execute at time of change in minimum time same as Formula 1 race video.
Finally, we carried out changes as per following chart & carried out following steps.
• STEPS-1-PRESENT STATUS
• VIDEO SHOOTING
• STEP 2-
• INTERNAL & EXTERNAL SET UP TIME
• 1. INTERNAL SET-UP.
• THOSE ACTIVITIES WHICH NEED STOPPING THE EQUIPMENT,
• LIKE, REMOVAL AND MOUNTING OF
• BEAM.
2. EXTERNAL SET-UP.
• THOSE ACTIVITIES WHICH CAN BE CARRIED OUT WITHOUT STOPPING THE EQUIPMENT i.e. LOOM.
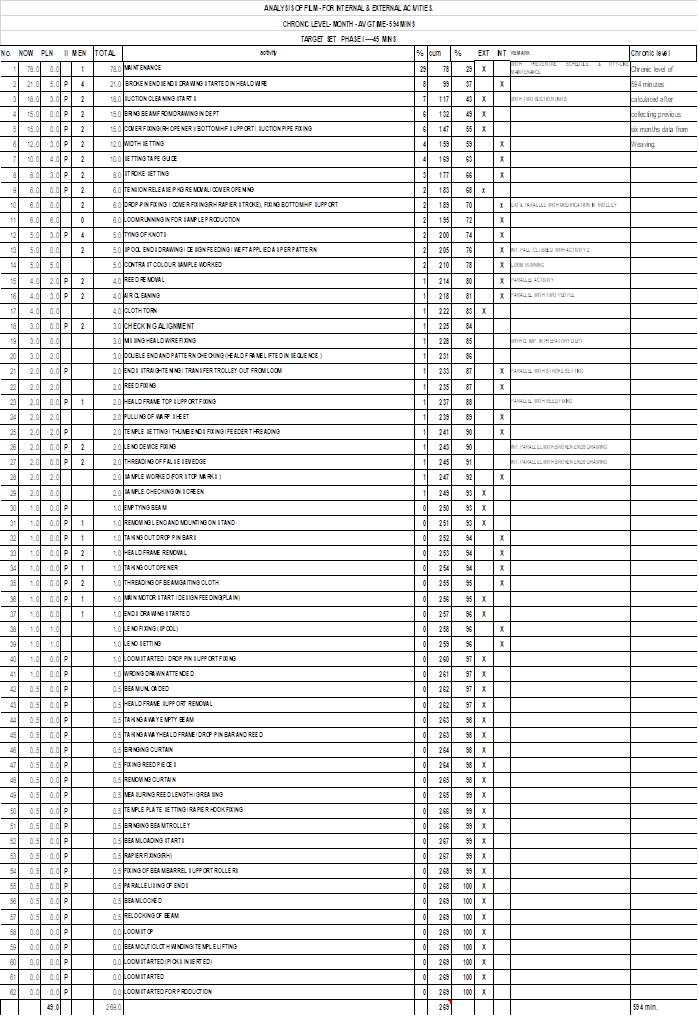
After conducting many trails, we could get following result with one-month summary. The earlier time for beam gaiting of 594 mins gradually reduced step by stem …
Step 1 594 Mins.
Step 2 269 Mins.
Step 3 112 Mins.
Final 49 Mins.
Saving 545 Mins. (9 Machine Hrs for every beam gating.)
SUMMARY
BEFORE | AFTER | ||
SR.NO | AVG.TIME | 594 | 45 |
1 | INTERNAL ACTIVITY | 60 | 22 |
2 | EXTERNAL ACTIVITY | 7 | 45 |
3 | PARALLEL | 30 | 47 |
TIME | 112 | 49 |
Hope you understood it clearly. Please visit our website www.gharatandassociates.com or send mail to gharatandassociates@gmail.com OR vilasgharat@gmail.com in case of any inquiry.