Uster, Switzerland, 20th January 2021 – A push notification appears on Muhammad Ashraf’s mobile phone. It reports that there is a variation in the CVm level at his mill. Ashraf calls his foreman to inform him, so he can take immediate action. The problem is quickly identified and fixed – thanks to the Alarm Center function with Uster Quality Expert. It gives round-the-clock monitoring of vital processes in the mill, and keeps management constantly informed of any issues.
In the case outlined here, the fault was rapidly pinpointed to a mix-up of bobbins at the Sangzor spinning mills in Uzbekistan, where Ashraf is General Manager. Ashraf has been using the Uster Mobile Alerts app for three months. Sangzor exports yarns to Pakistan, Turkey, Russia and China, and all its customers naturally expect to receive exactly the quality they specified. Ashraf knows the value of quality in keeping customers satisfied. It’s a top priority, so he likes to be informed of any deviations – whether at his desktop in the mill or on his mobile phone when he’s out.
The value of staying connected
Spinners around the world share a combination of requirements: controlling quality through immediate actions, while improving productivity and minimizing waste. Uster understands this need – and has responded with the Alarm Center, one of five Value Modules included with Uster Quality Expert. The Alarm Center prompts early intervention in quality issues. Key processes are monitored, and performance is displayed on a dashboard. It allows spinners to recognize problems at a glance, enabling immediate reactions.
Smart algorithms and in-built Uster Application Intelligence ensure reliable alerting. The Application Intelligence embedded in Assistant Q can immediately recognize issues, with no need for configuration by the spinner. Users receive problem-solving suggestions, and can also expand the knowledge base with actions they enter themselves. The learning system grows according to customer needs and ensures that relevant know-how is retained in mills.
The Alarm Center is also available on a mobile app, for quality management that is independent of time and location. There is no limit to the number of app users with one Quality Expert system. Mobile Alerts can be used by as many staff as required, to suit the mill’s organization of processes and responsibilities. Since the launch of the standalone version of Uster Quality Expert, the community of Uster Mobile Alerts app users has grown more rapidly. Uster Quality Expert Standalone connects Uster quality testing and monitoring instruments and leverages their value towards significant profitability gains. With the new standalone version, a relatively small investment means cotton spinners can quickly optimize quality and profitability at the same time.
Alerts – negative, positive and customized
Mobile Alerts shows critical issues and the Alarm Center provides negative alarms as well as positive ones. That means it points out quality issues but also suggests potential improvements. Ashraf says: “I very much appreciate the positive information, as improvement is part of the game. If you don’t improve you will stay behind.” With the latest release of Uster Quality Expert, alarms and improvements are listed separately for fast focus on serious issues – and for making quality managers easily aware of so far unnoticed improvement possibilities.
The mill for which Ashraf is responsible started operation 14 months ago with almost all new machines. He’s sure that the Mobile Alerts app will become even more important to him over time, as parts begin to show the first signs of wear. But he is already feeling the benefit of the app, especially for its performance, design and user-friendliness.
The facility to preselect which alarms to receive is another well-appreciated feature of Quality ExpertUsers can customize and activate or deactivate the kind of alarms, or the area of events, they want to get as push messages.
Make it a better life for spinners
Before the introduction of Uster Mobile Alerts, it was more difficult for spinners to see alarms. Now, quality management has become both safer and easier, as issues can be identified and located immediately. Problem-solving guidance is also another popular feature, as the app proves its worth across different staff groups, such as lab personnel, maintenance managers and all who share responsibility for professional quality supervision.
“Thanks to Uster quality assurance systems, textile spinning gradually becomes easier,” Ashraf says. “I enjoy Uster Quality Expert. It gathers and analyzes our online and offline results and keeps sending quality alerts and exceptions with possible root causes displayed graphically on my mobile phone 24/7 – and it’s good news that Uster Quality Expert expands its insightful analytics with valuable intelligence as each additional instrument is connected.”
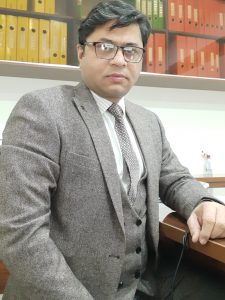
Muhammad Ashraf
About Uster Technologies
Uster is the world’s leading provider of quality management solutions from fiber to fabric.
Uster Technologies offers high-technology instruments, systems and services for quality control, prediction, certification and optimization in the textile industry. This includes systems for quality management, laboratory testing and in-line process control for fibers, staple and filament yarns, fabric inspection as well as value-added services.
Uster provides the globally-acknowledged Uster Statistics benchmarks for trading, textile know-how training, consulting and worldwide after-sales services – always aspiring to fulfill the textile market’s needs, to drive innovation forward with ‘quality in mind’.
Uster Technologies AG is headquartered in Uster, Switzerland and operates worldwide. It has sales and service subsidiaries in the major textile markets and Technology Centers in Uster (Switzerland), Knoxville (USA), Suzhou (China) and Caesarea (Israel).