The Indian textile industry is employing more than 105 million people directly and indirectly. It is one of the industries giving direct employment to such a large number of people approximately 45 million. It is also the industry that employs the highest number of services from the labor forces.
Our textile industry has a very rich culture. We are known in the textile world as a prominent player after China. Our worthiness & rich heritage is reflected in various textile products. We have also recently shown our competence in shuttles looms as well as dominated few sectors of the emerging technical textiles.
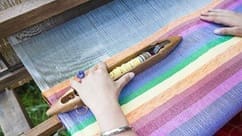
Figure 1Handloom, source internet
Indian cotton is famous in the world for producing high-value products.
The focus is more on how things are being done for ages in the industry. There are many technologies involved as far as technical textiles are concerned for e.g. spunlace, needlepunch, spunbond, melt blown, chemical bonded etc. So the point is that these many varieties of products require a particular resource beyond the raw material resources i.e. the manpower with finite skill sets.
Indian cotton is famous in the world for producing high-value products.
The focus is more on how things are being done for ages in the industry. There are many technologies involved as far as technical textiles are concerned for e.g. spunlace, needlepunch, spunbond, melt blown, chemical bonded etc. So the point is that these many varieties of products require a particular resource beyond the raw material resources i.e. the manpower with finite skill sets.
There is just not one raw material like cotton or to say the natural fibers creating baskets of products in different sectors there is also the synthetic industry having its dominance in India. Most of the value-added products produced are automated products manufactured on highly engineered machines. So the level of manpower needed in this industry requires a skillset driven by technology adaptions. The workforce required is less in number than the cotton industry but highly skilled manpower is needed. In each intermittent process, human help is needed. This human hand needs to be trained efficiently. This is where I feel currently an intervention is needed as professional training and developing the manpower is what is lacking or mishandled in our country. Let us try to understand the need gap analysis of the way things are happening for human resource development in the different sectors across the textile industry.
In ginning, as we all are aware most of the ginning press is close to the cotton-growing areas. So many practices are just carried forward for years now & the same old style of operations is still functional as in earlier days. We have observed that many malpractices are followed even today. Another angle for the no change in this training or skilling of the workforce of this sector is the hardship or environmental conditions in which the workers are working. The operations involve a lot of dust and dirt from the cotton bales, hence the people hired are not professional or not trained at all. They hire many small-time farmers who are simply put to work here without giving them proper. So there is a lot of gap as far as training needs are concerned. Similarly, we also know that the automated ginning equipment lines having the US technology are still not implemented in India. This is where the gap exists so we need to improve firstly the technology utilized for ginning and also where ever such machines are bought in the subsequent training needs to be provided.
The next process in the cotton textile industry is spinning, which is fairly organized. India is having a market share of 14% in global yarn productions. We have done remarkably well in the yarn supply. This has led us to adopt fairly all the good practices that are followed internationally. In many firms, there is senior-level training done which then trains and develops the staff under and a chain of training is created. So there is only on the job training that is provided. From the skillset point of view in spinning, the highest level of skill sets is required at the ring-spinning stage. As in this process, the production levels are very high & involves many manual operations. Let us assume the ring frame is running at 20000 rpm, the tenter needs to piece the yarn at that speed which happens periodically. Thus ring frame tenter is one of the major job profiles which needs high level of technical skills. Any errors by the tenter will get reflected on the quality parameter of the product & it needs to be rectified in the next process. The tenter skills also require training about understanding the production loss & efficiency loss to improvise his involvement in the process.
So to scale down, there is on the job training taking place for the ring frame department. But if we consider other departments like blow room, carding, combing, draw frame, or speed frame there are no proper training measures taken. However, for the entire production hall of spinning, the procedures of the on-job training are being followed.
Nowadays there is a need of involving an expert agency in man to man training for the textile workforce. This expert’s involvement with vast knowledge has also identified the physical attributes of the workforce suitable for the work for eg. Identifying what types of fingers are best suitable for the specific task. We are associated with a company called Werner International, a USA based company. One of their unique working models involves bifurcating the workforce based on their physical traits. For eg. A tenter role is handed to a person with very good eyesight having long fingers and good height that makes it easy for him to piece or to creel bobbing at the same time he should be clean and trim to move within ring frame aisles. Similarly, a person involved in the combing department must be the one with an alert mind as certain short fibers are removed. So an alert mind will ensure that good fibers do not end up as waste while removing the short fibers. At the same time by looking at the web, coming out of comber he needs to be smart enough to assure that the quality is maintained. Also, there should not be any piece mark that results in unevenness in the yarn. This particularly is to be taken care of, as it is an intermittent process where fringe by fringe is combed.
Similarly, by looking at the card web, we must check the number of neps forming in the process. So all the counts of faults like neps, thick place, thin place etc ultimately affect the yarn quality as they are measured in the final product.
If we take a screenshot of the Indian textile industry, in many units we will see that most of the manpower learns on the job with their experience or through the instructions given by the supervisor or the textile engineers. They are spoon-fed of how to do it, what to do etc without making them aware of the causes thus a new problem in the batch remains undetectable on many occasions. They are taught only to take care of the operations.
As we know the major emphasis in our country is on productions, hence the finer things may not be trained to the workers. Another role done by Werner international is believe in a time and motion study. Wherein they handle a list of operations to be performed by the workers instead of providing a particular set of machines for them to work on. This ensures that the skills of the workers are utilized to his full efficiency. Such training manuals prepared by the renowned international players need to be followed by the Indian textile industry to ensure optimal utilization of the skill manpower resource.
In the post spinning process, there is winding, assembly winder & TFO for double yarn process. This department also needs highly trained workers like the ring frame department. In this department also there is a gap as far as trained manpower is concerned as many times the available manpower is used & while operating the department they learn and adapt. So a proper pre-job training and monitoring of the process are the necessity for the growth of this segment of the industry.
In the knitting industry, most of the work is done by the machine itself. Especially in the case of the state of the art machine the knitting operator needs to have very good eyesight. He must be efficient enough to understand if anything is going wrong by looking at the fabric in the process. Also, another physical attribute needed for the operator is a good height is the creel is on top of the machine. The Skillset of mending for the packages is necessary not of high degree but the good observer is the criteria while selecting the workforce in this department.
In Weaving, highly skilled people are required for the ones working on looms. In the case of warping & sizing the skills can be learnt on the job while working on the machines. Nowadays the weaving industry utilizes high-speed machines like shuttles looms. So a worker with proper logical reasoning & analytical mindset is preferred. As he needs to understand how to handle the breaks of the machines & effectively resolve the issues. He needs to be alert on faults occurring at the backend of machines as most of the time the worker will be in between aisles monitoring the process and may not be able to see back side of the machine. Even though most of the machines have built-in signals for machine errors, an alert & cautious worker will be able to attend & resolve the issue without major delay in the system. Few agencies provide this type of specialized training. Many organizations are carrying out this training in-house for new entrants. Incorporating the feature of owning the operation is what is needed for brushing the skillsets of people involved in this segment.
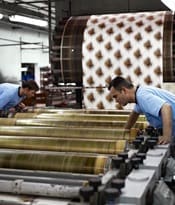
Figure 2Finishing process, source internet
In the case of finishing, the people are working are chemist with the common traits like good eyesight with a superior color differentiating ability. This helps in understanding the deviations such as color or shade change, change in the quality of the dye or print produced, etc. All of this also demands good observation skills. At the same time as the entire process is chemistry, they should be thorough on the knowledge of dye & its impact on various color combinations. Many units do not have sampling machines in the setup, hence the skills of masters in dye or printing are what is relied on. These masters are trained while on the job with the years of experience as their greatest teacher.
Most people learn while on the job, make changes to the procedures, develop skills, and evolve themselves as masters by creating their own best methodologies to follow. This learning & adapting to the job is a phenomenon that will be seen across all segments of textiles. Though there is indeed no greater teacher than experience. It is also necessary that some skills are to be trained for increasing the efficiency of these self-learning people thereby ensuring much better results.
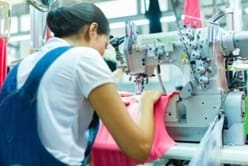
Figure 3: Garment Factory, source internet
The largest stage for conventional textiles is Apparels, where the stitching process is where the most skilled workers are needed. Here we will find that highly accurate and long working hours are the demands of the job. So a person with high patience is needed. It is observed that many mills prefer women for this department due to its specific skill requirements like efficiency & high patience, quality checking, good eye sights so a bit of multitasking is the need for this job. Also, part of this job like sewing is mostly learned by the ladies since childhood as part of our culture. This stage also needs the workers to continuously monitor a few mm of garment that they are stitching and keep the work going without gaps in between. As it is a continuous chain where time & quality is the major factor involved. This last part of zero time breaks is where the focus of the apparel industry should be today. Because when compared to the International markets our people are not trained for giving such high efficiency. The other factor affecting our efficiency is the shortcomings of consistency. Our workforce though is multitalented where the same person is involved in stitching various parts of designs as per the production demand we fall short of reaching the 100% efficiency for a single product as the person’s practice is diverted when a new part with a different type of stitch or design comes to picture. So training is a must for the new set of people joining. Another issue is the finding new replacement of the workforce as it involves ladies. Many of the times after marriage the girls are moving to new locations or household problems that increase the absenteeism thereby affecting the production levels. So training & brushing skills for high efficiency to compete internationally is a must in this segment.
When it comes to technical textiles, very few units currently are present but we are growing in this segment. This segment is where highly educated people are needed with analytic minds for understanding the machine signals. The person also requires good readability &understanding of the English language as it is the display language on machines software & thereby must make plans of machine cycles accordingly. Usually, entrepreneurs send key people abroad before bringing machines also few people have learned about the new machines while working on them and adapted efficiently to the changing times.
Conclusion
There is a wide gap as far as training needs are concerned. We need to have classroom training & shop floor training. There is already a global market evolved containing the methodologies that are developed for the best practices. Also, many renowned agencies are equipped in bridging this gap of trained skilled workforce. It is time to adopt the tools available to upgrade the training systems. A continuous training must be incorporated in day to day practices. We need to bring these training models to academic practices so that they learn new technologies and processes evolving. A syllabus reconfiguration is needed every 2 years or at least live projects are to be part of the curriculum for developing the youth of textiles. These are the small yet significant steps that will help us regain a position of being the strong competitor from the current image of distant number 2 players.
Let us practice the art of training….
For the dominance in the textile world tomorrow!!!
By Mr. Avinash Mayekar, MD & CEO,
Suvin Advisors Pvt. Ltd.