From Portugal to Pakistan, top-tier knitted fabric manufacturers rely on Monforts MONTEX stenters for precise and automated fabric handling, ensuring superior drying and finishing processes.
Advanced Solutions for Knitted Fabrics
“Knitted fabrics require delicate handling due to their higher elasticity compared to woven materials,” explains Monforts Marketing Manager, Nicole Croonenbroek. “Our MONTEX stenters provide smooth treatment at precisely controlled tension levels during all processing stages. Additionally, they offer gentle and uniform thermal treatment while significantly optimizing energy consumption.”
ATB: Europe’s Leader in Dyeing and Finishing
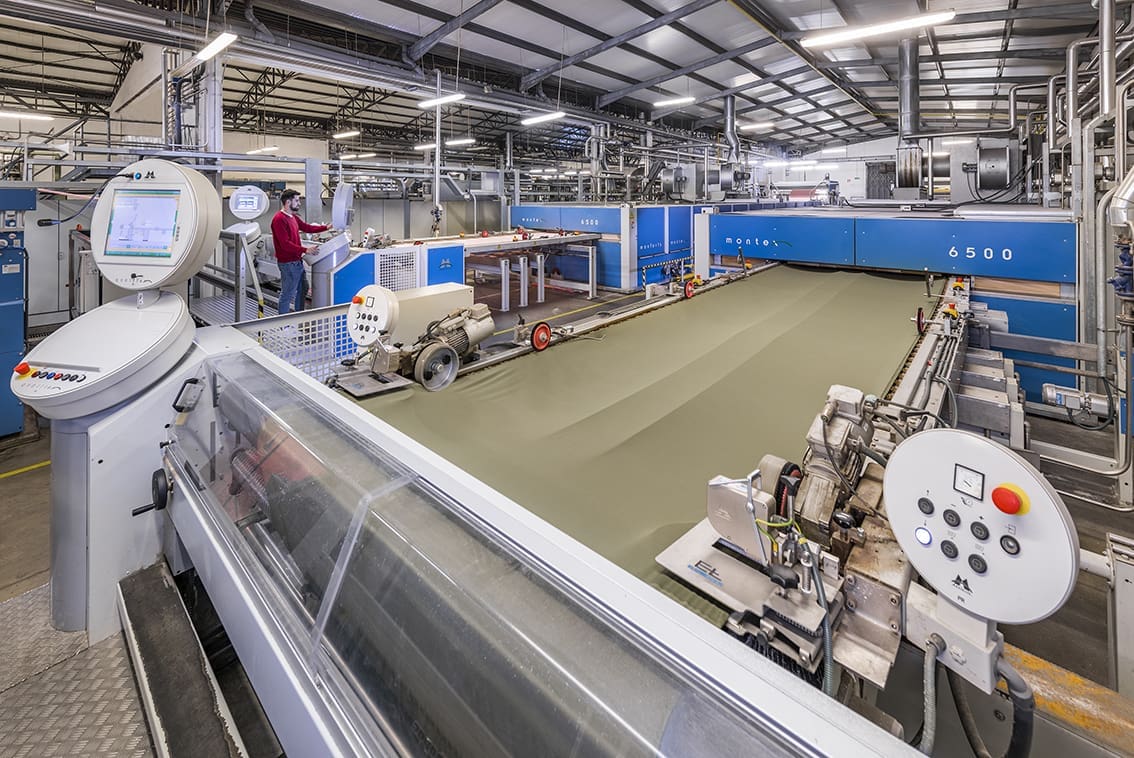
ATB’s finishing plant is extensively equipped with Monforts equipment.
ATB – Acabamentos Têxteis de Barcelos, one of the largest dyeing and finishing companies in Europe, processes between 36-40 tons of fabric daily for leading global brands, including Benetton, Inditex, and Mango.
Having installed its first Monforts MONTEX stenter in 1990, ATB has since added four more, all 2.8 meters wide and equipped with heat recovery units for enhanced energy efficiency. The company also utilizes two Monforts Dynair relaxation dryers and one EcoApplicator to ensure high process quality and reproducibility.
In 2024, Etevimol, ATB’s knitting subsidiary, became fully owned by the Mano family, prompting a strategic relocation of its 160 knitting machines to the ATB plant. A €5 million investment in new knitting machines is also underway.
“Our customers need fabric samples quickly, so we maintain an extensive fabric library with over 10,000 samples,” says ATB CEO Ricardo Mano. “We also test our fabrics in finished garments to anticipate customer needs with the support of our advanced technology suppliers like Monforts.”
Interloop’s Ambitious Expansion in Pakistan
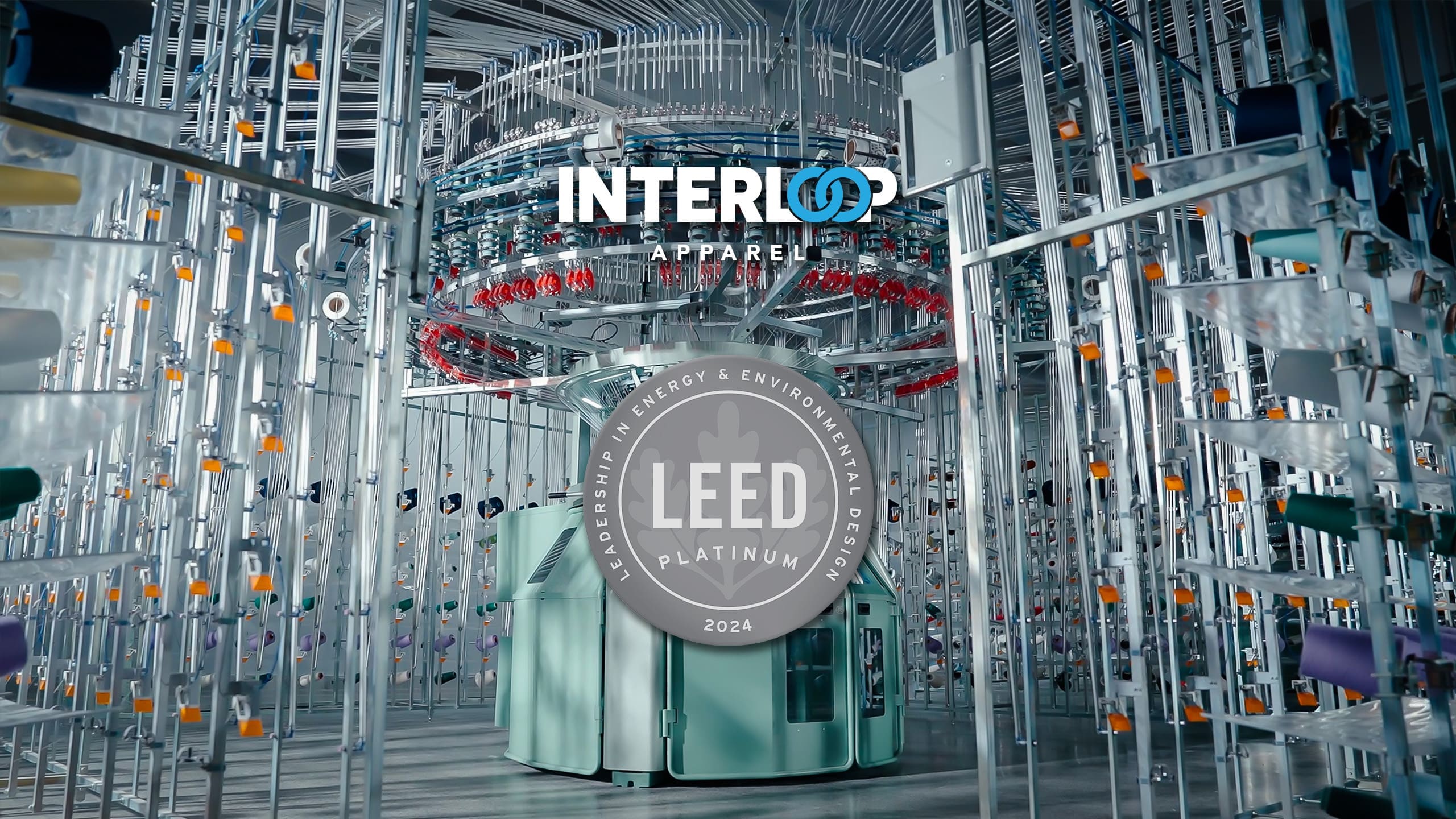
Interloop’s latest fully-integrated knitwear plant in Faisalabad, Pakistan, is equipped to produce fifty tons of knitted and dyed fabrics on a daily basis. Image coutesy of Interloop.
Interloop, one of Pakistan’s largest publicly listed textile firms, began operations in 1992 with just ten knitting machines for hosiery production. Today, the company is poised to achieve $700 million in annual sales by 2026, supplying renowned brands such as Adidas, H&M, Nike, and Target.
Interloop’s newest state-of-the-art knitwear facility in Faisalabad is designed to produce 50 tons of knitted and dyed fabrics daily, supporting an annual output of 45 million finished garments. Spanning 1.25 million square feet, this facility is Interloop’s most technologically advanced yet, achieving the highest LEED certification score for a facility of its scale. It incorporates renewable energy solutions, including biomass boilers, and advanced water and effluent management systems.
“We are setting new industry benchmarks by embracing innovative technologies and continuous process improvements,” says Interloop CEO Navid Fazil. “With our LEED-certified infrastructure, self-sustaining green energy grid, and transition to biomass fuel, we are expanding our sustainability efforts on an unprecedented scale.”
Unmatched Reliability and Performance
“Monforts MONTEX stenters have set the industry standard in fabric finishing, offering knitwear manufacturers precise control, sensitive handling, high production throughput, and exceptional energy efficiency,” concludes Nicole Croonenbroek. “Our machines stand out for their robustness, long service life, and strong customer support built on four key principles – helpfulness, accuracy, speed, and reliability.”