In the last two decades Textile Industries have observed tremendous changes in the field of product safety and environmental awareness. In the other words Textile Industries globally is passing through a very challenging phase. All these challenges are real and perceived environmental risk, pressure from retailers, NGOs and even from legislation.
In the middle of 2011 Greenpeace published “Dirty Laundry” -study report on release of hazardous chemicals by the textile industries in China. As a part of the investigations, Greenpeace also uncovered links between these polluting facilities and a number of major clothing, fashion and sportswear brands.
All major brands and retailers took this very positively and came up with plan to phase out top priority eleven hazardous chemicals from supply chain by 2020. H&M, C&A, Nike, Adidas, Li Ning and Puma joined hands together and formed group to execute their commitment on Road to Zero discharge and named this group as Zero Discharge of Hazardous Chemicals (ZDHC).
These new developments in global textile supply chain bring huge challenges for Dyes and Chemicals manufacturers thus created lot many opportunities for responsible manufacturers.
In general, dyes and chemical manufacturers need to ensure that their products complies with the requirements of the eleven priority chemicals. All textile processers also need to ensure that they do not intentionally use any of the eleven priority chemicals in their processing and will phase out from their factory premises. Additionally, they also need to ensure reduction in water consumption, waste water generation, waste generation and conservation of resources,
We are approaching the deadline of 2020 and in the meantime the NGO has acknowledged significant progress in The Roadmap to Zero program. In the last couple of years more brands and retailers joined the program and in the meantime this group also shaped up formally and registered as The ZDHC Foundation as nonprofit organization in Amsterdam. Slowly and steadily this ZDHC foundation is becoming well established common platform for whole textile supply chain having total 165 contributors including 30 brands, 114 value chain affiliates and 21 associates. ZDHC decided to take its program to another level and in January 2020 they launched The Roadmap to Zero program emphasizing on Safer Input Chemicals, Smarter Processes and Better Outputs.
For safer chemical inputs ZDHC developed Chemical Gateway with clear classification of chemicals in four different levels. By end of 2020 year ZDHC is going to phase out level 0 (self-declaration) and all their contributors need to ensure minimum Level-1 compliance. Additionally, ZDHC also updated its MRSL for chemical manufacturers and published version 2.0 which include some additional hazardous chemicals in addition to initial eleven priority chemicals. One year transition period is given to chemical manufacturers and suppliers to ensure compliance with ZDHC MRSL V.2. This will help to ensure phasing out of hazardous chemicals from supply chain. In December 2019 along with MRSL V.2, ZDHC also published candidate list which include potential chemicals list which may get included in Version 3 depending upon further evidential proof from their lifecycle assessment on their hazardous character.
Smarter Process is crucial link between inputs and outputs. Safer inputs make a big difference, as long as they are used in the right way, when good procedures and best practice are in place, outputs become cleaner and better. ZDHC provides practical help, guidance, training and support to the suppliers on best available technologies and procedures.
For ensuring better out puts ZDHC measures indicators like wastewater quality, sludge quality, or air emissions. Outputs help to validate the good work that’s being done with inputs and processes.
Being Responsible Care Company Colourtex always promote best practices and processes suitable for sustainable future. Hence we very well understand the responsibility to contribute in providing solution to our customers for minimizing the environmental impact in textile processing. Colourtex has been always focusing on introducing new products & processes to provide sustainable solutions to our valued customers.
To provide right solutions for such newer challenges in the field of safer chemicals and processes, Colourtex developed Sustainable Product Ranges in Reactive Dyes and Disperse Dyes which are based on the best available technology in the global textile dyestuff industry. These innovative product ranges are completely in compliance of ZDHC MRSL v.2 and fastness requirement of retailers while minimizing the overall impact on environment and ecology. Ultimately, providing right sustainable solution for our valued customers and textile industries in total.
Cora CARE EF:
Innovative Reactive dyes range for sustainable processing of Cotton & blends
- Reactive dyes free from all banned amines (inluding p-CA free Navy & Black)
- Incompliance with heavy metal requirements of ZDHC MRSL V.2
- Incompliance with all relevant requirements of Restricted Substance List
- Have high fixation and easy wash-off properties which helps in shortening of dyeing cycle and reduction in water consumtion and waste generation.
- Good wet fastness properties
Coralene HP:
Second generation high wash fast disperse dyes range for Polyester & blends
- Disperse Dyes free from all banned amines
- High wash fast disperse dyes
- Incompliance with all relevant requirements of Restricted Substance List
- Elimination of intermediate reduction clearing helps in shortening of dyeing cycle for polyester/cotton blends and reduction in water consumption and waste generation.
- Full range with all gamot of shades available
CoraCARE EF: New reactive dyes product range designed and developed by Colourtex is fully in compliance of ZDHC MRSL V.2 and also having patential for significant resource saving thus providing sustainable solution to the textile processing house.
FEATURES AND BENEFITS OF CoraCARE EF range:-
FEATURES OF PRODUCT RANGE | BENEFITS TO CUSTOMERS |
Reactive dyestuff range free from all banned amines (including p-CA free Black and Navy) & Heavy metals | Ecologically viable to promote/ work for special brands following Detox 2020 & ZDHC.Increase in brand value for processors |
Fast fixation dyestuff | Reduction in process cycle and can increase productivity.Saving of energy due to short dyeing cycleSuitable for both exhaust and continuos application |
Less substantivity of hydrolyzed dye | Easy washing off at low temperature resulting shortening of washing cycle and increase in productivity.Saving of Energy & WaterBetter Fastness |
Other features useful for application | DischargeableLow salt dyeable resulting in low load on effluent |
In the processing of 100% Cotton and regenerated cellulose, CoraCARE EF range of reactives dyes provides very robust application profile with the unique properties with high fixation and easy wash-off, this range helps in shortening the dyeing cycle compared to conventional process. Robustness of the range facilitates good lab to bulk and bulk to bulk reproducibility compared to conventional reactives even with the minor changes in application parameters including water quality.
CoraCARE EF process for deep shades on Cotton:
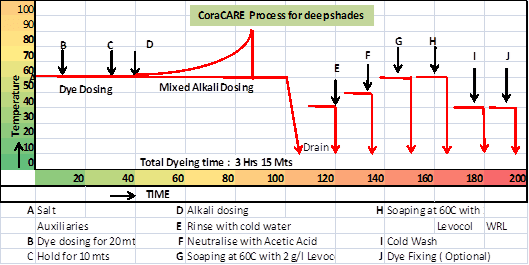
Conventional dyeing and wash off process for deep shades on cotton:
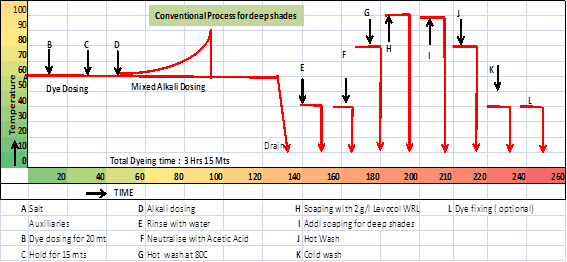
Advantages with CoraCARE EF range/ process over conventional dyeing process:
- 30-40% saving in water
- 20-23% saving in dyeing cycle
- 10-15% saving in energy
- Dyed Fabric is free from all rstricted substances.
With the increase in use of Polyester microfibre, also the demand for special chemical finishes for the dyed fabric and the boom in elastane containing fabrics, the demand for high wash fastness disperse dyes has been growing much faster than the growth rate of polyester itself. Leading retailer brands especially the sportwear suppliers are the driving force behind this demand. Colourtex initially introduced Coralene XF dyes as the first offer meeting this requirement and continued its efforts to overcome certain limitations of Coralene XF range and introduced Coralene HP range. This second generation high wash fastness disperse dyes range meets the stringent wet fastness requirements of retailers while helping the dyer to shorten the process therby saving in energy, water and chemicals.
Exhaust Dyeing of Polyester/Cotton Blend:
With the increase in trend of polyester/Cotton blends due to various reasons like new developments in polyester ( microfibre), shortage & higher cost of cotton etc. the processing sector faces more challenges. In addition to difficulty in achieving stringent wet fastness properties, conventional long process cycles reduces the productivity in the mill. Colourtex closely working with trend setters in the textile processing sector to address these issues and developed shorter dyeing cycles using the unique properties of these two innovative ranges in reactives and disperse dyes.
Polyester/cotton blend dyeing in single bath-two stages can be more beneficial by removing intermediate reduction clearing process using Coralene HP dyestuff and subsequently cotton dyeing with CoraCARE EF can reduce dyeing time,water and energy
Conventional exhaust process for PES/CO Blends:
In the conentional exahust dyeing process for Polyester/Cotton blends in medium/deep shades, after dyeing the polyester part at high temp( 130°C), for achieving the fastness properties, the fabric is subjected to reduction clearing with 2 g/l Caustic Soda and 2 g/l Sodium Hydrosulphite at 80°C for 20 minutes followed by hot wash, neutralising and cold wash. Following this the cotton portion is dyed with Reactive dyes as per the normal process which includes minimum seven wash baths of which at least two are at boil and two at 80°C respectively.
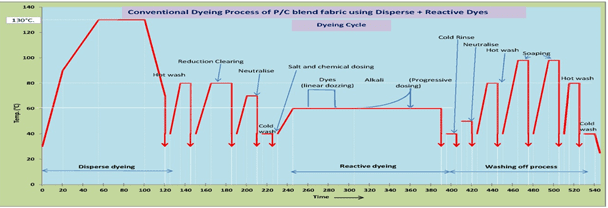
Innovative process with Coralene HP & Cora CARE EF for PES/CO Blends:
In the innovative process developed and estabilshed with Coralene HP & Cora CARE EF range, the reduction clearing step and related three wash baths are eliminated. Similarly, the after treatment baths after the Cotton dyeing are at 60°C and limited to maximum five baths as per the details illustrated in the fig 3 & 4 below. The unique chemistry of Coralene HP dyes facilitates alkaline clearing during the alkali fixation of Reactive dyes. Similarly the low substativity of the hydrolysed part of the Cora CARE EF dyes helps in comparatively easy wash off process while achieving comparable wet fastness properties.Further, with the shortening of the whole dyeing cycle with the unique process, mill productivity increases while saving in precious resources like water and energy.

Benefits over conventional exhaust process for PES/CO dyeing:
- 30 % saving in water
- 25 % saving in energy
- 30 % Higher mill productivity with shortening of dyeing cycle
- Dyed fabric free from all restricted substance under regulatory as well as ZDHC.
Continuous Dyeing of Polyester/Cotton Blend:
Conventional process:
In the case of conventional continuous dyeing process of polyester/cotton blends with disperse & reactive dyes, the polyster portion is dyed first by thermofixation at 210C followed by reduction clearing and after treatment.. Fabric needs to be dried before commencing the dyeing of the cotton portion either by pad-dry-chemical pad-steam or cold-pad-batch process. This slows down the production in the unit and also increases the cost due to number of additional process steps including intermediate drying.
Innovative process with Coralene HP dyes
The innovative process with Coralene HP range helps the dyer to complete the dyeing in one continuous pass avoiding the intermediate reduction clearing & drying as per the illustration below. As in the case of exhaust dyeing, the unique property of Coralene HP dyes range facilitates the alkaline clearing during the alkali fixation of the reactive dyeing during steaming thereby achieving comparable wet fastness properties.

In this process, Coralene HP disperse dyes and CoraCARE EF/Coralite FL range of reactive dyes are padded together, dried and thermofix for the disperse dyes before padding through Alkali for the fixation by steaming of reactive dyes. This process helps the dyer to almost double the production in the unit compared to the conventional process and also substantial saving in water ( almost 50%) and energy which minimises the impact on the envronment.