By ITMA Organiser, 8 Jan 2024
In today’s fast-moving textile industry, the technologies enabling the creation of advanced materials are allowing greater control for designers through digitalisation, enabling more recycled content to be accommodated in fabrics and making enhanced performance properties for demanding applications possible.
Design control
Designers, for example, are now able to simply and precisely conceptualise luxurious fabrics with intricate patterns knitted into their structures – while eliminating any need for fabric printing or dyeing – using the latest AlterKnit technology of Taiwan’s Pailung.
AlterKnit enables alternate yarns of different colour or composition to be paired together within the same rows and yields crisp patterns with sharp borders. It can capture the intricate details of a sports team emblem, for example, including text and logos, and is also reversible, producing two inverted versions of the same design in up to four colours on either side.
When designing for sportswear, different types of yarn can be combined to create functional fabrics with enhanced features, such as moisture-wicking, breathability, elasticity etc. And progress from initial design to final product is fully automatic.
Recycled cotton content
For yarn spinners, the inclusion of recycled fibres in conventional spinning is currently not an easy task, although customers of Swiss leader in spinning technologies Rieter have been processing their own pre-consumer yarn waste for decades on the company’s rotor machines.
Rotor spinning is best suited for processing yarns with a high short-fibre content but there is also now an increasing demand for recycled ring and compact yarns which need a higher tenacity to go into weaving, with fibre counts for soft touch fabrics the goal. This, however, is very difficult due to the neps and high short fibre content.
Nevertheless, in partnership with Spanish fibre recycling specialist Recover and Portuguese spinner and textile manufacturer Polopiqué, Rieter has recently successfully demonstrated a high-quality Ne 30 compact yarn that contains an impressive 40% recycled post-industrial fabric waste, and progress continues.
Recycled polyester
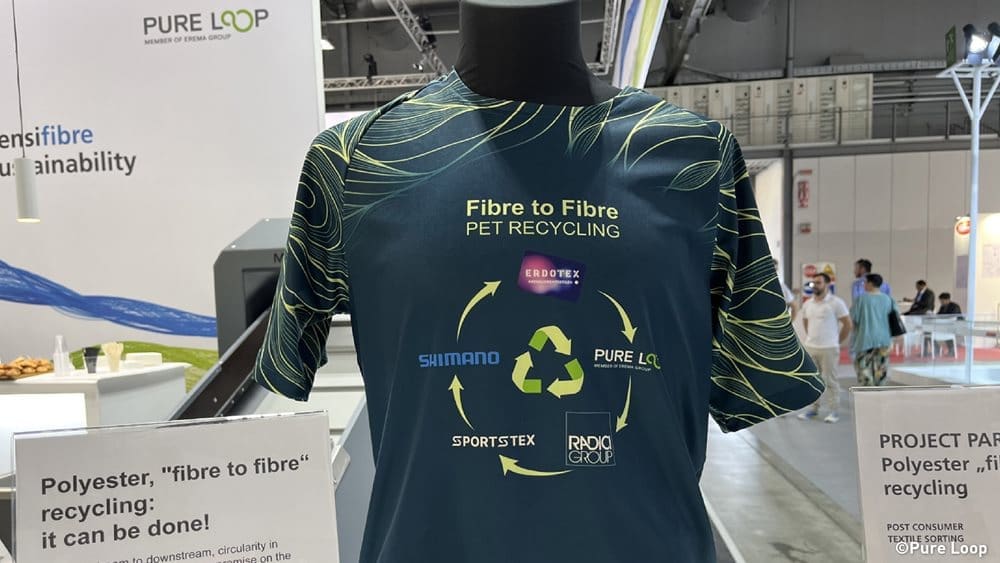
Closed loop garment production from recycled polyester has meanwhile been demonstrated by Pure Loop, a subsidiary of Austria’s Erema Group, in a partnership with fibre leader RadiciGroup, sportswear manufacturer Sportstex and cycling brand Shimano.
Via a gradually fine-tuned process to develop a yarn that is 100% derived from recovered textile waste, a Shimano cycling shirt has now been produced with exactly the same performance properties as a shirt made from virgin polyester.
High performance
Beyond the apparel sector, textiles are also employed in many technical applications, such as braided composite reinforcements. Here they are enabling the lightweighting of trains and boats and planes and much and much more, and millions of tons of CO2 emissions are being eliminated as a consequence.
The braiding technologies of Germany’s Herzog, for example, are widely employed in the creation of near-net shape carbon fibre composite preforms – 3D textile structures as close to the shape of the final finished component as possible.
Two other key growth areas for braided textiles are in ropes and medical products.
The ability to replace steel with high strength fibres such as aramids, Dyneema and Vectran has resulted in ropes that have 75% less weight with all of the advantages that bring in terms of towing, mooring, anchoring and lifting and lowering. In addition, ropes made from these fibres have ten times the working life of steel equivalents.
In medical products such as sutures, artificial ligaments and stents, braided fabrics are increasingly the preferred choice for their flexibility in terms of the customised shapes and patterns that can be achieved and the specialised fibres that can be accommodated.