ST. LOUIS — March 10, 2021 — Baldwin Technology Company Inc. invites plastic film extruders to a free webinar on how to improve safety, automation and productivity in cast film extrusion, plastic sheet extrusion and blown film extrusion. The one-hour live educational session is offered twice on March 23, and registration is free: March 23 at 6 a.m. Eastern Daylight Time (US) / 11 a.m. Central European Time (Europe) / 6 p.m. China Standard Time (Asia) and March 23 at 11 a.m. Eastern Daylight Time (US) / 4 p.m. Central European Time (Europe) / 11 p.m. China Standard Time (Asia). Those who cannot attend live, but who have registered, will receive a recording of the webinar afterward.
Events Updates | News & Insights
Baldwin hosts free webinar on how to improve safety, automation and productivity in film extrusion
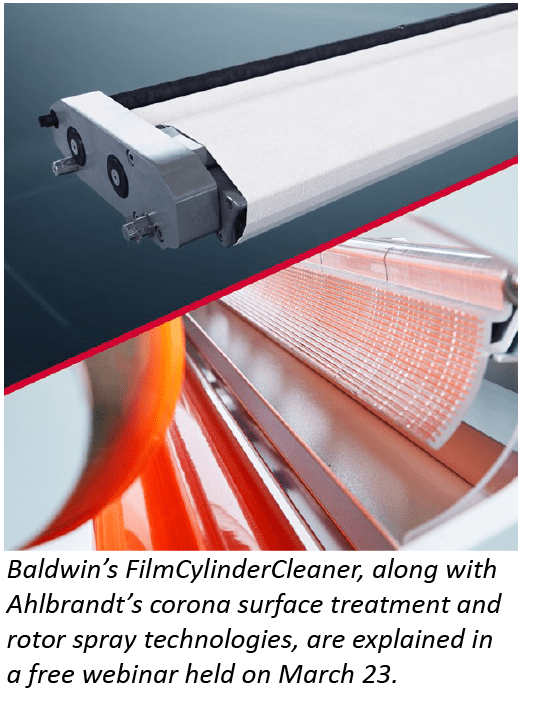
Published: March 11, 2021
Author: Manali bhanushali
During this forum, Baldwin experts will review downtime issues and other barriers within the plastic film extrusion process, and discuss reducing hazards and improving production quality. They also will share recent examples and innovations in surface cleaning and treatment technologies.
Extruders seeking to increase safety and eliminate the 30-to-60 minute process of manually cleaning chill rolls will have the opportunity to learn more about Baldwin’s automated FilmCylinderCleaner. This proven, highly efficient system cleans cast and chill rolls in minutes during operation, maximizing uptime, while enhancing film quality and saving material costs.
“Until now, surface cleaning has been a manual process. Besides the difficulties in accessing the chill rolls, manual cleaning also is uneven and hazardous,” said Matthias Knoch, Sales Director of Industrial Applications at Baldwin. “With our innovative FilmCylinderCleaner, extruders get a smart, automated cleaning system, so they can clean ‘on the go’ with consistent quality, gaining up to 250 extra production hours per year.”
Additional innovation topics include the highly energy efficient corona surface treatment systems from Ahlbrandt, a Baldwin company, as well as Ahlbrandt’s non-contact rotor spray systems. The innovatively designed corona surface treatment technology features top-performing, easily accessed electrodes, ensuring maximum efficiency and surface tension. Ahlbrandt’s rotor spray systems save both chemistry and energy consumption, while providing an even and precise coating with long-term anti-fog properties and release for demolding thermoformed parts.
“Surface treatment is not an option in film extrusion—it is a requirement for downstream converting of polypropylene (PP) and polyethylene (PE) film in printing, laminating and anti-fog coating processes,” said Alexander Rau, Product Manager at Ahlbrandt. “With our technology breakthroughs in corona and rotor spray technologies, extruders will experience increased productivity and decreased downtime.”
Related Posts