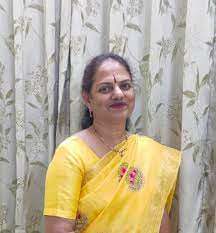
Sudha Babel
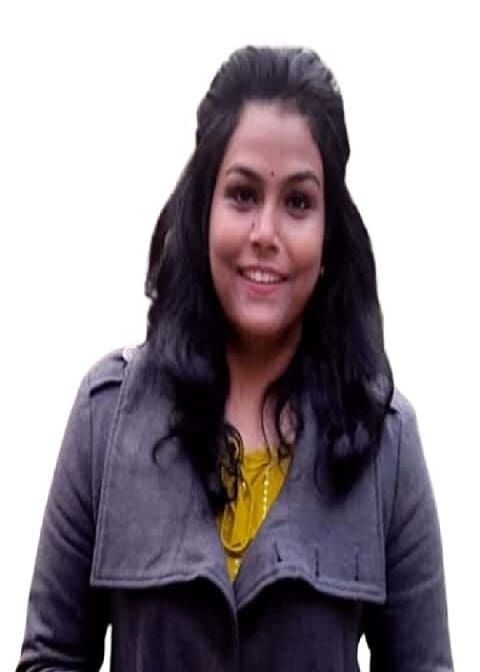
Iti Dubey
College of community and applied sciences, Maharana Pratap University of Agriculture and Technology, Udaipur, Rajasthan
Introduction
The term “digital printing” also applies to inkjet printing. In the markets for desktop and network printing, it has emerged as the dominant printing technology. Wide-format graphic arts and increasingly industrial applications like textiles, which until recently were the sole realm of conventional analog printing technologies, are just a few of the new application fields for ink jet printing that have been made possible by the arrival of digital color printing.
When using an ink jet printer, only the individual ink droplets come into touch with the substrate because there is no printing master involved. Consequently, it is categorized as a non-impact printing technique.
INKJET PRINTER COMPONENTS
Three fundamental parts make up ink jet technology. To produce an output that is suitable, the print head, the ink, and the medium must all function properly.
INKJET TECHNOLOGIES
There are 2 types of inkjet technologies.
- CIJ (Continuous ink jet)
- DOD (Drop on demand).
- CONTINUOS INKJET TECHNOLOGY
In CIJ, ink is squirted via nozzles at a constant pace while using a constant amount of pressure. Depending on the picture being printed, the ink jet is unstable and breaks into droplets as it exits the nozzle. The droplets are either let to fall into the medium or are diverted to a gutter for recirculation. Typically, the drops are electrically charged before the deflection is applied, and the drops’ trajectory is controlled by an electric field. Due to the constant ejection of drips, the term “continuous” was coined.
- DROP ON DEMAND TECHNOLOGY
Drops are only discharged in a DOD ink jet when they are required to create an image. Thermal ink jet (TIJ) and piezoelectric ink jet (PIJ) are the two primary drop ejector technologies used to produce droplets (TIJ)
In PIJ, a piezoelectric actuator rapidly reduces the volume of an ink chamber inside the nozzle to squeeze the ink droplet out of the nozzle. The ink is heated in TIJ to the temperature necessary for bubble nucleation using an electrical heater housed inside each nozzle. The ink is propelled outside the nozzle by the vapour bubble’s explosive growth.
Any ink jet-based technique for printing colourants into fabric is referred to as digital textile printing. Specifically, the term “digital textile printing” refers to the process of printing either smaller graphics directly onto clothing (such as T-shirts, dresses, or promotional wear; abbreviated as “DTG” for “Direct to Garment”) or bigger designs directly onto large-format rolls of material. This latter practise is a developing trend in visual communication, where commercials and company branding are printed on polyester medium. Flags, banners, signage, and retail designs are a few examples.
Types of printing can be divided into:
- Direct Print
- Discharge Print
- Resist Print
- Pigment Print
- Reactive Print
- Acid print
- disperse print
- Specialty Print
In an effort to replace analogue screen printing, digital textile printing first appeared in the late 1980s. It was feasible to print with low energy sublimation inks and high energy disperse direct inks directly onto textile media thanks to the invention of a dye-sublimation printer in the early 1990s, as opposed to printing with dye-sublimation inks on transfer paper and then transferring them to fabric separately using a heat press.
PRODUCTION REQUIRMENT:
The “textile market” includes a wide range of needs and uses. The most crucial place to start when determining precisely what is required to create a given final result is with the fabric’s intended usage. A “textile” product can range from natural yarns for clothing to synthetic fibres for flags and banners.A “textile product” can be a beach flag, national flag, company flag, stand-alone pop-up banner, wall-mounted banner, etc. It can be many different things, such as a bed cover, backlit frame, curtain, room divider, building wrap, or clothing.
.How digital textile printing improves production processes:
The newest advancement in the textile business is digital textile printing. It enables printers to satisfy customers’ requests for high-quality designs, small runs, and quick turnaround times.
Additionally, its quick sampling and quick delivery enable clients to market new ideas more quickly. Designs can instantly be changed digitally while printing digitally. This gives digital printing businesses a competitive edge over businesses that use traditional printing methods.
Benefits of digital textile printing:
- Low beginning costs as individual patterns do not require the engraving of screens; high resolution, delicate patterns, and limitless colour combinations.
- A sustainable solution that uses less ink and saves a lot of electricity and water.
- Unlimited repetition size because it is not constrained to the rotating screen’s circle.
Evolution and progression of digital printing of textiles
Digital printing on textiles is not a new concept. The first patent for the inkjet printing technique used in digital printing was issued in 1968. Since the early 1970s, carpet inkjet printing machines have been in use. At ITMA in 1995, continuous rolls of textile fabric printed with digital ink jet technology were displayed. Inkjet printers for paper printing applications became increasingly accessible in the 1990s. A number of industrial inkjet printers were once more unveiled at ITMA in 2003, establishing the new industry standard for digital printing on textiles.
The history involves the following series of inkjet printers;
- FESPA 1996
- FESPA and ITMA 1999
- ITMA 1999
- DPI 2001
- ITMA 2003
- Drupa 2004
- SGIA 2004
- FESPA 2005
There are several different print head technologies used in ink jet printing, and each has unique physical and chemical requirements that must be met for the ink formulation to function dependably in that platform.
Fabric pretreatment is a step in the digital printing process before printing. Because adding auxiliary chemicals and thickeners to the low viscosity ink has proven problematic, pre-treatment of textiles is done in order to prepare them for ink-jet printing.
Reactive dyes and pigments are often the options when printing on cotton. The pigment printing process is less complicated than reactive printing because it only has two additional steps (print, dry, and bake/cure) (print, dry, steam, wash-off, dry).
REASONS FOR PRE-TREATMENT
The following are the main justifications for applying the dye ink and other chemicals individually to the fabric instead of mixing them together.
- ‘All-in’ inks are less stable and have poorer storage stability, for example, reactive dyes are more likely to hydrolyze when the ink contains alkali.
- Chemicals in the ink corrode jet nozzles; for example, sodium chloride has a bad effect on steel surfaces.
- Inks used in continuous printers that print “charged drops” should have a low electrical conductivity.
- Ink thickeners frequently lack the desired rheological qualities.
- Some chemicals are allowed for use in pre-treated cloth but would have stability issues in ink. For example, sodium carbonate is permitted as an alkali for reactive dye fixation on fabric but not in ink.
COMPARISON BETWEEN CONVENTIONAL SCREEN PRINTING AND DIGITAL PRINTING
Comparable Factors | Screen Printing | Digital Printing |
Tools | The process involves making a stencil using a drawn/digitized image or a photograph, attaching to a screen, placing it over the desired canvas and spreading the ink over the image. | All need is a computer and a printer with ink cartridges of every color. |
Efforts | Takes a lot of time consuming effort, because the screens need to be made and the process takes long | As it is so easy to operate and gives results at the touch of a key. It is relatively quicker. |
Quality | Offers better quality imaging as the ink gets deeply absorbed and lasts longer. Screen printing also gives clearer edges to the image printing, because of the precision that carefully created stencils offer. | The ink does not spread because the image is directly printed on the fabric, but tends to fade quicker that the screen printed images. However, person has a colorful image to imprint, then this is an option, all the colors are present in the single image and person does not need separate screen for the same. |
Cost | Costs escalate with the numbers of screens. If person want a more complex image with many colors, then individual slides for every color are created. It also required trained labor which adds to the cost. It is most apt if person want a large quantity. | The computer and printers are one time investments and digital printing is cheaper compared to screen printing as the charge is offer for per imprinted image. |
ADVANTAGES OF INKJET PRINTING
The manner that firms produce their printed documents has been transformed by digital printing. In contrast to the more conventional process of textile printing, it is quick, efficient, and available.
- Quality: Digital printing offers the highest quality available. Alignment and registration difficulties don’t occur, and images are essentially error-free. Colors are also bright. The complete length of an item that can be printed can also be used by digital printers.
- Speed: Digital printing’s ability to switch over to a new label almost instantly is another perk of using digital printing. Your order is probably going to arrive at its intended location days, if not weeks, earlier because there isn’t any time lost setting up plates and printing equipment.
- Advantage of short runs: Without the need for screen changes, digital textile printing quickly creates designs for runs as little as one yard of fabric.
-
- Less water and energy are used in digital textile printing, which eliminates the need for a significant amount of water and electricity for rotary screen preparation, printing, and cleanup. Disperse/sublimation and pigment digital textile inks, which only need a heat-fixation step for post treatment, can save even more water and energy.
- Less chemical waste: Compared to screen printing, digital textile printing uses a lot less ink and produces a lot less waste. Digital printing is more environmentally friendly than screen printing when the added chemistry and chemical waste from screen manufacture are taken into consideration.
- Enormous repetition sizes: Instead of being constrained by the standard rotary screen-printing pattern repeat size, digital textile printers can print large designs (such as cartoon figures on sheets and blankets) on roll cloth.
- Reduced production space needs: Because digital printing does not require the preparation and storage of client screens for later use, the production footprint is much smaller than that of a rotary screen print facility.
- Less printed inventory is required since digital textile printing gives one the freedom to create a design whenever they want.
LIMITATIONS OF INKJET PRINTING
- Particle size restriction: These machines can’t print metallic hues because to the huge particle sizes.
- Large Volumes are Expensive: To avoid getting too technical, digital printing presses can only print at a maximum speed of roughly 50 feet per minute. While this speed is adequate for low-volume (10,000–15,000 item) projects, larger-volume work will benefit from the use of conventional presses that can operate at speeds between 300 and 500 feet per minute.
- Ink restrictions: While digital printing does a great job with colour and ink, digital inks have a tendency to fade more quickly than offset inks when placed in direct sunlight. Additionally, because digital ink is thinner by nature than offset ink, its opacity isn’t quite as high (though the difference between the two is only noticeable when dealing with clear or metallic media). To help avoid this issue from occuring, many lamination kinds are available.
CONCLUSION: The ability to mass customize products via digital printing allows for compliance with current market trends. It has been proven to be a reliable technology for producing samples. The principal impediment to the commercialization of technology, among other issues, is the printing process’ speed. The goal is to reach printing speeds that are practicable for businesses. To get printing speeds that are suitable for commerce, efforts are being done. Up until then, production will still be done using rotary screen printing in addition to digital printing for sampling.
REFERENCES:
-
- https://www.spgprints.com/digital-textile-printing
- https://www.spgprints.com/digital-textile-printing-machines
- https://textilelearner.blogspot.com/2017/03/digital-printing-textiles.html
- https://pdfs.semanticscholar.org/8f1d/162eb5578d300cb67f1057fa1b7b3bef3470.pdf
- https://en.wikipedia.org/wiki/Digital_textile_printing