Abstract
Viscose Rayon is one of the regenerated fibre manufactured from wood pulp as it has similar properties compared to cotton in terms of water-absorbing and comfort. It has gained popularity across the globe. Recycling, Reuse, and upcycling of the fiber are some of the essential parameters to be considered. These approaches help to establish a sustainable and green approach.
Introduction
Rayon is a Regenerated synthetic fiber produced from natural sources such as wood and agricultural products. It has a similar molecular structure to cellulose. Viscose can mean
- A viscous solution of cellulose
- A synonym of rayon
- A specific term for viscose rayon is because, rayon made using the viscose process
Many types and grades of viscose fibres and films are developed. Some fibres give the feel and texture of natural fibres such as silk, wool, cotton, and linen. The types that resemble silk are often called artificial silk. The fibre is used to make textiles for clothing and other purposes.
Rayon production involves solubilizing cellulose. One popular method involves the use of alkali and carbon sulphide. Rayon can also be manufactured by another method using ammonia solutions of copper salts. Alternately, the lyocell process, relies on a particular solvent.
Chemical Reaction Involved for Viscose Rayon Production
The cellulose is treated with a 17.5% of NaOH, which converts it into sodacellulose. The soda-cellulose with carbon disulphide react to form sodium cellulose xanthate. Sodium cellulose Xanthate is dissolved in dilute solution of caustic soda. It is extruded into sulphuric acid, which regenerates the cellulose now in the form of long filaments (Viscose rayon)
Cell-OH + NaOH Cell-ONa + H2O
Cell-ONa + CS2 Cell-O-CS-SNa (Sodium Cellulose Xanthate)
Cell-O-CS-SNa + H2SO4 Cell-OH + Na2SO4 + CS2 (3).
Production of Viscose rayon
Generally, Eucalyptus trees are used as a raw material for manufacturing viscose rayon. The flowchart of Viscose rayon manufacturing is given in Fig.1 below:
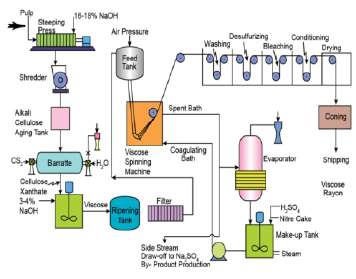
Fig. 1 Manufacturing process of Viscose rayon
Preparation of the wood pulp: a particular variety of woodViscose rayon is produced from . But wood contains lignin other than cellulose. For producing viscose rayon is by purifying cellulose from wood. Here the barks are removed, and wood is shredded into pieces and treated with Ca(HSO3)2. The treated chips are cooked with steam under pressure for 14 hours.
- Steeping and pressing: These prepared wood pulp contains 90 to 94% pure cellulose. First they are conditioned by storing in a room at controlled humidity and temperature. The pulp is then soaked in a 17.5% solution of NaOH for 1 to 4 hrs.
- Shredding: The shredding machine consists of a drum inside, which revolves around a pair of blades with serrated edges. In 2 or 3 hours they break it up into fine ‘crumbs’ (break into tiny pieces).
- Aging: After shredding, the crumbs are aged. They are placed in a galvanized vessel with a lid. Through oxidation with atmospheric oxygen, derivative changes set in. some depolymerization occurs, and the degree of polymerization drops from about 5000 to 350 in this process. The higher the temp. The more rapidly does aging.
- Churning: After aging, the soda cellulose crumbs are added into a rotating air-tight hexagonal churns. About 10% of their own (crumbs) weight of CS2 is added, and the crumbs and CS2. With a result, a result, a deep orange gelatinous sodium cellulose xanthate is formed.
- Mixing: The sodium cellulose xanthate is stirred with dilute caustic soda (NaOH) solution for 4 to 5 hours in the mixers. The vessel is cooled. The xanthate dissolves to a clear-brown viscous liquid appearance like honey. This liquid is known as viscose but is still too impure, too young to spin.
- Ripening: The sodium cellulose xanthate reacts with H2SO4 & forms regenerated cellulose. The viscose solution is stored for 4 to 5 days at 10-18°C, for ripening. At first the viscosity falls, then rises so that by the time the solution is ready to spin, the viscosity has nearly risen to its original value.
- Spinning: When the viscose is ripe, it can be fed in the spinneret of a spinning unit with additives to form Viscose (3).
Applications of Viscose Rayon
Viscose rayon is used in a multitude of applications
- Yarns – Embroidery thread, Chenille, Cord, Novelty yarns
- Fabrics- Crepe, Gabardine, Suiting Lace, Fur Coats, and Outer Wear
- Apparel – Blouses, Saree, Jackets, Sportswear, Curtains
- Domestic – Bed Spreads, Blankets, Draperies, Sheets Slip, Upholstery
- Industrial – High tenacity rayon is used to reinforce mechanical rubber goods (tires, conveyor belts, hoses) (4).
With such diverse applications, from casual wear to technical textiles, recycling is an important consideration.
Reason of Recycling
Recycling involves reuse, reprocessing, or reproducing a product with multiple aims of conserving raw materials, energy, water, and other chemicals, diminishing waste, preserving environmental impacts, and so on. Though it is beyond doubt that the reuse of any material will be very much beneficial in conserving various resources enlisted above, it will not be much applicable in the case of second-hand clothing due to limited practical applicability (5). Recycling brings ample benefits to both the environment and the economy (6). But unfortunately, it has a lot of barriers, such as financial, technological, educational, legal, and infrastructural barriers, which prevent textile recycling from being a successful option at the end-of-life stage (7).
Recycling textile fibers will aid in progress towards the sustainability of both products and processes (5). The importance of recycling reduces the load on landfills. If not recycled, the next destination could be a landfill, which is not desirable because it negatively impacts the environment (8).
Recycling of Viscose rayon
Viscose rayon market has increased tremendously in the past two decades, which was surveyed by the ministry of textiles around 13 %. It contributes to the global share recycling of viscose fiber helps reduce carbon footprints and develops a circular economy in future production.
Approaches in recycling Viscose Rayon
Bartl, A. (2005) stated that for recycling fibres a proper characterization method is required. Detailed knowledge of the fibre morphology makes it possible to evaluate potential applications. It is necessary to determine fibre length and width. Most of the literature on the recycling of fibres does not provide details about fibre characterization. However, characterization of short fibres such as recycled fibres is not an easy task. Due to their rather short length, standard methods for fibre characterization fail. But at the same time, due to their extreme nonspherical shape, established methods for particle characterization are not applicable (5). It has been demonstrated that a Mor Fi analyzer, which was developed for pulp characterization (9), is suitable for the characterization of short fibres originating from renewable resources. Characterising the fibres can be helpful to separate and identify helps recycle.
According to Karen S. Prado, during the manufacturing of Viscose rayon fabric, small fibres are wasted during the weaving process; these fibres can be used for recycling.
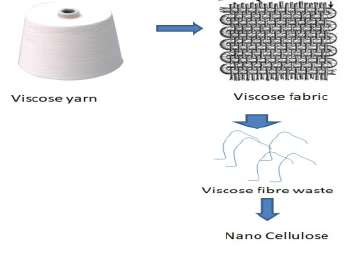
Fig. 2 Recycling process for Viscose Rayon wasteb
As viscose rayon is made of cellulose treatment with sulphuric acid, i.e. acid hydrolysis reaction (Acid hydrolysis with mineral acids (6–8 M), at 40–100 °C, from 30 min to several hours) produces Nano-cellulose.
Nano-cellulose is an interesting material because it has unique physicochemical properties such as large specific surface area, high strength, and low density. The potential applications of Nano-cellulose are in the fields of Nano-composite, template formono hybrid synthesis, food packaging, drug delivery, tissue scaffolds for cellular culture, oil treatment (10).
The emergence of fast fashion has led to increased consumer purchasing and shorter clothing life cycle, and higher rates of clothing disposal. Some of these clothes can be recycled and up-cycled 18 JUNE 2021 according to the available resources since many awareness programs have been implemented to develop recycling. A large amount are going to landfill. Some of the fibres are shredded and used for the making of the carpets. Studies show that in carpets, imparting different types of chemical finishes value addition can be done. Another approach is to use the waste from the sustainable fashion of viscose and cotton blends, prepared into yarns by shredding. The recycled spun yarns are made into carpets, and flame retardant finishes are applied (11).
Recycled rayon waste-kapok mixture (RRWK) for the sorption of different types of oil (diesel oil and motor oil) under static conditions. Oil with a higher viscosity tends to have a higher initial sorption ratio. The SEM images of RRWK show that fibre structure affects oil sorption due to the hollow lumen and the gaps between the fibre. RRWK showed that the capacity for oil sorption was higher than polypropylene. It can be concluded that utilizing industrial waste to produce RRWK is an effective way to create low-cost, environmentally friendly oil sorbents (12).
The mechanical properties of viscose sandwich composites composed of uniaxial warp knitted viscose fabrics as surface layers and non-woven viscose fabrics as the sandwich core were investigated. The aim was to investigate a low-cost non-woven viscose fabric used in structural composites so that a sandwich-type laminate was obtained. Combining a higher cost and high performing fabric, with a low-cost fabric, was possible to minimize the overall costs without a significant sacrifice on the mechanical performance. Combining the percentage of uniaxial warpknitted and non-woven fabrics with varying configurations shown to be effective for improved impact resistance behavior. The results showed that samples with higher uniaxial fibre weight and configuration could withstand a significantly higher force (13).
Chitosan-Viscose rayon bio-composite was successfully prepared using a chitosan matrix reinforced with viscose rayon filaments in uni-direction. FTIR spectra suggested a molecular interaction between the components in the composite. Tensile strength of the biocomposite increased in proportion to the reinforcing material with a simultaneous increase in stiffness, as shown by the decrease in elongation. The thermal stability of the composite was far higher than the pure chitosan film. The bio-composite was more crystalline as compared to the blank chitosan film. SEM indicated a uniform distribution of the chitosan polymer around the viscose rayon filaments. Thus, such bio-composites, composed of sustainable cellulose and protein resources, are biodegradable with excellent mechanical and thermal properties that can be used in various fields like medical, construction, and automotive (14).
Recent Developments in Viscose production
Viscose rayon occupies a global share of about 31% of all the fibres recent research states that recycled cotton waste fibres and viscose rayon can be produced by using cotton as raw material, as we know that Viscose is manufactured from tree pulp cutting down of trees and forests can be saved helps to regenerate the oxygen levels and helps to maintain ecological balance (16). Birla Cellulose has committed to the circular economy by using a minimum of 20% in-house cellulosic pre-consumer industrial fabric and had plans of increasing the potential use upto 50% waste from industrial fabrics and postconsumer clothing with a distinction of Recycled Claim Standard (RCS) (17). In 2021, Reviva was launched as a next Gen innovation bu upcycing cotton waste. The focus on recycling of cellulosic pre- and post consumer waste as raw material thus reducing the dependence on virgin raw materials for Viscose rayon manufacturing (18).
Conclusion
As Viscose rayon is one of the fibres that is popular, the demand across the globe has risen. Recycling, reuse and up-cycling of Viscose can help develop a green and sustainable solution to the environment and also helps to reduce the water and carbon footprints. Many applications have been developed from Viscose rayon, but the scope for furthering applications is immense. Although mechanical shredding of yarns to a fibrous form to go back in production gives scope for circularity, there is also a potential through chemical means.
References
- Rayon Accessed from https:// en.wikipedia.org/wiki/Rayon
- Muhammad Rehan Ashraf (2014), https:// textileinsight.blogspot.com/2014/09/historyof-viscose-rayon.html
- Md. Omar Faruk, (2018),Viscose Fibre, Viscose Rayon Production, Properties of Viscose Rayon. Accessed from https://textilestudycenter.com/viscose-rayon-production/
4.https://www.swicofil.com/commerce/ products/viscose/278/applications
- Bartl, A., Hackl, A., Mihalyi, B., Wistuba, F. I., Marini, I., (2005). Recycling of fibre materials. Process Saf. Environ. Prot. 83 (B4), 351–358.
- Economic Benefits of Recycling, DHEC’s Office of Solid Waste Reduction and Recycling, Columbia, SC, OR-0591 3/08. It can be downloaded from http://www.scdhec.gov/ environment/lwm/recycle/pubs/economic benefits of recycling.pdf.
- Bhalla, N, (2005). Market Transformation Programme–Waste Clothing Textiles. Environmental Resources Management, October 2005. www.erm.com.
- Recyclability Potential Index (RPI): The concept and quantification of RPI for textile fibres. https://doi.org/10.1016/j.ecolind.2011.10.003
- Passas, R., Voillot, C., Tarrajat, G., Caucal, G., Khelifi, B. and Tourtollet, G., (2001), Morfi as a novel technology for morphological analysis of fibers, Recents Progres en Genie des Procedes, 15: 259–264.
- Karen S. Prado, Danielle Gonzales, Márcia A.S. Spinacé (June 2019), Recycling of viscose yarn waste through one-step extraction of nano cellulose, International Journal of Biological Macromolecules 136, 729–737
- Raj Kishore Nayak, Shadi Houshayar, Asis Patnaik, Long, T. V. Nguyen, Robert Shanks, Rajiv Padhye, (December 2019), Sustainable reuse of fashion waste as flame-retardant mattress filing with ecofriendly chemicals. https://doi.org/10.1016/j.jclepro.2019.119620
- Chaowalit Senanurakwarkul, Panadda Kongsricharoen, Darathip Pejprom, Sutha Khaodhiar, Supawan Tantayanon, (2012) COVER STORY- REVIEW PAPER 19 JUNE 2021 Utilization of Recycled Rayon Waste-Kapok Mixture (RRWK) as a sorbent for oil removal, International Conference on Chemical, Bio-Chemical and Environmental Sciences (ICBEE’ 2012) December 14-15, 2012 Singapore
- Mikael Skrifvarsa, Hom Dhakalb, Zhongyi Zhangb, Joseph Gentilcoreb, Dan kessona, (2019), Study on the Mechanical Properties of Unsaturated Polyester Sandwich BioComposites composed of Uniaxial Warpknitted and Non-woven Viscose fabrics, Composites Part A 121, 196–206 https://doi. org/10.1016/j.compositesa.2019.03.025
- Vikrant Gorade, Babita Chaudhary, Omkar Parmaj and Ravindra Kale, (2020), Preparation and Characterization of Chitosan/ viscose Rayon Filament Bi-composite Journal of Natural Fibers Volume: Issue, 20 May 2020.
- P. Franciszczak, R. Merijs-Meri, K. Kalniņ š, A.K. Bł ędzki, J. Zicans, (2017), Short-fibre hybrid polypropylene composites reinforced with PET and Rayon fibres – effects of SSP and interphase tailoring -Composite Structures. Composite Structures.
- A. A. Polyutov, L. S. Gal’braikh, A. V. Byvshev, R. Z. Pen, Yu. Ya. Kleiner, and V. M. Irklei, (2000), Cotton Cellulose: Ecological and Resource-saving Raw material for the production of Viscose Fibres, Fibre Chemistry, Vol. 32, No. I. https://www.textileschool. com/156/rayon-the-multi-faceted-fiber.
- Birla Cellulose Manufactures Viscose Fibre Using Pre-consumer cooton Waste, (2019), https://www.adityabirla.com/media/press-reports/birla-cellulose-manufactures-viscose-fibre-using-pre-consumer-cotton-waste.
- Sustainability Report 20-21 Viscose Accessed from https://sustainability.adityabirla.com/pdf/reportspdf/policies_reports_ pdf_30_1614145577.pdf
Author: