Garment manufacturing industry is primarily engaged in the design, cutting and sewing of garments from fabric. On industrial basis there are certain areas or sequence through which Garment are manufactured
Textile industry has been playing a pivotal role in Indian economy. Textile sector alone presently provides for nearly 28% of total organized manufacture sector’s employment in India. About 93 million people directly and indirectly are engaged in this industry. Indian Textile Industry enjoys inherent comparative advantage because it is almost self-reliant from the stage of production of raw materials to the delivery of finished products from cotton growing, ginning, spinning, and weaving to Manufacturing of clothing items.
The world fast moving towards natural products and as a result of this trend, demand for cotton Garment is increasing. The demand of hosiery garment is increasing at a fast pace because of the comfort and soft feel of the product.
Garment Dyeing
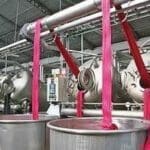
source: https://www.indiamart.com/proddetail/cloth-dyeing-services-8764560512.html
Dyeing prefabricated items of clothing represent an interesting supplement to the conventional manufacturing of clothing from ready-dyed pieces. This is above all the case because the risks involved in conventional manufacturing with reference to the correctness of the colour shade are substantial and frequently generated a broad colour range with increased storage cost.
Dyeing clothing after fabrication bears the risk of a higher extent of damage should problem in the Dyeing process. In worst-case scenarios, losses in value after irreparable error as exacerbated by an inability to maintain delivery commitment.
Basic Theory of Garment Dyeing
Depending on the wet fastnesses requirements the fabric, garment made from the cotton gray fabric are mainly dyed with direct and reactive dyes. For the low colour fastness direct dyes ars used and for high colour fastness reactive dyes are used for cotton garment Dyeing. If the cotton garment dyes with reactive dyes then two types are available in the market, namely:
- Hot brand reactive dyes.
- Cold brand reactive dyes.
Among those two brand of reactive dyes, hot brand reactive dyes are commonly used for cotton garment dyeing. Because cotton garment dyeing with hot brand dyes facilitates easier and quicker dyeing process with reasonable good dyeing quality.
Stages of Production
Apparel Production is generally done in four stages:
- Procurement and Inspection of raw material
- Laying and Cutting of fabric/material
- Assembly of the product
- Finishing and Packaging
Besides these, there may be an additional stage of ‘Value Addition’, which is a term used to indicate any process that adds to the total cost of the product and hence increases the value of the product. The addition is to enhance use and serviceability/functionality of the product and/or its aesthetic appeal. This includes special finishes to yarn and fabric (e.g., special washes to garments like sand wash or enzymes wash for denims) or surface ornamentation (e.g., prints, embroideries, etc.). This becomes specific to the product style and could be done before, during or after assembly of the product.
- Procurement and Inspection of Raw Material
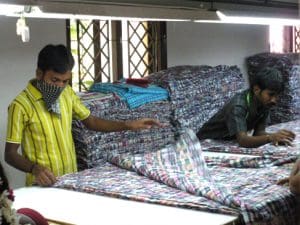
source: https://textilelearner.blogspot.com/2015/07/raw-material-inspection-in-garment.html
The process of apparel manufacture begins with the procurement of raw material and inspection or checking of the same. This includes the fabric and trims (zippers, buttons, interlinings, labels, tags etc.). Fabric inspection is done to find faults or defects in the fabric. Ideally 100 per cent of fabric received should be checked before it is cut. However, when the fabric is procured from a reliable source or when the fabric is certified as fault free by the fabric manufacturer, only representative sample quantities are checked.
Fabric defects can be classified on the basis of the source of the
faults as:
(a) Yarn faults
(b) Weaving faults
(c) Dyeing faults
(d) Finishing faults
Some defects may arise due to a combination of the factors detailed above.
Let us briefly examine some of these:
Defects arising from yarn faults

source: https://fashion2apparel.blogspot.com/2016/12/yarn-faults-spinning-types-yarn-fault.html
- Coarse end and fine end: Warp yarns having a larger diameter or smaller diameter than those normally being used in the fabric.
- Fuzz and Fuzz balls: Fuzz is the loose or frayed fibers originating from the yarns. These may form tiny balls and get woven into the fabric.
- Slub: An abruptly thickened location in a yarn characterised by softness in twist and more or less of short duration.
Defects arising from weaving faults
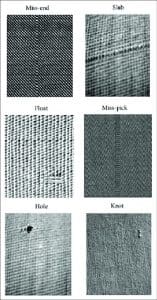
source: https://www.researchgate.net/figure/Some-of-fabric-defect-caused-by-a-knitting-machine_fig2_330820797
- Bar: Filling wise band across the full width characterised by a change in appearance from normal color or texture of finish.
- Barre’: An unintentional, repetitive visual pattern of continuous bars and stripes usually parallel to the filling of woven fabric or to the course of circular knit fabric.
- Bias filling: The filling yarns or colour pattern not being at right angle to the warp yarns.
- Bowed filling: The filling yarns or the colour pattern having a curvature.
- Broken end: A warp yarn missing for a portion of its length.
- Float: Thread that extends unbound over the threads of the opposite yarn system with which it should normally be interlaced.
- Kink: A short length of yarn spontaneously doubled on itself. Also called curl, kinky thread, looped yarn, snarl.
- Misreed: A warp wise streak caused by improper spacing of the ends across the fabric.
- Smash: An area where the fabric has been ruptured by the simultaneous breaking of a large number of adjacent warp threads.
Defects arising from dyeing faults
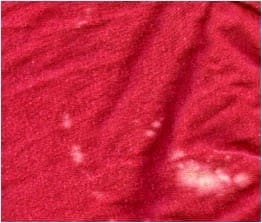
source: https://textilelearner.blogspot.com/2014/08/fabric-faults-created-during-dyeing-and.html
- Colour run: The colour of one area has bled or superimposed on the colour of another area.
- Shaded: The colour or bleach is not uniform from one location to another.
Defects arising from finishing faults
- Baggy: A fabric which will not lie flat on the cutting table.
- Chafe: An area where the fabric has been damaged by abrasion or friction. Cuts, tears, crease, wrinkle and curled selvedges.
- Tentering marks: Enlarged pinholes or distorted areas along the edge of the fabric caused by the holding of the fabric to width during finishing. Also called pin marks.
- Uneven finish: The finish is not uniform from one location to another.
Fabric Inspection and Testing

source: https://bournecrisp.com.au/how-we-test-bourne-crisp-fabrics-to-ensure-quality/
There are internationally accepted systems of fabric inspection which define the way the fabric is to be inspected and what constitutes an “OK” fabric. In all the systems, the fault or defect is assigned points based on its size, type, spread etc. The total points in a given linear length are then totalled and the fabric is ‘accepted’ or ‘rejected’. Some companies have customised their own system by adapting from existing systems according to their need and specialised fabric types. The acceptance criteria also depends on the final product (style, market, functionality, performance base, etc.) being made. Other than this, certain tests are also conducted to test the suitability of the fabric for its end use. The tests may be standard tests done by any fabric manufacturer or may be specially requisitioned by the buyer of the end product. These tests include colour fastness (against light, moisture, perspiration, chlorine etc.), thread count, fabric weight, shrinkage, flame-retardant etc. Once the defect and its extent are identified, the possibility of repair/rectification is checked. If the fabric can be rectified, it is sent for the selected process. If not, the fabric is rejected. Some faults may be accepted if the extent is not very high i.e. it does not affect a large area of the fabric. Sometimes the decision to accept defected fabric may be taken if the cost and/or time involved in the reprocessing of the fabric are too high to be absorbed by the cost of the order. Fabric inspection is one of the most important steps in the process of production, as it defines the final quality of the product The cost of raw material in any garment is about 70%, out of which 90% or above is that of the fabric. In case this process is not carried out properly, the cost factor of the fabric component in the garment would increase leading to less profits and, in some cases, losses.
- Laying and Cutting of Fabric/Material
source: https://fashioninsiders.co/toolkit/how-to/cutting-fabric-for-production-versus-sampling/
The next stage in the production of garments is the planning and processing
of the cutting of the fabric. This involves the following steps:
- Marker plan:
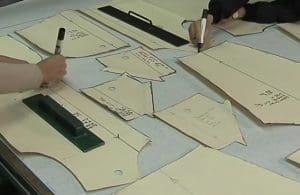
source: https://fashion2apparel.blogspot.com/2017/03/marker-making-methods-apparel.html
A marker is defined as the placement of pattern pieces on fabric in such a manner that the consumption of fabric per garment is optimised. The first stage is to identify the number of pieces that make up the entire pattern of one unit of item. The planning of the marker defines the average consumption of the fabric per piece which ultimately affects the cost of the product.
The marker may be planned by manually placing pattern pieces on a defined width of the table and creating permutations till the most optimum length is achieved. This is very time consuming especially where the number of pattern pieces involved are high (such as in a formal jacket). There is also the problem of copying the marker so that it can be replicated for multiple lays. The more efficient technique of marker planning is by using specific computer software or CAD system. In this, the pattern pieces are fed into the system (digitised) and planning is done on a monitor. This technique is time efficient and eliminates most of the errors that are related to a manual plan. A printout of the final marker/s is taken for replication which ensures that the consumption of fabric per unit of product is maintained.
2. Spreading:
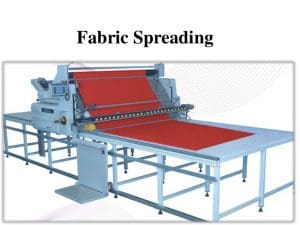
source: https://www.slideshare.net/Farhanullahbaig/fabric-spreading-72936786
Fabric is smoothened and spread along lengths of table in layers. The length of the layer is defined by the marker. The fabric layers are matched along one length edge and are equal in length. The fabric may be spread by hand or with the assistance of machines called Spreaders. These machines may be mechanically, electrically, electronically or computer operated. The final product of the spreading process is called a lay. The height of the lay will also affect and be affected by the cutting apparatus to be used. Care is taken during lay preparation that each lay consists of only one type of fabric.
3. Marking: The patterns are traced on the top layer as per the define marker. In some cases a computerised printout of the marker on a paper sheet of the same width as the fabric may be used as the cover to the lay. This then gets cut with the fabric layers.
4. Cutting:
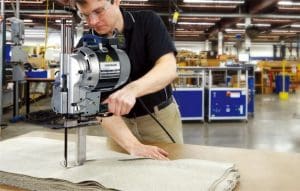
source: https://fashion2apparel.blogspot.com/2016/12/types-fabric-cutting-machines.html
The layers are cut simultaneously using machines that maybe controlled either manually or through computer systems. There are different types of machines like the straight knife, round knife, band knife and die cutters. The height of the lay, i.e. number of layers in each lay, is dependent on the type of cutting apparatus as well as the dimensional stability of the fabric. Each type of cutting apparatus has its own merits and demerits — e.g., the straight knife machine is the most readily available and the cheapest of theme chained cutting apparatus. However, it is not the best choice to cut knitted or stretch fabrics as it does not have the grip that can control the dimensional stability of such a fabric while cutting. The cutting apparatus used to cut a lay is usually mechanised. This is because scissors cannot cut through multiple layers with precision. Also the time and effort required in this is higher than may be possible in production.
5. Bundling:
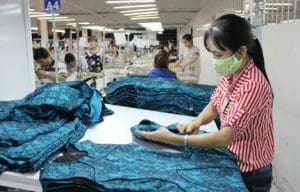
source: https://textilelearner.blogspot.com/2012/04/garment-checking-checking-list-of.html
The cut pieces are bundled for further processes of stitching/embroidery/printing etc. The number of pieces in a bundles dependent on the type of production system and the process sequence to be followed. The bundles may have all the components of a garment or only selected ones. Along with bundling, ticketing of the components is done which identifies the layer number within the lay. This is done to ensure that components of one garment are cut from the same layer of fabric.
- Assembly of the Product
source: https://fashion2apparel.blogspot.com/2017/03/production-organization-systems.html
The garment pieces are next sent to the assembly or stitching section comprising of different types of sewing machines. The sewing machines may be multipurpose, i.e they can be used for different types of operations of sewing, or the machines may be specialised, i.e., they are used for specialised operations only. The more common of the first category of machines (multipurpose) is the Single Needle or Lockstitch Machine. It uses two threads to do the stitching, one which enters the fabric from the top through the needle and one which enters from the bottom through a bobbin. This machine can be used for any type of fabric and any kind of stitching operation. The lockstitch is reversible and a very stable, strong and inflexible stitch. It is also possible to work it in reverse direction to have a double stitching line.
For stitching of knitted fabric, the machine used is the Chain Stitch machine. This stitch may use between 1–5 threads for formation. The lower thread comes through a hooked device called the looper. The looper may or may not have its own source of thread. The chain stitch is flexible and non-reversible by nature. It is predominantly used to accommodate stretch in the fabric being sewn. The commonly used type of this machine is the Over lock machine. This machine is used for all garments made from knitted fabric.
The process of assembly, i.e., the way in which the multiple pieces of the garment are put together to make a complete garment, may use one or a combination of multiple production systems. Some of these are:
- Tailor system – Each operator or tailor assembles an entire garment. This system is used mainly in customised clothing — clothing made to fit and to the measurements of one individual. The operators are extremely skilled and are capable of working on varied types of machines.
- Team working or module system — The garment is assembled by a group or team of operators. This is the most popular system in the garment manufacturing industry. Each team is a mix of skilled, semi skilled and unskilled workers and jobs are allocated according to skill level requirements of the assembly process.
- Unit production system – The garment assembly process is broken into smaller units called operations. Each operator is given one or more operations to do which need to be done on the same sewing machine. The piece is passed from one operator to the next operator in a predetermined pattern enabling the total assembly of the product. This system is used effectively in units with large manufacturing facilities or/and in garments which have many operations as also in manufacturing units which are catering to production of a single product. This system is dependant more on the training of the operator. Operators are trained on specific machines and in specific type of operations so that their individual productivity is high. The system does not work very well in small orders and for garments which have very few operations.
- Finishing and Packaging
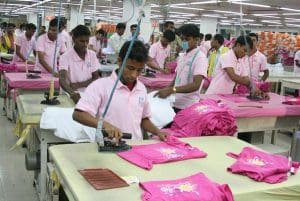
source: https://in.pinterest.com/pin/310818811765266911/
The garments are finally sent for finishing and packaging. The finishing process includes final inspections, stain removal, repairs, ironing/pressing and folding. The pressing/ironing techniques would also define the final look of the garment (creases, folds, size of fold, etc.). Packaging of garments can be done in many ways. Some garments are hanger packed (coats, jackets, suits, children’s dresses etc), some are fold packed (shirts, t-shirts, track suits, etc.) and some are folded and then hanger packed (trousers). The type of packaging is dependent on the specifications of the buyer, the display techniques at point of sale, the bulk of the garment (volume of individual piece), the price of the garment etc. For exports, all the above detailed types of packaging may be used as specified by the buyer. The packing of the garments differs from packaging. Packing is the process of preparing any product for dispatch from one place to another. The most common packing technique is the use of Cartons. A carton is made of layers of corrugated paper stuck together in a box shape (cube/ cuboid). The size of the carton can be customised as per requirement, defining its length, width and height.
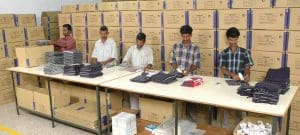
source: http://hassanindustries.com/ft_finishing.html
Quality Assurance in the Garment Industry
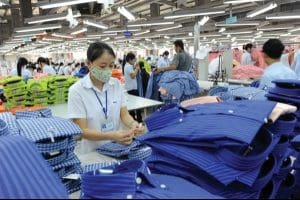
source: https://clothingindustry.blogspot.com/2017/12/quality-assurance-process-apparel.html
Quality of the product is defined as its ‘fitness for use’. That means the requirement of the customer actually dictates whether any product is a quality product or not. The frequently used term ‘Bad Quality’, hence, does not exist as the term ‘Quality’ by itself defines the fitness of the product. The quality of the product is ensured by –
(a) Adopting proper procedure of work – defining the complete process of the product manufacture from raw material to finished goods and elaborating on operating procedures for each department.
(b) Following the adopted procedure as defined above.
(c) Selection and use of appropriate machinery.
(d) Training of manpower – This is done at all levels, i.e., operators, supervisors and management – on machinery, maintenance, quality systems, production and the product.
(e) Inspection of product at various stages of production – For this, crucial stages are selected. There are no defined rules on the frequency and quantity of inspection. Companies tend to develop their own rules for the same. The important issue is that the final product should conform to the standards and specifications laid out for the product in question.
Textile and Clothing Industry of India
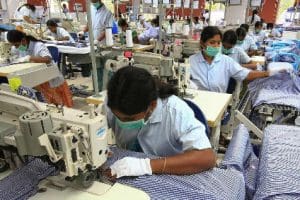
source: https://www.just-style.com/analysis/india-lockdown-of-little-impact-as-orders-already-cancelled_id138416.aspx
Textile and Clothing (T&C) industry is one of the key contributor in Indian economy. The textile industry accounts for 14% of industrial production, employs 35 million people, accounts for approximately 12% of country’s total export basket and contributes 4% of GDP. At current prices, the size of India’s textile industry is US$ 55 billion out of which 64% is consumed in domestic market only (Annual report 2009-10).
As per available WTO data, India’s percentage share in global textile and clothing trade was 4% in textiles and 2.8% in clothing during the year 2007. India’s rank in world trade has been 7th in textile and 6th in clothing. The vision statement for the textile industry in the 11th five-year plan (2007-12) is to secure 7% share in global textile trade by 2012. The export basket consists of a wide range of items comprising readymade garments, cotton textiles, handloom textiles, manmade fiber textiles, wool and woolen goods, silk, jute and handicrafts including carpets. Readymade garments accounts for almost 42% of total textile exports. Readymade garments and cotton textiles accounts for nearly 72% of total textile exports (Annual report 2009-10).
Exports of textile and clothing products from India have increased steadily over the past few years, particularly after 2004 when quota in textile was discontinued. In global context, India offers a comparative advantage in textile and apparel sector, with its excellent raw material base, skilled manpower and cost competitiveness. Through exports of textile and clothing products, India earns its major chunk of foreign exchange required to payoff for its imports and minimizes the trade deficit. .
The Indian textile industry has already established its name in supplying high quality yarns and grey fabrics to the world markets. However, it is yet to make and impact in finished products. It only makes sense to go in for further value added products such as garments and leverage on the country’s established name in the export markets. Naturally many textiles companies have announced plans to diversify into value added business to target a higher realization and compete better in the export markets (S.V. Arumugam 2006).
The Indian industry as a whole is going through one of its good times with growth rates going up from 5.8% in 2002-03 to 7% in 2003-04 and 8% in 2004-05 (S.V. Arumugam 2006) and 8.5% in 2007-08. Year of 2008-09 has not been so good because of world-wide economic meltdown. Where US along with some of the other economies of the world have shown negative growth or contraction in GDP, India has shown positive growth.
Since elimination of quota, the demand for Indian textile product has increased world-wide and India has emerged as strong global sourcing destination. Different foreign brands have opened their liaison or sourcing office in India. Most prominent names are Marks and Spenser, Nike, Haggar, Kellwood, Little Label and many more.
Impact of Covid-19 on the Indian Apparel & Textile Industry
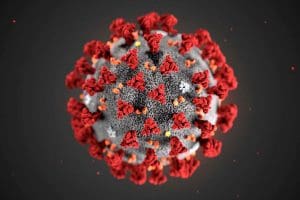
source: https://www.newscientist.com/term/covid-19/
Indian Textiles and Apparels (T&A) industry, accounts for approximately 4% of the global T&A market. The T&A industry is one of the largest and the most important sectors for the Indian economy in terms of output, foreign exchange earnings and employment. The industry contributes approximately 7% to industrial output in value terms, 2% to the GDP and 15% to the country’s export earnings.
Due to countrywide lockdown, however, the industry is grappling with major hurdles in the following areas:
Labour force and employment: T&A provides direct employment to over 45 million people but the nationwide lockdown has led to a temporary closure of factories and lay-offs have already begun among low wage workers.
Import & Exports of raw material and ready-made garment: The Covid-19 pandemic is primarily expected to adversely impact exports and with second order impact on the domestic markets with both exports as well as domestic sales falling.
The pandemic has affected the majority of India’s export market (the US and EU together constitute for approximately, 60% of the total apparel exports from India in value terms), causing order cancellations/deferral of order leading to inventory build-up and expectation of slower realization of export receivables leading to higher working capital requirements.
Apparel exports are expected to fall due to drying up of order in the last quarter of FY20, working capital issues and lack of clarity on the duties and incentives especially when exporters from Bangladesh, Sri Lanka and Vietnam receive preferential access.
Additionally, domestic consumption is also getting impacted due to all India closure. New store openings have stopped and even domestic stores are facing an inventory build-up due to apparel sources for the upcoming summer season, Further, domestic prices could be negatively impacted if exporters dump their inventories in the domestic market leading to even reduced margins. This could lead to short term blips such as reduced employment of casual labour (factory closures and people moving back to their home towns) and reduced consumption.
Cash flow constraints: The sector has been grappling with profitability issues due to a sharp decline in yarn exports, cheaper imports etc. these issues only look to get aggravated further with the current crisis.
Supply chain disruption: The Garment manufacturers need to look at local sourcing opportunities, due impact on imports and export.
Consumer sentiment: If nationwide lockdown continues and the situation persists, it will impact consumer sentiment on the higher side, due to closure of the market and mall also to maintaining social distancing, safety and health.
The extent of the outbreak and lockdown would directly impact the length of the recovery cycle. However, to minimize the impact the Confederation of Indian Textile Industry (CITI) has requested the government to immediately announce a relief package for the textile and apparel sector to mitigate the crisis being faced by the capital and labor-intensive textile Industry, post the corona virus spread.
Conclusion
Garment production is an organized activity consisting of sequential processes such as laying, marking, cutting, stitching, checking, finishing, pressing and packaging. This is a process of converting raw materials into finished products. It will be difficult to maintain the industry if production is not, up to the mark if the preproduction phase of preparation of material is not properly carried out.
Ready to wear apparel or garment manufacturing involves many processing steps, beginning with the idea or design concept and ending with a finished product. Apparel manufacturing process involves Product Design, Fabric Selection and Inspection, Patternmaking, Grading, Marking, Spreading, Cutting, Bundling, Sewing, Pressing or Folding, Finishing and Detailing, Dyeing and Washing, QC etc.
Reference
http://ncert.nic.in/textbook/pdf/lehe203.pdf
https://shodhganga.inflibnet.ac.in/bitstream/10603/2895/7/07_chapter%201.pdf
https://admin.umt.edu.pk/
https://www.textilelearner. com
https://www.iit.delhi.com
http://www.retail4growth.com/news/impact-of-covid-19-on-the-indian-apparel-textile-industry-4963

Article Writtten By-
Ms. Sidrah Mubin Patel. B.Sc. in Textiles and Apparel Designing, Sir Vithaldas Thackersey College of Home Science.
Textile Value Chain Intern. Email: tvcmedia.digital@gmail.com