Abstract
Automation is most often defined as, “automatically controlled operation of an apparatus, process or system by mechanical or electronic devices that take the place of human organs of observation, effort, and decision”.
The purpose of this paper is to investigate the status and the effects of technology adoption on the level of organizational factors within the context of the apparel industry.
- Introduction
1.1 Definition
Automation is often defined as, “The automatic operation of an instrument, process or system by mechanical or electronic devices that replace human organs for observation, effort, and resolution”. The intensified competition in the global market, it became important for manufacturers to thrive, to gain sustainable competitive advantage by innovations in technology or concepts as well as in production. Typical production in the garment manufacturing process still involves large manual operations and automatic assembly. Garment manufacturing is still more labour intensive than technical work, so the need for technical support may not be significant in apparel industry technology. Faced with the rising cost of labour, advanced textile manufacturing technologies have been called upon to increase productivity and produce high-quality goods, at high volume, in short cycles, at low cost [1].
The adoption of advanced technology is a way to improve such areas and meet export standards. Recent automation in apparel industry includes computerized data monitoring, computer-aided designing, automatic fabric spreader, automatic fabric cutters, high-speed sewing machines, advanced pressing and finishing machines, etc. This contributes to the development of advanced goods in the global supply of clothing and provides a new understanding of how manufacturers can embrace technology and remain competitive in the global market.
- The need for Automation in Apparel Industry
The adoption of technology has emerged as an important competitive decision in recent global trade. The most important reasons for moving toward more mechanization and automation are to be able to reduce cost or to increase production without increasing cost. If the industry can decrease the cost per item, it will increase production without increasing total cost. The ability to increase the quality without increasing cost per item was nearly as important.
Flexibility, quality, inventory reduction, efficient production cycle, and shorter lead-time in manufacturing became essential for firms to achieve global competitiveness. It is apparent that reducing cost and improving production capacity are most important for firms, which are seeking an increased share of the market today. The common introduction and adoption of new technologies become an important factor in the competitive advantage of the global market because firms can maintain rapid responses and market demands using technology [1].
- Developments in various department of the garment industry
2.1- CAD
CAD stands for Computer-Aided Design. It is nothing but the use of computer in the creation, modification and optimization of a design. CAD software is used to improve the efficiency and productivity of a designer by providing a tool using which they can visualize how the 3D model of that product design will look like. CAD is used in many applications including automotive, shipbuilding and aerospace industries and many more. CAD also widely used to produce computer animation and to produce special effects in movies. CAD plays important role in designing and manufacturing industries [2]. Nowadays CAD software becomes an essential tool for fashion designers and garment manufacturers by providing functionality such as pattern making, virtual test fitting, pattern grading, marker making etc. With the help of CAD, software designers can visualize the final product and can inspect these models to make modifications. Along with the conversion of the 2D model into the 3D model, the system also provides tools to give animations to these products so that movement of that product can be visualized. In addition, we can rotate the model to view it from all angles. Hence, with this 3D modelling, there is no need to make a physical sample and every design can be stored online for future reference [3].
3D Designing
3D designing in garment industry refers to the draping of 2D digital pattern pieces on virtual mannequins followed by making changes according to the requirement of designs. Later on, this virtual garment can be displayed on the real body by making an actual garment. Various computer-aided design systems for visualizing 3D designs have been already introduced into the garment industry [4].
2.2- Spreading
- Spreading development –
Spreading is the process of the unwinding of fabric rolls on long and wide tables for cutting. It is the basic step to get a high-quality final product, so it should be done precisely. Several fabric layers to be spread depends upon several garments to be stitched. Spreading can be done manually or with the help of machines. Fabric spreading machine is used for bulk production.
- Intellocut software –
This system works at the fabric utilization stage i.e., at cutting department. Before cutting of garment pieces, it is important to spread fabric correctly. Intellocut helps us by providing features like planning automation, paperless execution, providing warning signals and real-time visibility.
- Planning Automation- Intellocut helps us for automatic planning with the assistance of artificial intelligence by providing the most efficient cut plan.
- Paperless Execution- Intellocut controls key processes such generation of the lay plan with the help of system or tablet application by avoiding any paperwork.
- Warning Signals- Intellocut software can immediately replan cut plan on one click after getting any negative feedback from the cutting department.
- Real-time visibility- Intellocut tracks fabric usage or wastage with the BOM vs actual reporting. This will give us a clear idea about the current scenario of cutting department [5] [6].
Figure 1: Process flow of Intellocut system (source- Intellocut)
2.3- Cutting
Cutting information –
Cutting is the process of cutting fabric into garment pieces. This department is responsible for the cutting of fabric and feeding of that cut parts to the sewing department. After marker making, garment parts are cut and taken out of layers. Cutting can be done manually or with the help of machines. Various cutting technologies like straight knife cutting, band knife cutting machine and computer-controlled automatic cutting machines are available.
- Gerber Cutter (Blade)
Gerber introduced the world’s first automated cloth cutting machine, which brought a revolution to the apparel industry.
Key features:
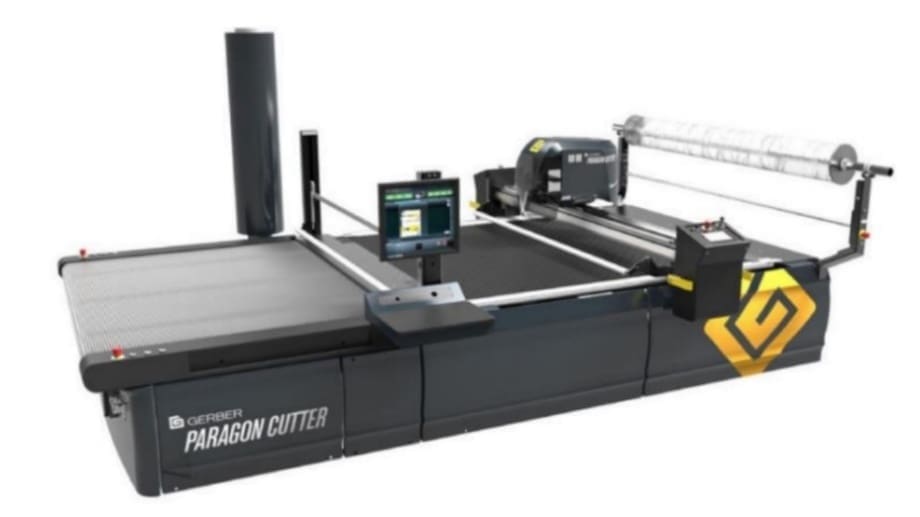
Figure 2: Gerber Blade Cutter (Source – Gerber)
- Easy to use- Gerber cutter is user friendly; an operator can learn within a few hours how to operate Gerber cutter and can rely on its built-in intelligence to guide them through any cutting task.
- Maximum throughput- Machine helps us for quick and accurate setup. Moreover, its self-adjusting intelligence allows an operator to start cutting faster with higher efficiency. It improves productivity and workflow; the output of the machine is cut parts hence it reduces lead-time.
- Optimal first-run yield- Machine makes a fine balance between cut speed and part quality. It maximizes the speed of the machine only when it is giving optimum quality in the final cut parts.
- Uptime- Operator can replace knife-sharpening stones in few seconds and get up to three times more usable life than traditional stones.
- Metrics that matter- It provides easy to understand metrics containing certain parameters like total cutting time, idle time, the time between jobs, total units cut and more. By using this parameters management team can manage the workflow of processes.
- Integrated data sharing- Gerber cutter can integrate with CAD and automatic
Spreading the machine and help to save time and reduce errors by making the system more visible. Simply machine can scan a barcode to retrieve a specific parameter so there is no need to search for a file and manually enter details like ply count and material type etc. [7].
2. Plasma Cutting
Plasma cutting was originally invented to fulfil the need for accurate cutting of stainless steel and aluminium. However, nowadays plasma cutting can be used in the apparel industry to cut the fabric. In this system, cutting is carried out utilizing a high-velocity jet of high temperature ionised gas (Argon). This method can cut the plies of fabric at a faster rate but it leads to the problems related to the quality of cutting [8] [9].
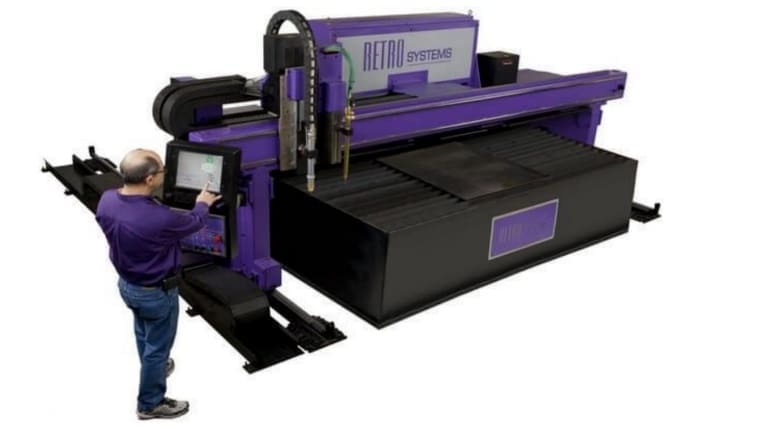
Figure 3: Plasma Cutting Machine (Source – Clothing Industry)
The plasma cutting can be used to cut one or more plies of fabric at a time by using a special gas (Argon), which becomes plasma at 30000 °C. The fabric is cut with higher speeds by the nozzle, which is made up of argon gas.
3. Water jet
Water jet cutting machine is a machine in which cutting is carried out through high-pressure jet of water. For this purpose, either specially treated water or an abrasive agent may be used. A fine jet of water is passed through a nozzle at a very high speed to cut the fabric. The pressure of water is nearly 60,000 pounds per square inch. The high-pressure water jet acts as a solid tool when it cut the fabric [10] [11].
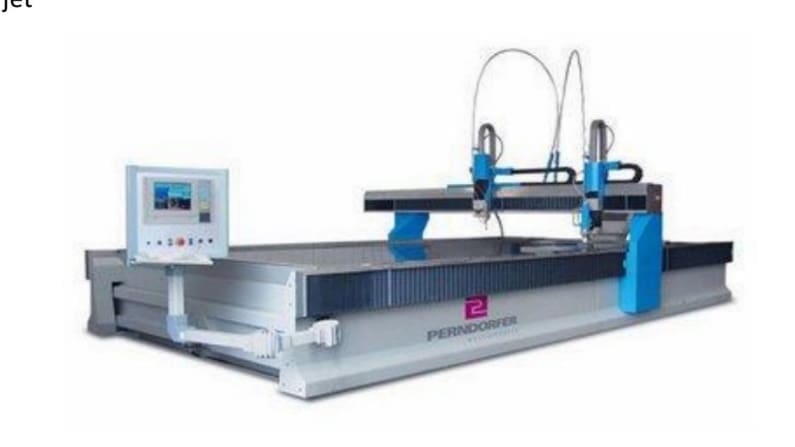
Figure 4: Water Jet Machine (Source – ETMM Online)
4. Laser cutting machine
In Laser, cutting machine cutting is carried out through ray of light in very fine spot by using the laser. This machine is widely used in leather and apparel industry. A computer controls the cutting head. Fashion designers are mostly selecting laser cutting in the garment industry. In synthetic fabrics, the laser melts the synthetic fibres and fuses at the edges, which result in getting well-finished edges; this will avoid the problem of fraying of fibres at edges of cut parts produced by conventional knife cutters. In laser, cutting a laser is used to cut the fabric into the desired shapes of patterns. A very fine laser is focused on the fabric surface, which increases the temperature and cutting takes place through vaporization. Generally, gas lasers (CO2) are used for cutting of fabric [12].

Figure 5: Laser cutting machine (Source – Core.ac.uk)
The only limitation of laser cutting is the number of lays of the fabric that can be cut. This cutting is best suited for cutting of single or a few lays, but the accuracy and precision are not obtained with a greater number of plies. So most preferably, this cutting machine is used for cutting of single-ply.
2.4 Sewing
- Automatic sewing machine
Sewing machines plays a crucial role in constructing the garment by stitching the fabric pieces together with the help of thread. The sewing machine was invented during the first industrial revolution (18 to 19 century). Sewing machines have been leading a change amongst the apparel industry from manual sewing to automatic sewing and have enabled operators to create garment at the tip of their fingers. This automation has greatly improved the efficiency and productivity of the apparel industry. The effects of the automation in the apparel industry have led to major changes in other industries as well. Like fabric, manufacturers have made to produce more fabric to match the need of apparel industry [13] [14].
Automation has done in various types of machines like single needle lock stitch, double-needle lock stitch, overlock, button stitch, buttonhole machine, etc. This can be achieved by using work aids. Following are a few examples of automatic sewing machines.
1.1 Surging
Surging is nothing but overlock at the edges. It is mainly done at trouser. The automatic surging machine needs to feed just trouser pattern and the machine will automatically surge both the edges of the pattern. After surging is done, the machine lays those patterns on the handle.
Here is a normal sewing process, there are two different operations for each edge of the pattern, but in an automatic sewing process, it is completed in a single operation [16].

Figure 6: Auto Surging machine (Source – Juki)
1.2 Computer-controlled cycle machine with an input function
Cycle sewing has been very popular among the apparel industry. Cycle sewing machine includes a small operation panel box for data input and a clamp to hold the pattern. The operator just needs to input the parameters of sewing are like length width, stitching path, etc. and clamp the pattern. Then the machine will automatically stitch the pattern as requested [16].

Figure 7: Computer-controlled cycle machine with input function (Source – Juki)
1.3 Pocket attaching machine
Welt pocket stitching is one of the critical operations amongst the all. This process includes 3 to 4 pieces for stitching and around 4 to 6 operations. This automatic pocket-stitching machine makes this operation easy by performing all the operations at a time [16].
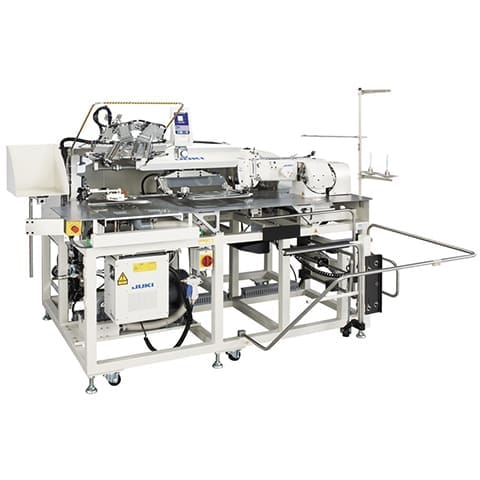
Figure 8: Computer-controlled cycle machine with input function (Source – Juki)
1.4 Automatic belt-loop attaching machine
For belt loop attaching, there are three processes, which is belt loop making, cutting and stitching. The belt-loop sewing shape and sewing size can be easily changed through the operation panel. This machine not only reduces the time required for the belt attachment process but also achieves labour saving, such as the completion of the previous process i.e. belt-loop cutting [16].
1.5 Buttonhole indexer
Computer-controlled buttonhole indexer is newly renovated next-generation buttonhole machine supplied with the preset mechanism to increase productivity and sub-clamp mechanism helps to achieve both accurate and consistent buttonholing quality. It has one operational panel box to give inputs to the machine-like distance between two holes, type of buttonhole, etc. [16].
1.6 Other
Apart from this, there are many other industrial sewing machines like pocket creasing and setting, automatic presser foot force control. Additionally, shirt front contour seamers, automatic hemmers, automatic surging of a panel with four sides surged, automatic cuff makers, ultrasonic sewing, belt turners with air-operated, cuff shapers are contributing in the automation of the garment industry [17].
2. GSD
GSD stands for General Sewing Data, which gives accurate data to calculate SMV for precise costing, line balancing, capacity, and efficiency calculations and to improve workers performance. During the production, unbalanced sewing lines results in bottleneck formation. Uncertain production capacity results in missed delivery times, production break time and overtime. Inefficient SMV calculations cause incorrect costing and production capacity. To overcome all these issues GSD provides the ability to design and measure each step or process in a production process, from cut pieces to packaging [19].
To measure each step GSD makes the work performed by a sewing machinist broken down as follows
- Get part or parts and match
- Pre-form and/or put parts to machine foot
- Sew parts together align or add parts between bursts
- Trim threads
- Put parts aside
GSD develops a common language (GSD Codes) to establish real-time production and costs, as well as a tool to create cost-effective production or production opportunities. Each code has a time value attached expressed as TMU’s (Time Measurement Units). It establishes ‘International Time Standards’ using the appropriate predetermined ‘Motion Code’ for each step in the Operation Bulletin. GSD provides a scientific, truth-based method of estimating and improving production methods and costs. Also, accurately and consistently establishes ‘International Standard Time’ for clothing and other products are sewn in the Apparel Supply Chain. These results in
- Accurate Costing
- Increase productivity
- Lesser the defects
- On-time delivery
- Improve workers performance
This process then creates an accurate & consistent Methods Database for the organisation. This database can be used further for a different style of production. The standard values set by GSD are accurate, the breakdown of the process is easily understood and therefore greater efficiency is obtained. Managers and supervisors can gain the value understanding within the short-term training.
3. ETON
ETON in the garment industry is fully automated and highly flexible material handling system, which designed to minimize manual material handling. This system helps to improve productivity, quality of a finished garment.
Technically this system consists of overhead conveyors on which individual carriers are placed. These carriers consist of several clamps in which all parts of the single garment are hanged. These carriers are moves automatically finding its way to the correct next operation, according to pre-determined operations. This movement is monitored by computer and provides all necessary data required for monitoring and managing the process of the production line. The system can be easily modified according to distinct changes in the operation cycle that is why it is considered a highly flexible system.
When an operator performs his /her operation, he/she will push a button placed on one side of a sewing machine. The system will actuate and the carrier is passed to the next operation. When a carrier leaves its place and moves to the next place it is recorded by the data collection system.
This system minimizes manual material handing because of which improves lead-time, improves ergonomics and substantially shorter throughput time, improves efficiency may vary from 30%-100%. ETON system is the most valuable investment made by garment industries from all over the globe.
Additionally, with minimum manual handling, the system helps to keep floor clean and workstation free from bundles of garment parts. In this ETON system, material-handling methods are based on ergonomics. With this system, it is possible to move material up to the distance of one centimetre from operation workstation. All opening, retying, reaching, lifting, pulling of bundles and work in process of bundles can be eliminated. Because of the application of this system operator experiences fewer injuries, less fatigue, which reduces absenteeism. Pain and injuries at the shoulder and neck are a common type of injuries causes in this system [20].
1.7 Finishing and packing
- Vapour (Steam) press
Ironing can be a daunting, time-consuming and tedious task. Using steam iron helps to give your clothes a crisp and polished look and makes ironing faster than before. New types of machines use steam because steam makes the job faster. Research proved that for wrinkle-free and super crisp clothes, steam is a key. Automatic vapour or steam press makes the pressing easy and effective. For this, the industry needs a separate boiler where steam will be produced. This one can be achieved via the use of “Vapour-Phase durable press”, finishing the garment so that it is virtually wrinkle-free for the consumer. This process, called the Ameriset process, involves the treatment of apparel with formaldehyde gases in a sealed reaction chamber. Several advantages are listed, including abrasion and crease resistance and retention of hand as well as tensile strength [21].
Another way of automatic pressing is by using a buck press machine. Its design varies as per the type of garment e.g. jacket, trouser, shirt, etc. It usually comes with blowing suction for the stability of the garment. During operation, the machine releases a high amount of steam provided from a boiler to give more pressure on the garment to give it a perfect shape and wrinkle-free look.
- Automatic folding machine
Automatic garment folding machine is very interesting equipment, which will be used to fold almost any garment that a manufacturer should want to fold before distribution for sale. This automatic folding machine can make the folding operation in almost half of the time taken by the manual way. Previously with manual folding the time required for folding one T-Shirt was 30 – 35 seconds. However, with an automatic folding machine, this time reduced to 8 – 10 seconds. The operation of the machine requires a small person (manual) involvement, which is a great help to an organization that is always looking for time to save [22].
It will work as a semi-automatic process; Users only need to place the clothes on the machine’s folding tray and the machine will pick them up for folding as the operator presses the button. For this operator need to give input to the machine with a folding pattern of the garment. The standard apparel industry style, in terms of t-shirt wraps, is now done quickly and requires little attention or monitoring. This machine can help users to reduce their load and is very useful for users with bulk folding shirts. The distribution and sorting of garments are time-consuming and subject to manual error. Automation in this field saves time and error-free distribution of garments can be achieved.
- Packing
Packing is the last operation in the garment-manufacturing unit. After folding is done, the garment pieces now need to be packed properly as per the buyer’s need. Automatic garment bagging system contributes to making automation in the garment industry. This automatic equipment accepts garments of any length and on any type of hanger. A standard monorail system delivers garments to the packing. Packing material is supplied on a roll, and the bottom of the garment is sensed, the length of the garment determines the length of the bag and the garment is packed [23].
Because of the flexibility of the equipment, garments can come to the packer in random assortment and still can be packed in the correct length of the bag, all without any direct operator labour.
- Conclusion
New innovative things in the industry will not wait; certainly, the industry itself cannot wait, due to the pressure from importers and competitors constantly forcing testing and equipment changes.
The paper has written to review about the various types of developments in apparel industry to cop up with the changes required by the fast changing fashion. The automation in the paper has been discussed from the spreading to the finishing of the apparel industry.
- References
- Automation in Textile Industry, 1 Dr. Nitin S. Choubey, 2 Manish Agrawal,1 HoD Computer Science & IT Dept. NMIMS Shirpur, INDIA, 2 PhD Scholar, NMIMS, Shirpur, India, International Journal on Textile Engineering and Processes ISSN 2395-3578, Vol 2, Issue 1, January 2016
- Abu Sadat Muhammad Sayem, “Objective analysis of the drape behaviour of virtual shirt, part 1: avatar morphing and virtual stitching”, International Journal of Fashion Design, Technology and Education, 10:2, pages 158-169, 2017
- Laurel D. Romeo, Young-A Lee, “Creative and technical design skills: are college apparel curriculums meeting industry needs?”, International Journal of Fashion Design, Technology and Education 6:3, pages 132-140, 2013.
- Abu Sadat Muhammad Sayem, Richard Kennon, Nick Clarke, “Resizable trouser template for virtual design and pattern flattening”, International Journal of Fashion Design, Technology and Education 5:1, pages 55-65, 2012.
- https://www.threadsol.com/request_a_demo cited on 30 October.
- http://www.threadsol.com/intellocut, cited on 30 October.
- https://www.dksh.com/global-en/products/tex/gerber-cutter-paragon#accordion1412913113345-1-collapse, cited on 8 November.
- https://clothingindustry.blogspot.com/2018/01/methods-fabric-cutting.html, cited on 8 November.
- https://garmentsmerchandising.com/fabric-cutting-machines-apparel/, cited on 8 November.
- https://www.etmm-online.com/water-jet-cutting–function-methods-and-applicationexamples-a-834966/, cited on 10 November.
- https://fashion2apparel.blogspot.com/2016/12/types-fabric-cutting-machines.html, cited on 10 November.
- https://core.ac.uk/download/pdf/81741943.pdf, cited on 9 November.
- Minkyung Kim , In Hwan Sul , Sungmin Kim, “Development of a Sewing Machine Controller for Seam Pucker Reduction using Online Measurement Feedback System”, Journal of Engineered Fibres and Fabrics, Volume 12, Issue 2 – 2017.
- Rezia M. Molfino, Fabio Bonsignorio, “Automated garment assembly and manufacturing simulation”, January 2009, ResearchGate.
- Ryder C. Winck, Wayne Book, “A novel approach to fabric control for automated sewing”, ResearchGate, Conference Paper, August 2009.
- juki.co.jp/en/products/industrial/, cited on 9 November 2020
- Helder Carvalho, João Monteiro, “Automatic presser-foot force control for industrial sewing machines”, Article in International Journal of Clothing Science and Technology, February 2012.
- Nadine Ruyle Latrhop, “Automation and mechanization in the apparel industry in the state of Washington”, May 4, 1973.
- Helder Carvalho, Fernando Ferreira, Patricia Mellero , Sandra Biegas, “Monitoring and control of industrial sewing machines”, International Conference on Engineering, Technology and Innovation (ICE/ITMC), June, 2017.
- https://textilespedia.blogspot.com/2020/08/production-systems-in-garment-industry.html, cited on August 24, 2020.
- Venu Varukolu, B.Tech., “TECHNOLOGY ADOPTION OF INDIAN GARMENT MANUFACTURING FIRMS”, Osmania University, 2003 August, 2007.
- Bansari Shetye, Pooja Randive, Snehal Shedbale, “Automatic T-Shirt Folding Machine”, International Research Journal of Engineering and Technology (IRJET), Volume: 06 Issue: 04, Apr 2019.
- Technical Systems Ltd UK, “Automation for Industry Specialist, TS-10 , Semi-automatic machine”, http://www.technical-systems-uk.com/Baggingrange.htm.
Article By:
Dr. Pravin Ukey
Akash Deshmukh
Trupti Pawar
DKTE Society’s Textile and Engineering Institute, Ichalkaranji