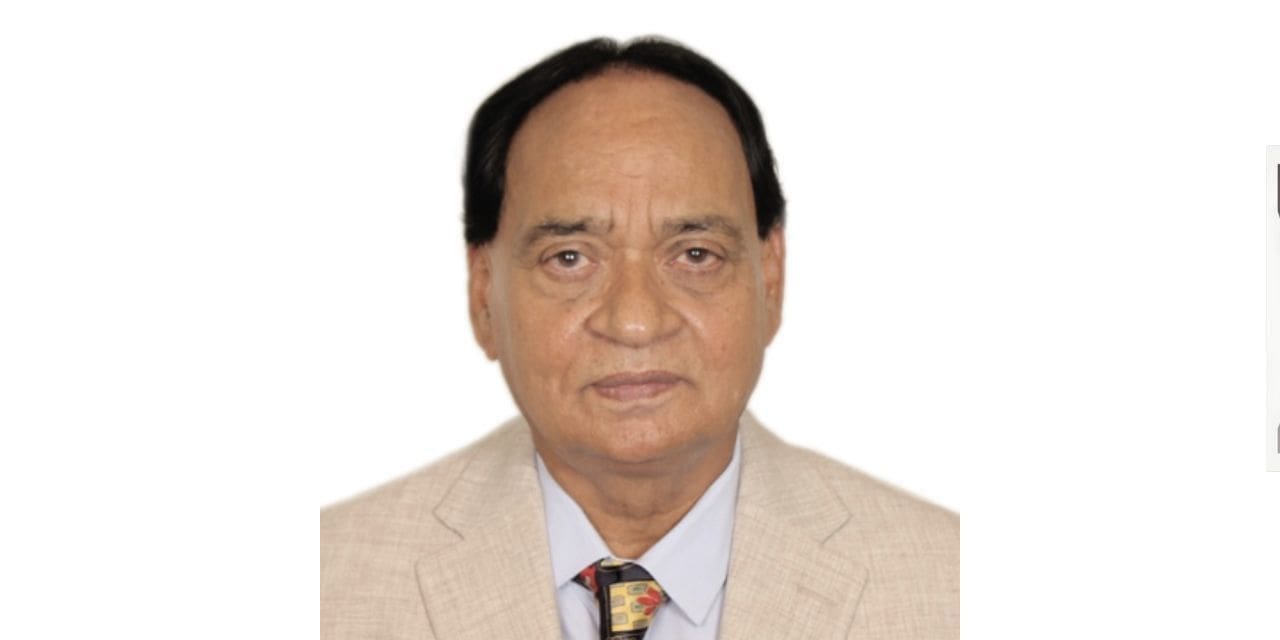
Munish Tyagi
Textile Industry Consultant
Overview of Sustainability in Textile/Apparel Industry
The much discussed ‘Global Climate Change’ is no more a topic for discussion. It has become a reality now with disruptions in global temperature and occurrence of unseasonal rains and floods and storms. The early October temperatures in the cold countries of Canada and North America are touching unusual Day temp. of 20-24°C vis-a-vis past normal of 12-16°C.
The simple reason is extreme carbon footprint around Earth, which comes from manufacturing industries including textiles, caused mainly due to the use of solid fuel emissions and also due to burning of crops and solid and liquid effluents.
The main resources like water, solid fuel energy and of course land, are not renewable and are undergoing depletion. It is therefore high time for the global manufacturing industries especially Textile/Apparel sector, to work on Sustainable processes using new and innovative technologies, recyclable raw materials and sustainable manufacturing process to create products of longer life cycles.
In true meaning, Sustainability in Textile and Apparel sector will mean and require increased focus towards, the concepts of >>Reuse >> Recycle >> Renewal /Regeneration of usable products via ‘post-consumer’ waste reprocessing.
REVIEW OF KEY PROCESSES IN TEXTILES & APPARELS MANUFACTURING
Raw Materials: All textile products like fabrics, apparels, home textiles and industrial textiles are created from different type of raw materials, mostly fibers, that are both natural and synthetic or manmade types. Natural fibers like Cotton, Wool, Jute, Hemp are Bio-degradable and easy to recycle too.
However, natural fibers require extensive use of land and water, but are decomposable and/or recyclable and cane be used to create renewable textile products. The fibers are finally and eventually converted to consumer textiles by the textile mills and under a series of manufacturing processes that consume large amount of power, hence use of solid or agri-fuels. Also, large amounts of water and a variety of chemicals are used. On an average, to create 1 Kg of wearable textile product, we require approximately 150 Ltr. of Water and in case of fashion products like Denim jeans it is about 200 to 300 Ltr. of water for per Kg, on weight basis.
THE MAIN PROCESSES IN CONVERSION OF FIBERS TO CONSUMER TEXTILES ARE:
Yarn spinning: to create twisted yarns for use in making woven or knitted fabrics, or home textiles.
Fabric making: to create woven fabric via Weaving and create knitted fabric via Knitting process; and create Industrial textiles via the new processes of Nonwoven manufacturing techniques,
Fabric Dyeing or Printing: to give colors and designs to consumer fabric to create Apparels & home textiles and eventually make the wearable textiles/apparels through sewing, finishing and making up.
What are core Sustainability issues? vis-a-vis Devil attributes for Textile Raw Materials
BACKGROUND: The Textile manufacturing Value chain starts from the core raw materials that are generally Fibrous and are both Natural fibers e.g.: Cotton, Wool, Silk, Jute, Hemp, others; and also, Manmade or Chemically produced fibres from the crude oil derivates. These are mainly Polyesters, Acrylics, Nylons, Spandex, Aramide filaments, and few similarly produced fibres. Viscose fibers/filaments in different varieties are derived from natural forest base, but consume Land, Forest cover, chemicals and water when converted for use.
Devils for Natural RM: Natural fibres originate from land cultivation or from farm animals like Sheep, Goat, Rabbit, Camel. To sustain their global output, 2 Key Resources are: Land, used for growing or grazing and Water, used for crop irrigation, and continued use of large quantities of water in the manufacturing/chemical processes.
Devils for Synthetic RM: Synthetic or manmade fibres are produced via chemical inputs and the processes for which the basic source is Petro derived polymers. Such manufacturing also requires huge quantity of solid fuels, water and variety of chemicals. In addition, the Biodegradability or the decomposition rate of such polymeric fibres is thousands of years and have serious negative impacts on landfills and ocean resources.
Further, to create usable apparel or industrial textile products, the downstream manufacturing process also consumes huge number of resources like water, power and more chemicals.
The Fast fashion cycles generates more demand recurring production, and post-consumer waste. It is clear that Slow fashion supports both recycling of post-consumer textiles and, thus sustainability.
The core processes in textile manufacturing creating needs for ‘Sustainability Technology’ applications.
Mostly RM /Fibers are supplied to Textile mills for further conversion, in cleaned and pressed Bales, quality-wise, for use in textile manufacturing processes.
Cotton is the thirstiest crop in terms of water consumption, it is also labour intensive and a pesticide-using crop, whereas linen, hemp and viscose use considerably less water and nearly no pesticides.
The Core conversion process are as below:
1]GINNING AND YARN SPINNING: for conversion of fibers to yarns or threads, for further fabric formation.
2]FABRIC WEAVING/KNITTING: for converting spun yarns to usable but raw fabrics via weaving or knitting as per the structure and design etc. Color is introduced later via Dyeing and printing processes.
3]FABRIC DYEING/PRINTING: are Value adding process for adding Colors, as per the chosen design, and create fabrics for their ultimate use of apparel making or for home textile or, as industrial textiles.
4] GARMENT MAKING & PRINTING: Once garments are made from textile fabrics such garments can also be dyed/ printed or embroidered. In case, of denim fabrics, there is special laser treatment to surface.
All the above conversion creates their inherent process waste and which can be Recycled back. It creates high water demand and effluent load in Yarn/Fabric & garment Washing, Dyeing and Printing.
Scope of Sustainability related RM Corrections
RAW MATERIAL STAGE CORRECTIONS via new Technology & Processes.
It is advised to grow high-yielding cottons of varieties that consume less of water or can be grown on semi-arid lands with rain water. This would help to conserve water for more of food and livestock needs.
Also, for cotton, it is important to shift to organic cottons that do not require extensive use of chemicals or pesticides, with use of local livestock manure etc.
For synthetic fibres, the major globally consumed fibres are polyester or viscose types.
While Viscose fibers require huge forest cover of trees such as Eucalyptus, and large volumes of chemicals like Sulphuric acid, salts and water; their consumption has led to the depletion of the Forest cover for such trees in countries like Canada, India etc. New fibers like ‘Lyocell’ and ‘Renew’ are products of green technologies.
Polyester fibers and filament are derived from the polymers produced from petrochemical derivatives, and Textiles of such materials take long to decompose or biodegrade.
There are now ‘Recycling’ technologies that can regenerate such Poly or PET materials from the post-consumer waste of PET drinking bottles, and also from regeneration of Poly fibers from the consumer used and disposed garments. Indian Oil has taken up a initiative to reuse 20 million used and discarded PET water bottles to regenerate Poly fiber to produce uniforms for their 0.3 million workers.
Such recycled Poly fibers are now much in demand and vogue by the MNC apparel brands like Zara, GAP, H&M. And subject to global certification, called G R S label, to establish they are genuinely recycled /renewed.
This is a major Step for reducing Poly waste into landfills or oceans and for Regenerating the ‘same use’ consumer product.
ROADMAP TO SUSTAINABLE PRACTICES IN TEXTILE INDUSTRY
PROCESS WISE:
- Fiber to Yarn Conversion
FOCUS TO BE: Low RM Wastage, Reuse, Recycling, Newer technologies for blending, Regeneration of Polyester from Pet bottles.
- Yarn to woven or Knit Fabric
Reuse of yarn and fiber waste from manufacturing process and re-cycling it with or without blending with the fresh or virgin fibers.
- Fabric to Garment Conversion
Reuse of rejected fabrics and cut Garment waste from manufacturing process; and its regeneration and blending with the virgin fibers.
- All processes to have the Objective to Reduce water intake, energy consumption and to improve biodegradability.
- Use of NEW TECHNOLOGY:
e.g. OE Spinning in Yarn production and Soft Flow /Nitrogen gas Dyeing for Low water use in Fabric Dyeing especially of heavily polluting Indigo dye based Denim fabric and increased use of Digital printing like DTF and DTG. Reducing the Fast fashion to Slow one, will further support above mentioned technologies.
SOME TEXTILE TECHNOLOGIES TO DRIVE SUSTAINABILITY IN COMMON MANUFACTURING PROCESSES IN TEXTILE PRODUCTION.
There are many newly available contemporary technologies to enhance the Sustainability efforts and practices for many core processes in Textile manufacturing. These cover the Core process from fiber to Apparel production:
1] For GARMENT MANUFACTURING: e.g.: Lesser use of laser for Denim effects and greater use of Digital printing, DTF and DTG, in case of Fast Fashion
2] For YARN SPINNING AND FABRIC MANUAFCTURING: recycling of Cotton waste in Ring Spinning and OE process, and its further utilization as RM for Medical Cotton and Non-woven fabrics.
3] For VALUE ADDING DYEING AND PRINTING PROCESS: the enhanced focus to be on minimizing use of Fossil fuels e.g., replacement coal by Gas; and also adopting New types of dyeing technologies like Nitrogen or water less dyeing to substantially reduce the Effluent load on external environment.
4] For REDUCING/REVISING CONSUMPTION OF RAW MATERIALS BY REGENERATION OF POST CONSUMSER TEXTILES: e.g. via Garment tearing up, to regenerate fiber and produce yarns and fabrics such textiles are now in demand.
KEY TAKEWAYS FOR ENHANCED AND BETTER SUSTAINABILITY: THE WAY FORWARD TO BE
The Core pillars and Road Map of Sustainability practices are to be with Key Take Away as below:
- To adopt and increase the proactivity and greater use of Recycling textile wastes, and to Regenerate fibers from post-consumer or used textiles. Recycled Poly fiber is great success…
- To adopt and increase the Alternate sources of energy generation e.g., Solar power for running the machinery and/or natural Gas versus solid fuel/coal for Boilers to produce Steam for Dyeing.
- To renew and replace the used-up Forest cover, e.g. for creating pulp resources for Viscose fiber industry and also to recycle the viscose used apparels to regenerate usable Fiber.
- To adopt high yield Cottons, exceeding 1000 Lb output per Hectare land and minimise the consumption of huge amounts pesticides cotton growing, via going for organic cottons.
- To adopt and practice Low water consuming technology like soft flow dyeing for fabric dyeing, and Digital Printing for printed fabrics; and new coming up Nitrogen dyeing for high polluting and water consuming Denim Jean manufacturing. And use of ZLD plant with RO recycling.
- And finally, to move back to Slow fashion with vis a vis Fast fashion. In case of Polyester uses, to adopt the available technologies to regenerate Fiber from used PET bottles.