Shashi Kumar, National textile Corporation Ltd. and Dr.D. V. Raisinghani
Textile Manufactures Dept.,
Veermata Jijabai Technological Institute
Mumbai- 400019.
Abstracts:
Today sports in India have gained significant importance as a career option as well as leisure and fitness activity. Participation in various national and international games such as Olympics, Commonwealth Games, Asian Games, and Wimbledon etc. is being encouraged by the government as well as work organizations. The performance of a participant in any sport is dependent not only on his physical strength and training but also on the quality of the sports goods and comfort provided by sports fabric. A failure of sports goods may lead to a major injury to the sportsman hence the designing of present day sports product requires high precision, good comfort and safety features. The present paper reviews the influence of design characteristics of sports fabric especially canopy fabric on air permeability, one of the major factors affecting the performance of sport fabric. Air permeability plays a significant role in sports-wear as well as canopy fabric (i.e. parachute, sails cloth, tent fabric, etc.). The air permeability of a fabric is influenced by the structural properties of fiber, yarn, fabric and finishing treatments. Various studies have been carried out by number of researchers to understand the influence of different parameters on air permeability.
Keywords: Air-permeability, Comfort, Sports fabric,Parachute
Introduction: Today sports in India have achieved a peak in terms of popularity and as a career option. From Tendulkar, Paes, Bhupathi, Anand, Karthikeyan to Sania Mirza lead the present sports generation of India. Cricket, Hockey, Football, Boxing, Tennis, Weightlifting, Kabaddi, and Archery are the sports of India that have been deep seated into an Indian psyche, whether of a sports person or a sports lover. Not only physical strength, power and satisfaction but also a strong alternative of recreation; sports in India have covered a long way towards the road of success and have made themselves a hallmark in the world of sports. Due to increasing interest and participation in the sports and leisure activities, the consumption of sports goods and equipment and attendant consumption of textiles in such goods and equipment has shown steady increase. With increase in the number of participation in sports, the number of injuries and fractures also increases. Although many injuries seem unavoidable but many of them can be avoided by introduction of good quality along with standard materials and improvement in the existing sports protective wear and equipments. Today’s sports demand high performance equipments and apparel. Today, technical textile products can be manufactured tougher than wood, stronger than steel, breathe like skin, waterproof like rubber, lighter like feather and at the same time they can be eco-friendly as well as highly economical. Introduction of light weight and safety features in sports textile have contributed significantly for their substitution for other materials. One of the main functions of clothing is to keep the human body comfortable. All types of clothing like sports, defense or protective apparel require comfort property. The comfort achieved from sports wear depends on the complex interaction between a range of physiological, psychological and physical factors. The physical aspect of comfort includes water-vapour résistance, air permeability, moisture holding ability, wind resistance etc. The present paper focuses on the air transport properties and various factors affecting it for sportswear fabrics.
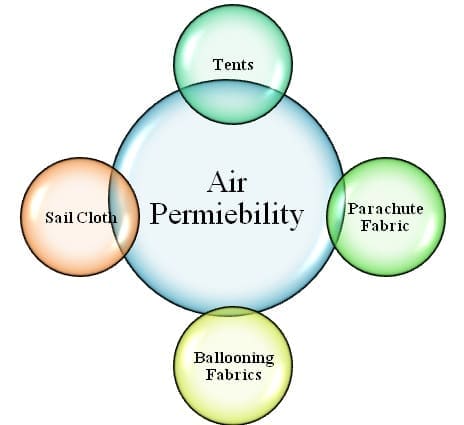
Fig1. Requirement of Air Permeability in different sports application.
Air Permeability is one of the important property that has significant influence on the utilization of fabric for some technical and clothing applications. Air permeability plays a very vital role in the properties of fabric for various sports application like fabric for parachute, sail cloth, tent cloth, filter fabrics, underwear products, socks and other garments. It gives an indication about the breathability of clothing fabrics. Air permeability also affects the thermal properties of textile materials that influence the thermal comfort of human body for proper body temperature[1]. Passage of air is important for a number of fabric end-uses such as raincoats materials, shirting, down-proof fabrics and air bags.
Air permeability is defined as the rate of air flow passing perpendicularly through a known area under a prescribed air pressure differential between the two surfaces of material as per the Indian Standard test method for air permeability of textile fabric[2] Or it is define as the volume of air in milliliters which is passed in one second through 100 mm2 of fabric at a pressure difference of 10 mm head of water[3] Or it is defined as the volume of air in liters which is passed in one minute through 100 cm2(10cm*10cm) of the fabric at a pressure difference of 10-mm head of water [BS EN ISO 9237 1995].
Air permeability of fabric at a static pressure differential between two surfaces of fabric is generally expressed in SI units as cm3/s/cm2 and in inch pound units or ft3/min./ft2 calculated at operated conditions [2].
Methods used for determining the air permeability: Three principles can be used to measure the ability of the fabric to allow the air passage through it [5].
- Measurement of time required to pass the given volume of air through a given area of fabric.
- Measurement of pressure differential required for air to pass at a given constant volume rate through a given fabric area.
- Measurement of volume rate of flow of air through a given fabric area under a given pressure differential. Most of the instruments are working on this principle. (ASTM D737-96).
The air permeability depends on the size and shape of pores and a number of interthreads channels which are dependent on the structural properties of the fabric. Fig. 2 shows the structure of a simple plain woven fabric with four different air flow regions.
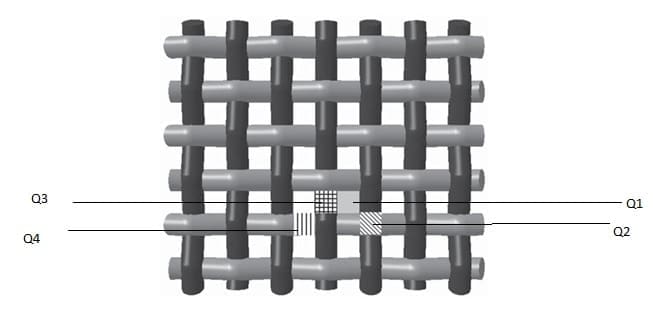
Fig 2: Flow region in woven fabric.
- Flow rate between warp and weft yarn(Q1)
- Flow rate through the interaction point of warp &weft yarn(Q2)
- Flow rate through the fibers of warp yarn(Q3)
- Flow rate through the fibers of weft yarn(Q4)
It has been found experimentally that permeability of inter-yarn pores (Q1) dominates the total air permeability of the fabric but the air passing through the interstices of the fibers or filaments (Q2) are equally important. So taking into consideration all these regions basically the air permeability depends on the structure of the fabric, the main structural parameters being fabric densities, yarn denier, weave [4].
Factor affecting air permeability: The permeability of fabric may be considered mainly in term of three factors (a) the cross-section area of each void (b) thickness of fabric or the depth of each void (c) numbers of voids per unit area [6]. So we can give a statement that fabric air permeability depends on the porosity of the textile materials where as the porosity of fabric is a function of raw material, yarn type, fabric construction, working condition of loom like speed, and other parameters [7]. However it is known that fabric porosity and permeability are not uniform throughout the width of the loom from nozzle to feeler side in case of fabric woven on airjet loom. It is different in centre part of fabric compared to both the selvedge sides and due to this reason, the user cannot utilize the full width of the fabric to their end product.
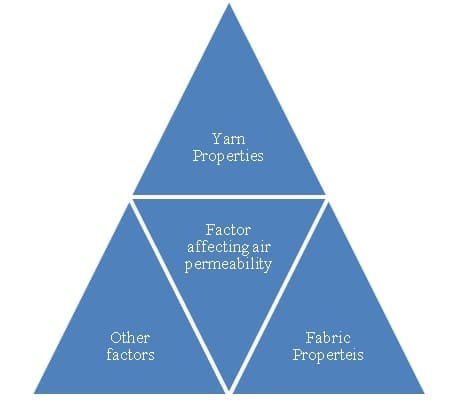
Fig 3: Factors affecting the air permeability
Table 1: Different factors affecting the Air permeability.
Yarn Properties | Fabric properties | Other factors |
Yarn Type i.e. Monofilament, multifilament or Spun | Weave | Area of test sample |
Denier | EPI & PPI | Pressure head on testing machine |
Yarn Twist | Tension and crimp in yarn | Finishing and laundering |
Yarn Type: Monofilament yarn does not allow the air to pass through it. The air can pass through the pores of the fabric created through the interlacement of warp and weft yarn during weaving. Whereas in multifilament yarn a number of filaments are there in a single yarn. So the presence of gaps in between the filaments or within the yarn allows the air to pass through it. This directly affects the total air permeability of the fabric. In the ribbon form of twist-less or zero twist multifilament yarn these gaps can be seen easily with the help of microscope. The effect of number of filaments in a yarn structure on the air permeability needs to be studied.
Yarn Twist: Twist plays an important role in air permeability of a woven fabric. As the level of twist increases, the regularity and circularity of yarn increases which tends to reduce the yarn diameter as well as the cover factor of fabric. The decrease in the diameter of yarn due to increase in twist results in an increase in the air permeability of fabric [9]. An increase in twist level of yarn beyond a limit, results in more circular and high density yarn structure. These types of highly packed tight yarn reduce the air permeability of the fabric in a tightly woven structure after weaving[10].
Denier: Coarser yarn produce thicker as well as higher GSM fabric. The weight of fabric (GSM) also increases with more number of threads in single unit area. If the GSM of fabric is kept constant and the yarn diameter and yarn density or the both parameters reduced, the air permeability gets reduced because of decrease in pores size of the fabric that tends to reduce the air permeability [9].
Weave: The air permeability cannot be given for a particular type of fabric structure or weave with great accuracy as a small change in the parameter of yarn and construction results in considerable change in the permeability of fabric. However, plain weave always exhibits high air permeability. Due to more number of interlacement points in plain fabric, the total size of voids increases that leads to increase in the permeability of the material.
Thread Density: More the number of ends and picks per cm of the fabric, tighter will be the fabric structure that leads to reduced size of pores in the woven fabric. The experiments done by Clayton[6] shows the effect of warp crimp and GSM of the fabric with change in picks per inch keeping all other parameter (like EPI, warp/weft count, weft crimp) constant on air permeability of fabric.
Tension and crimp in the yarn: It is important to measure and minimize the yarn tension variation and keep it as low as possible for textile processes. During the process of weaving, low warp tension results in an unclear shed formation for picking while high tension in the warp thread cause yarn breaks. So it is important to optimize the warp and weft tension for improvement in the efficiency of the machine as well as the fabric qualities. Warp tension and its variation depend upon yarn stress, fabric formation, warping speed and tension variability, and machine types[7] [11].
It is known from the previous researches that tension in the warp threads varies across the fabric width and it is higher in the central zone than in edges. These changes in tension cause the crimp variation in the threads over the whole warp sheet in grey fabric[12]. The change in the crimp % changes the air permeability of the fabric along the width of fabric. As discussed there is linear relationship between total pore size and the air permeability of the fabric. The change in air permeability may be due to the distortion in the pores/voids or the variability in the pore size.
Another reason for effect on air permeability is the filling tension of the weft yarn. For grey fabric it is found that higher average filling tension produces larger opening in the fabric that gives better penetration of air through the fabric resulting in an increase in air permeability[13].
Pressure head on testing instrument: The pressure head on testing instrument and air permeability has linear relationship. As we increase the pressure the air permeability of the fabric increases for all other parameter kept constant. Hence, the air permeability of the fabric has to be determined at different pressure level depending on the type and end use of the fabric.
Laundering and Finishing: In allwet processing the shrinkage of fabric takes place in both warp and weft direction due to relaxation of filament in the yarn as well as in the fabric. The shrinkage results in change in the structure of pores/voids as well as in the fabric in both the directions. The voids shape in grey fabric is generally rectangular and larger than the finished fabric. The warp ends are closely packed due to circular cross-section where as in finished fabric the shape of yarn is much flattened so the void space is smaller that causes change in the dimension of the voids in the fabric. So reduction in the void dimension is the main reason for reduction in air permeability of the fabric.
Calendaring: According tostudies it has been found that this process has high influence on reduction in the porosity as well as air permeability of the fabric. The reason for the change in structure of pores may be flattening of the vertical diameter of low twisted yarn to a great extent and increase in the horizontal diameter of the interlacing yarn. The change in porosity depends on the calendar pressure. The air permeability can reduce up to 35-70%. So calendaring is found to be a very effective tool to reduce the air permeability but unfortunately the strength of the fabric has adverse effect of it. It has been studied by Bardhan in 1979 in detail for nylon parachute fabric[14].
Conclusion:
From above discussion it is clear that air permeability and pore size are strongly related to each other. If the fabric has very high porosity it can be assumed that it will be permeable. Air permeability of the fabric is not only influenced by air flow rate between yarns but also between fibers . Warp and weft filling tension also have the influence on the air permeability. More the tension, higher will be the air permeability due to better penetration of air through the larger openings produced by yarn. So it is important to maintain the tension variation as low as possible. All the wet processes result in variation in air permeability of fabric. Calendaring is the most common process that reduces the variation of air permeability of the fabric after finishing but this process also leads to reduced strength of the fabric.
References:
- Ogulata R.T, Serin(Mavruz), Total porocity, theoretical analysis and prediction of air permeability of woven fabrics, The Journal of the Textile Institute, June (2012);Vol. 103, No. 6, 654–661.
- Indian standard test method for AP of textile fabric.
- Saville B.P, Physical testing of textiles, Woodhead Publishing Limited.
- Fatahi I, Yazdi AA., Predicting Air Permeability Property Values from the Parameters of Weave Structure, Fibres & Textiles in Eastern Europe( 2012), 20, 3(92): 78-81.
- Goglia M. J, Air permeability of parachute cloth, WADC Technical report, Nov. (1952)283.
- Clayton, F. H. “The Measurement of AP of the fabric”, The Journal of the Textile Institute, (1935), 26, T171.
- Kotb N., Ei-Geiheini A., Investigating the influence of the widthwise warp-end tension variation on fabric performance properties, Autex (2009) world textile conference.
- Malasius R,Rukuizieene Z, Investigation of correlation of fabric inequality in width with fabric shrinkage, Fibre and Textile in Eastern Europe July/Sept.(2003), vol.11, No. 3(42).
- M.K. Bardhan, Air permeability of nylon parachute canopy fabric, Man-Made Textile In India, August, (1981).
- HU Jinlian, Fabric testing, Wood head publishing Limited, (2008).
- Adanur, S., Gowayed,Y., Thomas, H., Ghosh, T., Esad, M., and Qi, J., On-line measurement of fabric mechanical properties for process control, Natural Textile Center annual report, final report, November(1999), I96-A09, p.p.1-9.
- Ozkan G., Eren R., “Warp Tension Distribution Over The Warp Width and Its Effect on Crimp Distribution in Woven Fabrics”, International Journal of Clothing Science and Technology, (2010),22(4), pp:272-284.
- Adanur, S, and Qi, J., Property Analysis of Denim Fabrics Made on Air-jet Weaving Machine. Part II: Experimental System and Tension Measurements, Textile Research. Journal (2008); 78, 10.
- M.K.Bardhan, Effect of weaving and processing on the fundamental properties of parachute fabric, Man-Made Textile in India, May, (1979).