B Sathish Babu a
a Department of Textile Technology, PSG Polytechnic College, Coimbatore – 641004, India
Email: sathishbabu_babu@yahoo.com
P Senthilkumar b
b Department of Textile Technology, PSG College of Technology, Coimbatore – 641004, India
M Senthilkumar a
a Department of Textile Technology, PSG Polytechnic College, Coimbatore- 641004, India
ABSTRACT
The properties of any clothing is decided by the constituent of its fibres, yarn and fabric structure. As clothing it should satisfy the wearer both in functional and aesthetic aspects. Thermal comfort is related to the temperature of the body and micro environment between the fabric layer and the skin. The heat generated by the human body during strenuous activity must be dissipated to the external environment through the clothing. So the clothing worn next to skin should have the property of transferring the perspiration from the skin and to transfer the moisture to the atmosphere thus making the wearer to feel comfortable. Moisture transfer refers to the transfer of both moisture vapour and perspiration away from the body. The influence of tuck density on thermal comfort characteristics of double – face knitted fabrics has been studied with 120 denier cotton grey yarn and 240 denier polypropylene yarn. Five different double-face fabrics of 6´9 double-face fabric, 6´6 double-face fabric , 3´3 double-face fabric, 9´9 double-face fabric and 12´9 double-face fabric were produced using high speed double circular knitting machine with inner layer as polypropylene fabric and outer layer as cotton fabric. With respect to tuck density, 6´9 double-face fabrics show better results for moisture transfer characteristics. The number of tucks per square centimeter influences the moisture transfer characteristics of double-face knitted fabrics.
KEYWORDS: Double-face fabrics, Tuck density, Wetting, Wicking, Moisture vapour
transfer
- INTRODUCTION
Moisture transfer in a fabric performs a key role in maintaining the body heat at ambient body temperature of 370C which is essential for a fabric in deciding its comfort level. Whatever heat the human body produces must flow out through the fabric via the body surface by conduction, convention and radiation. Sport which involves higher level of physical exertion causes the body to sweat and it should be evaporated in making the body cool. So the clothing must ensure a higher level of moisture transmission. Fabric must have the property of transferring the sweat out of the body and making the wearer to feel comfortable. So moisture transfer can be defined as the ability of a fabric to transport moisture away from the skin to the fabric outer surface and to release it into the surrounding air. Hence wetting, wicking and moisture vapour transmission characteristics are the critical aspects of a fabric in deciding the clothing comfort of the wearer.
In functional fabrics, to maintain high moisture, cotton fibres are used to maximize the moisture transfer. Double layered knitted fabrics with polypropylene yarn as inner layer and cotton or viscose yarns as outer layer makes the wearer more comfortable during strenuous activity 1. The mechanism of moisture transfer through clothing during transient conditions play a key role in deciding the dynamic comfort of the wearer 2. A high level of comfort can be achieved by producing a double-face knitted fabric. In the double-face knitted fabric, the parameters can be selected independently of one another for both the inner layer and outer layer 3. In double-face knitted fabrics, the inner layer can be preferred as hydrophobic synthetic filament yarn which has good capillary action and outer layer can be hydrophilic yarn which absorbs the moisture and allows it to evaporate 3. The comfort properties of bi-layer knitted fabrics with cotton/polypropylene bi-layer knitted fabric and tencel/polypropylene bi-layer knitted fabric were studied and found that tencel/ polypropylene bi-layer knitted fabric shows better results for wetting, wicking, water absorption, moisture vapour transfer, dryness, thermal conductivity and air permeability characteristics and recommended for sportswear 4. The moisture management and thermal absorptivity properties for double-face polypropylene cotton knitted fabrics were studied and found that inner polypropylene layer transmits quickly the moisture to the outer cotton layer. Due to this faster rate of moisture transfer from the polypropylene layer, both the moisture content and wetted area on the polypropylene side found smaller than the cotton layer. Polypropylene-cotton knitted fabric easily transfers the perspiration by keeping a dry warm feeling to the wearer 5. The comfort and thermo physiological characteristics of multilayered fabrics with various woven and knitted fabric combination by using cotton, lyocell, polyester and polypropylene were studied and found that cotton/polypropylene plaited fabric and cotton/polyester plaited fabric shows better results for air permeability, thermal conductivity, water absorbency, water spreading rate, water vapour permeability and wickability and recommended for use during cold climatic conditions 6. The thermal comfort properties of bi-layer knitted fabric structure for volleyball sportswear were studied and found that bi-layer knitted fabric made with polypropylene as inner layer have better moisture transfer characteristics when compared with plated and single jersey structure 7. The moisture-management properties of bi-layer knitted fabrics for sportswear were studied and found that the micro-fibre polyester and modal bi-layer knitted fabric shows better results for moisture management property 8. In this study, the influence of tuck density on moisture transfer characteristics of double-face knitted fabrics produced with different tuck density is analysed.
- MATERIALS AND METHODS
2.1 Production of double-face fabrics
In order to study the influence of tuck density on thermal comfort characteristics of double-face knitted fabrics, cotton grey yarn of 120 denier and polypropylene dope dyed yarn of 240 denier were selected for the study. Five different double-face fabrics were produced from 120D C/240D PP as 6´9 double-face fabric, 6´6 double-face fabric , 3´3 double-face fabric, 9´9 double-face fabric and 12´9 double-face fabric. The polypropylene yarn selected were multifilament dyed yarn of 24 filaments and the cotton of combed hosiery grey yarn. The selected yarns were knitted using high speed double circular knitting machine of 20 gauge with speed of 25 rpm to produce five different double-face fabrics containing 3 mm stitch length having tuck stitch at every 6th wale and every 9th course, tuck stitch at every 6th wale and every 6th course, tuck stitch at every 3rd wale and every 3rd course, tuck stitch at every 9th wale and every 9th course and tuck stitch at every 12th wale and every 9th course of the fabric with inner layer as polypropylene fabric and outer layer as cotton fabric. The basic structure of double-face fabrics produced is plain single jersey structure having two layers connecting them by introducing tuck stitch. Production of the five different fabrics was made by changing the cylinder and dial needle arrangements. Production of 6´6 double-face fabric is explained in section2.2. All other four fabrics were produced in the similar manner.
2.2 Production of 6th Wale and 6th Course Double-Face Fabric
The dial needle arrangement, cylinder needle arrangement, needle set out and cam set out for producing double-face fabric having tuck stitch at every 6th wale and every 6th course are discussed below.
Dial cam has two tracks. The Short and Long needles move in track 1 and 2 respectively. Cylinder cam has four tracks, out of which the small and medium needles move in track 1 and track 2 respectively, long needles move in track 3 and no needle has been placed in fourth track of knitting. This is shown in the dial and cylinder needle arrangement in Table 1 and Table 2.
As shown in Figure 1.a every 6th needle of the cylinder produces a tuck stitch in wale wise with the corresponding 6th needle of the dial (i.e.) cotton yarn goes in to the loops of polypropylene yarn to produce double-face fabric. That is the cylinder needles 1, 7, 13, 19…1867 from track 3 produces tuck stitch due to the presence of tuck cam. The cylinder needles of 2-6, 8-12, 14-16, 20-24…1872 needles produce knit stitch due to presence of knit cam.
Needle set out for 6th wale and 6th course double-face fabric
Where, X- No of Needles in Wale wise, Y- No of Feeders in Course wise
Figure 1.a Needle set out diagram of 6th wale and 6th course double-face fabric
As shown in Figure 1.b, Out of 36 feeders, the cylinder needles were controlled by tuck cam in 2nd, 14th and 26th feeder. Thus the cylinder needles produced tuck stitch with the dial needle. (i.e.) cotton yarn goes in to the loops of polypropylene yarn at every 6th course to produce the double-face fabric of 6th wale and 6th course knitted structure.
Cam set out for 6th Wale and 6th course double-face fabric
F1 | F2 | F3 | F4 | F5… | F14 | F15.. | F26 | F27…. | F36 | |
DN1 | – | ´ | – | ´ | – | ´ | – | ´ | – | ´ |
DN2 | – | ´ | – | ´ | – | ´ | – | ´ | – | ´ |
CN1 | ´ | – | ´ | – | ´ | – | ´ | – | ´ | – |
CN2 | ´ | – | ´ | – | ´ | – | ´ | – | ´ | – |
CN3 | ´ | O | ´ | – | ´ | O | ´ | O | ´ | – |
Where – : Miss Cam, ´ : Knit Cam, O : Tuck Cam
Figure 1.b Cam set out diagram of 6th wale and 6th course double-face fabricKnitting loop formation of double-face fabric
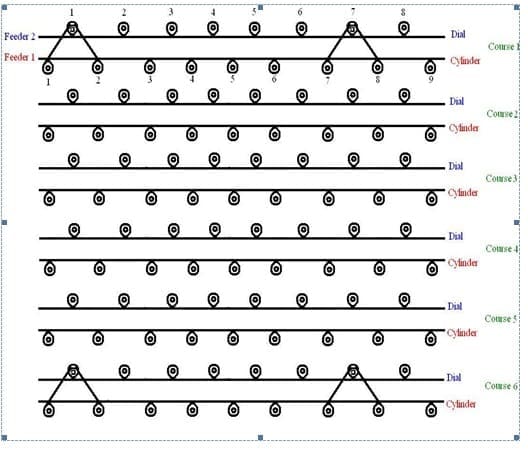
Figure 1.c Knitting loop formation of 6th wale and 6th course double-face fabric
As shown in Figure 1.c, the dial and cylinder needle will perform miss and knit stitch simultaneously during fabric production. The cotton yarn from feeder 1, forms miss stitch with dial needle and knit stitch with the cylinder needle. The polypropylene yarn from feeder 2 produces knit stitch with dial needle and miss stitch with the cylinder needle. Every 6th needle of the cylinder in track 3 produces a tuck stitch in wale wise with the corresponding 6th needle of the dial due to the presence of tuck cam. As the cylinder needles are controlled by tuck cam in 2nd, 14th and 26th feeder, the cylinder needle produces tuck stitch with the dial needle at every 6th course to produce 6th Wale and 6th Course double-face fabric.This cycle was repeated throughout the knitted fabric production.
As discussed in production of double-face fabrics (Figure 1.a, 1.b and 1.c) having tuck stitch at every 6th wale and every 6th course, similar arrangements of dial needle arrangement, cylinder needle arrangement, needle set out and cam set out were followed to produce other four different double-face fabrics having tuck stitch at every 6th wale and every 9th course, tuck stitch at every 3rd wale and every 3rd course, tuck stitch at every 9th wale and every 9th course and tuck stitch at every 12th wale and every 9th course of the fabric with inner layer as polypropylene fabric and outer layer as cotton fabric.
The double layered knitted fabrics produced were subjected to hot wash and bleached with hydrogen peroxide at 3% on weight of material at 1000C and dyed with hot brand reactive dye at 5% on weight of material at 900C in winch dyeing machine. Then it was washed and dried in a stenter at 1300C and subjected to relaxation for 48 hours. Then the fabrics were tested for its geometrical and moisture transfer characteristics.
- TESTING
The double-face fabrics produced were tested to assess the thermal comfort characteristics. The wettability of the double-face fabrics was measured by evaluating the time taken by the fabric sample to sink completely in water . As per (BS 3424) the vertical wicking test was evaluated. The transverse wicking characteristics were analysed for the double-face fabrics 9-11. The moisture vapour transfer characteristics of double-face fabrics were measured by using ASTM E 96 – cup method. The drying rate was measured for the double-face fabrics 12. Air permeability test was carried as per IS 11056 : 1984. Thermal conductivity test was carried as per lees disc method. The thickness of the double-face fabrics were measured by using thickness gauge as per ISO 5044:1996.
- RESULTS AND DISCUSSION
To study the influence of tuck density on thermal comfort characteristics of double-face fabrics, five different double-face fabrics produced from 120D C/240D PP were used and denoted as 6´9 fabric for 6´9 double-face fabric, 6´6 fabric for 6´6 double-face fabric, 3´3 fabric for 3´3 double-face fabric, 9´9 fabric for 9´9 double-face fabric and 12´9 fabric for 12´9 double-face fabric.
4.1 Geometrical Characteristics
The geometrical properties of double-face fabrics were studied and the average value of 10 samples was given in Table 3.
From the Table 3 it was found that change in tuck density affects the thickness of the double-face fabrics. The 12´9 double-face fabric shows higher values for thickness as compared to other four fabrics.
4.2 Moisture Transmission Characteristics
The moisture transmission characteristics such as wetting, transverse wicking, vertical wicking and moisture vapour transfer of double-face fabrics were analysed and the average values were given in Table 4.
From Table 4 it is seen that with respect to tuck density, 6´9 fabric takes lesser time to sink in water when compared to other four fabrics. The wicking height both in wale wise and course wise direction was higher for 6´9 fabric than other fabrics. The wale wise wicking height was more than the course wise wicking height for all the five fabrics. In transverse wicking and dynamic transverse wicking, the time taken to absorb one drop of water on face side of top layer of 6´9 fabric was lesser than the other fabrics. The area of water spread for one drop of water and the area of water spread to reach saturation was also found to be higher for 6´9 fabric.
4.2.1 Analysis of Wetting Characteristics
The ability of double-face fabrics to sink in water completely were studied and given in Table 4.
From Figure 2.a and Table 4, it is found that 3 x 3 fabric shows quicker sinking time. The fabric transmits the water quickly to the cotton layer which absorbs and spread the water to the entire fabric surface. This makes the fabric to sink in water in lesser time as compared to other four fabrics. When the tuck density of the fabrics is decreases, fabric pores will be increases, which will makes the fabrics to sink quickly. 6 x 9 fabric show optimum value with respect to sinking time. The standard error bar in the Figure 2.a. indicates the significance level of 3×3 fabric with other fabrics with respect to sinking time. Effect of tuck density on wetting behavior of double-face knitted fabrics is significant at 95% confidence level (F calculated > F tabulated: p-value 1.27E-45).
4.2.2 Analysis of Wicking Characteristics
The rate of water spreading due to capillarity were studied and given below.
4.2.2.1 Longitudinal wicking rate
The rate of water spreading on various double-face fabrics were tested both for wale wise direction and course wise direction and given in Figures 2.b and 2.c.
From Figures 2.b, 2.c, the wicking height was analyzed for all the five fabrics in relation to wicking time from 1 minute to 30 minutes. In general, wicking height increases with wicking time in both wale wise and course wise direction for all the five double –face fabrics at all intervals of time. 6´9 fabric having 3.28 tucks per square centimeter has higher wicking height than the other four fabrics.
Wicking height of selected five fabrics increases with decreasing tuck density from 18.12 tucks per cm2 to 3.28 tucks per cm2. After that wicking height of the fabrics was reduced from 3.28 tucks per cm2 to 1.54 tucks per cm2. This trend was observed in all wicking time intervals. Wicking height of the fabrics is higher in wale-wise direction than that of wicking height in course-wise direction. Inter yarn space between and with-in fabrics are increases when the tuck density decreases. This may be the reason for increasing wicking height from 3×3 fabrics to 6×9 fabrics. After that decrease in tuck density from 3.28 to 1.54 tucks per cm 2, makes the fabrics more porous and it doesn’t allow the water to arise. That is why the fabrics 9×9 and 12 x 9 fabrics have lower wicking height. The standard error bar shown in the Figure 2.b and Figure 2.c indicates the significance level of 6×9 fabric with other fabrics with respect to wicking height in wale wise and course wise direction respectively. Effect of tuck density on wicking in wale wise direction of double-face knitted fabrics is significant at 95% confidence level. (F calculated > F tabulated: p-value 3.41E-38). Effect of tuck density on wicking in course wise direction of double-face knitted fabrics is significant at 95% confidence level. (F calculated > F tabulated: p-value 1.4E-37).
4.2.3 Analysis of Transverse Wicking and Dynamic Transverse Wicking Characteristics
The area covered by spreading one drop of water on various double-face fabrics for transverse wicking and dynamic transverse wicking were given below.
4.2.3.1 Area of water spread for one drop of water
The area covered by spreading one drop (1 ml) of water was tested and given in Table 4.
From Figure 2.d, Figure 2.e and Table 4, the water spreading area of the double-face fabrics was measured.
When one drop of water is placed on face side of top polypropylene layer of double-face fabrics, it first interacts with surface and is transported immediately to the next layer. This is because of transverse wicking. During this period water also travels longitudinally. As gravitational force is higher than wetting force, it comes to the next bottom cotton layer quickly without spreading much on top layer. So, it has minimum spreading area. As soon as droplet comes to bottom cotton layer it travels both in transverse and longitudinal directions. Here, wetting force is higher than gravitational force and it also take time to travel in transverse direction. In the mean time, due to wetting force, water moves in longitudinal direction and reaches the bottom layer. That’s why bottom cotton layer has more spreading area than top polypropylene layer.
From Figure 2.d, Figure 2.e, and Table 4, it was found that as 6´9 fabric having 3.28 tucks per square centimetre transmits one drop of water from polypropylene layer quickly to the cotton layer which absorbs and spread the water in cotton layer fabric surface. As it transfers the water quickly the spreading area is found less in polypropylene layer and more in cotton layer. 6´9 fabric spreads the water quickly from polypropylene layer to cotton layer with minimum spreading area of water on polypropylene layer surface and maximum spreading area of water on cotton layer surface than the other four fabrics. This is real moisture management behavior of the double faced fabrics. It was achieved with the 6´9 fabric. The spreading of water at the back side of bottom layer has been measured by cutting the tuck stitches between cotton and polypropylene layers of all the double-face fabrics. The standard error bar shown in the Figure 2.d.and Figure 2.e. indicates the significance level of 6´9 fabric with other fabrics with respect to water spread on face side of top layer and water spread on face side of bottom layer respectively. Effect of tuck density to spread 1 ml of water on face side of top layer of double-face knitted fabrics is significant at 95% confidence level. (F calculated > F tabulated: p-value 1.12E-30). Effect of tuck density to spread 1 ml of water on face side of bottom layer of double-face knitted fabrics is significant at 95% confidence level. (F calculated > F tabulated: p-value 8.09E-43). Effect of tuck density to absorb 1 ml of water of double-face knitted fabrics is significant at 95% confidence level. (F calculated > F tabulated: p-value 1.12E-30).
4.2.3.2 Area of water spread and time taken to reach saturation The area covered and the time taken to reach saturation point of the double-face fabrics were studied and given in Table 4.
From Figure 2.f and Table 4, the water spreading area of the double-face fabrics to reach saturation was measured. From Figure 2.f and Table 4, it was found that 6´9 fabric having 3.28 tucks per square centimetre transfers the water quickly from polypropylene layer to cotton layer and get saturated in minimum time with maximum spreading area than the other four fabrics. As 6X6 fabric has 5.39 tucks per square centimetre and 3´3 fabric has 18.12 tucks per square centimeter the time taken for water to get transfer from polypropylene layer to cotton layer increases with decrease in spreading area. As 9´9 fabric has 2.92 tucks per square centimeter and 12´9 fabric has 1.53 tucks per square centimeter the space between the two layers of these double-face fabrics are very high respectively which increases the water transferring time with decreased water spreading area. The standard error bar shown in the Figure 2.f. indicates the significance level of 6´9 fabric with other fabrics with respect to effect with 3´3 fabric, 9´9 fabric and 12´9 fabrics with respect to area of water spread and time taken to area of water spread and time taken to absorb water in reaching saturation.
Effect of tuck density to spread water in reaching saturation of double-face knitted fabrics is significant at 95% confidence level. (F calculated > F tabulated: p-value 1.16E-66). Effect of tuck density to absorb water in reaching saturation of double-face knitted fabrics is significant at 95% confidence level. (F calculated > F tabulated: p-value 1.96E-50).
4.2.4 Analysis of Moisture Vapour Transfer Behaviour
The rate at which the moisture vapour get transferred to the double-face fabrics were tested and given in Table 4. Number of tucks per unit space influences the moisture vapour transfer behavior of the fabrics. Moisture vapour transfer characteristics of the fabrics are decreasing with decreasing tuck density. Tuck stitch in the fabric allows the water vapour to pass out of the fabric. Moisture vapour transfer measured by weighing method has no significant effect. As 3×3 fabric is porous than 6×6 and 6×9 fabric it allows more moisture to pass through the fabric. As the space between the two layers are more in 9×9 and 12×9 fabrics due to lower tuck density, these fabrics allow less moisture to pass through them. The standard error bar shown in the Figure 2.g indicates the significance level of 3×3 fabrics with other fabrics with respect to moisture vapour transfer. Effect of tuck density on moisture vapour transfer in reduction in height of water of double-face knitted fabrics is significant at 95% confidence level. (F calculated > F tabulated: p-value 3.08E-70). Effect of tuck density on moisture vapour transfer in reduction in weight of water of double-face knitted fabrics is significant at 95% confidence level. (F calculated > F tabulated: p-value 3.38E-64).
4.2.5 Analysis of Drying Characteristics
Drying rate of the double-face fabrics was calculated and expressed as average weight loss over initial water content per unit area. It was the ability of the double-face fabrics to evaporate the moisture present on the fabric surface.
From Figure 2.h it was found that 6´9 fabric has quicker drying time to return to its original weight when compared to other four fabrics. This is due to minimum water holding capacity of the fabric. The trend observed was as tucks per square centimeter increases to 5.39 for 6×6 fabric and 18.12 for 3×3 fabric, the time taken for these fabrics to get dried is found high in these fabrics. As 9´9 fabric has 2.92 tucks per square centimeter and 12´9 fabric has 1.53 tucks per square centimeter the space between the two layers of these double-face fabrics are very high respectively which results in higher drying time in these fabrics. The standard error bar shown in the Figure 2.h indicates the significance level of 6´9 fabric with other fabrics with respect to drying rate. Effect of tuck density on drying rate of double-face knitted fabrics is significant at 95% confidence level (F calculated > F tabulated: p-value 1.78E-54).
4.2.6 Air Permeability Characteristics
Air permeability of the double-face fabrics were tested and given in Figure 2.i. It was found that 3×3 fabric has higher air permeability than the other four fabrics. The air permeability decreases with decrease in tuck density. As 3×3 fabric is porous than 6×6 and 6×9 fabric it allows more air to pass through the fabric. As the space between the two layers are more in 9×9 and 12×9 fabrics due to lower tuck density, these fabrics allow less air to pass through them. The standard error bar shown in the Figure 2.i represents the significant level of 3´3 fabric with other fabrics with respect to air permeability. Effect of tuck density on air permeability of double-face knitted fabrics is significant at 95% confidence level. (F calculated > F tabulated: p-value 2.27E-32).
4.2.7 Thermal Conductivity Characteristics
Thermal conductivity of the double-face fabrics is the ability of the fabric to conduct heat. It is found that there is a good correlation between air permeability and thermal conductivity value of the selected five fabrics. Tuck density decreases with increasing fabric thickness. Fabric thickness is the influencing factor for thermal conductivity. Thermal conductivity of the fabrics increases with increasing fabric thickness. This trend is observed from 3×3 fabrics to 6 x 9 fabrics. After that thermal conductivity values decrease for 9x 9 and 12 x 9 fabrics though the fabric thickness value is in increasing trend. This is may be due to higher entrapped air between layers of the fabrics. The standard error bar shown in the Figure 2.j represents the significant level of 6´9 fabric with other fabrics with respect to thermal conductivity.. Effect of tuck density on thermal conductivity of double-face knitted fabrics is significant at 95% confidence level. (F calculated > F tabulated: p-value 3.26E-39).
5. CONCLUSION
Influence of tuck density on thermal comfort characteristics of double-face knitted fabrics was analyzed. It is observed that 6´9 fabric takes optimum sinking time , higher wicking rate, lesser time in absorbing one drop of water than the other four selected fabrics. In dynamic transverse wicking, 6´9 fabric shows an increase in area of spread on bottom cotton layer than the other four fabrics. Further, it shows lesser time in reaching the saturation point on the fabric surface than the other four fabrics. The fabric shows optimum value with respect to moisture vapour transfer and quicker drying when compared to other four fabrics. 6´9 fabric shows optimum air permeability and higher thermal conductivity when compared to other four fabrics. It is concluded that the tuck density (number of tucks per square centimeter) plays a major role in deciding the moisture transfer characteristics of double-face knitted fabrics to achieve suitability for making sportswear.
6. REFERENCES
- Piller, B. (1986), Integrated multi-layered knitted fabrics- A new generation of textiles polypropylene fibres, Melliand Textilberich, 67, 412-416.
- Das, B. Das, A. Kothari, VK. Fanguiero, R. & Araujo, M. (2007), Moisture transmission through textiles, Part I: Processes involved in moisture transmission and the factors at play, Autex Res J, 7, 100-110.
- Oglakcioglu, N. & Maramarali, A. (2009), Thermal comfort properties of double face fabrics knitted with cotton and polypropylene, Autex 2009 World Textile Conference, Proceedings, 26-28.
- Anbumani, N. & Sathish Babu, B. (2008), Comfort properties of bi-layer knitted fabrics, The Indian Text J, 8, 17-28.
- Gamzen Supuren, Nida Oglakcioglu, Nilgun Ozdil & Arzu Marmarali. (2011), Moisture management and thermal absorptivity properties of double-face knitted fabrics, Text Res J, 81, 1320-1330.
- Kandhavadivu Mallikarjunan, Ramachandran, T. & Geetha Manohari, B. (2011), Comfort and thermo physiological characteristics of multilayered fabrics, J of Text & App Tech & Management, 7, 1-15.
- Suganthi, T. Senthilkumar, P. & Dipika, V. (2017), Thermal comfort properties of bi-layer knitted fabric structure for volleyball sportswear, Fib & Text East Eur, 25, 75-80.
- Suganthi, T. & Senthilkumar, P. (2017), Moisture-management properties of bi-layer knitted fabrics for sportswear, J Ind Text, DOI:10.1177/ 1528083717692594.
- Sampath, MB. & Senthilkumar, M.(2009), Effect of moisture management finish on comfort characteristics of micro denier polyester knitted fabrics, J Ind Text, 39, 2,163-173.
- Sampath, MB. Aruputharaj, A. Senthilkumar, M. & Nalankilli, G. (2012), Analysis of thermal comfort characteristics of moisture management finished knitted fabrics made from different yarns, J Ind Text, 42, 1, 19-33.