Introduction:
In today’s world, micro-scale and nano-scale devices are extensively used in various optic, electric, semiconductors, mechanical, chemical, pharmaceutical applications. At the heart of this technology are the Micro-electric and mechanical (MEMS) sensors. MEMS can be defined as a miniaturized system with characteristic sizes ranging from 100nm to 1mm containing a combination of electric and mechanical components. The MEMS fabrication technology involves a micro-machining process that selectively etches away parts present in the silicon wafer and adds new layers of electrical and mechanical components. That creates a major difference between the traditional IC manufacturing that only fabricates electric components like conductors and insulators versus MEMS which provide a combination of electric and other mechanical elements such as Gears, Cantilever, beams, diaphragms, etc. These micromachines can be used as both sensors and actuators along with a combined application as transducers depending on the specific requirements. Nowadays, advanced research is happening in the field of smart sensors that are systems reacting passively or actively to a given stimulus.
Coming to the working principle of a MEMS sensor, it is based on the change in physical energy of any movable structure like a cantilever, gear, or membrane due to the application of an external force. This deflection in energy is measured using an optimal electric or optical technique and is finally used to back-calculate the applied external force. The different domains of physical energy can be categorized as Mechanical (Length, area, volume, torque, pressure), Chemical (Concentration, enzyme selectivity, spectroscopy, composition), Thermal (Temperature, entropy, heat flow), Electric (Voltage, resistance, inductance, capacitance, polarization, piezoresistive effect, dipole moment, etc.), Magnetic (permeability, flux density, field intensity,magnetic moment,) and Radiant (Intensity, Wavelength, Refractive index, transmittance).
Types and Application of MEMS:
Due to their high sensitivity, accuracy, reproducibility (manufacturing at scale), reliability, and reduction in costs, MEMS are used in various applications.
1) MEMS Accelerometers – These are micro-devices used to measure force and acceleration. Two broad categories are piezoresistive and capacitive. Variable Capacitive (VC) sensors are low range, highly sensitive devices whereas piezoresistive (PR) sensors are higher range, low sensitivity devices.
They are widely used in smartphones to switch tabs or pocket-mode operations, gravity sensors, digital compass, GPS Tracking.
2) MEMS Gyroscopes – These are micro-devices that measure angular/rotational motion (Revolution per second RPS) or displacement of an object. Physically they can be assumed as spinning wheel/disc/beam mounted on an axle that is free for rotation and contains an oscillating component to detect acceleration.
They are widely used to ensure safety in vehicle stability, image stabilization, airbag systems, automatic roll-over prevention, car navigation, and also photography and industrial robotics.
3) MEMS Pressure Sensors – Based on the type of measurements and pressure requirements, these micro-devices are further classified into Absolute pressure sensor, Vacuum pressure sensor, Sealed pressure sensor, Gauge pressure sensor, Differential pressure sensor. These sensors are used to calculate the external pressure and have a huge demand in defense, medical, aerospace, industrial, automotive, beverage applications. For e.g. The MEMS pressure sensor can be used to measure the fluid pressure in humans in case of a brain hemorrhage. Due to their small size, they easily get inserted into the human body compared to macro-devices.
4) MEMS Magnetic field sensors – Magnetic MEMS are used to detect and measure the electromagnetic interactions between magnetic materials and active or passive sources of the magnetic field. The change in magnetic force causes a change in voltage frequency. These sensors are extensively used in linear angle, linear speed, and position measurements in the industrial, consumer, and automotive industries.
Some other types include:
5) MEMS gas sensors – Micro-devices used to detect different types of gases and their concentration.
6) Bio MEMS- Micro-scale sensors used for biological and biomedical applications that may or may not have direct electric or mechanical functions. Examples include implantable microelectrodes used to send and detect nervous signals for enhanced disease identification and monitoring clinical parameters, microtools like microneedles, tiny forceps that are used for surgeries, drug delivery, vaccination, etc.
Need for sensors in the Textile Industry:
The field of textile is not just limited to manufacturing apparel. Textile is a machine and research-oriented field which always has the need for technological development towards improving accuracy, low cost, less space, eliminating complications. MEMS can have applications in the following sectors of textile: Ginning, spinning, weaving, wet processing, knitting, apparel manufacturing, technical textiles,Polymer matrix composites, textile testing, fiber formation etc.
Application of MEMS in Textile : Specific Applications
1. Warp break detection in Weaving:
Drop wire pins are used on weaving loom in order to stop the machine during end break. Whenever the yarn breaks, the drop pin falls on the serrated portion and stops the machine. The yarns in the warp sheet remains in continuous contact with the metallic drop wires, and thus it results into hairiness and deterioation in the qualityof the warp yarns. Therefore, in order to improve productivity and achieve lesser yarn defects, MEMS can be used for sensing the warp-end break without having any contact with the warp yarn.
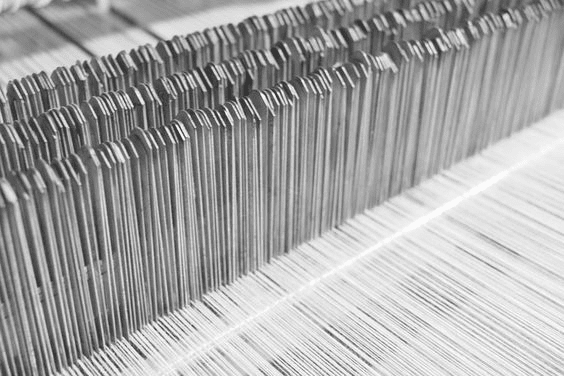
Source: https://www.batesmillstore.com/
2. Relative Humidity in Spinning:
It is crucial to maintain proper humidity in the spinning section. If the humidity is higher it may result in drafting roller slippage and lower humidity results in fiber breakage. Hence MEMS sensors, requiring lesser space and higher productivity can be used for measuring humidity to get accurate results in order to maintain proper machine settings and conditions.
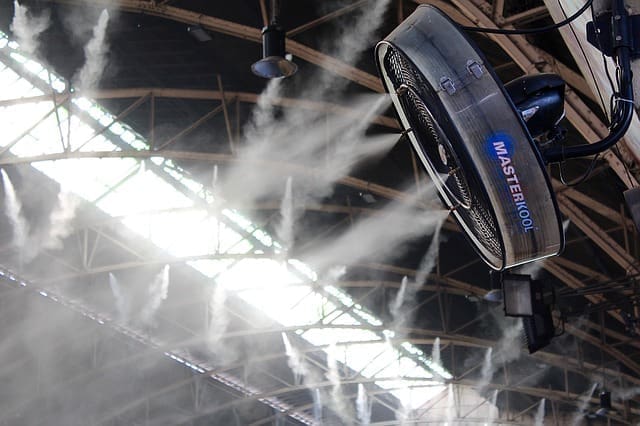
Fig- Humidification system in Industry
3. Smoke Detectors (Ginning, Spinning, Weaving, Wet Processing)
There is continuous friction in textile machineries and materials used in manufacturing are prone to catch fire easily. Having an efficient smoke detector system that detects fire conditions can be achieved with the help of MEMS. These sensors being robust, consuming less power and providing stable electric properties are ideal for applications as miniaturized gas sensors. There are many MEMS-based gas sensors being developed for detecting specific concentration of gases in controlled chambers. They primarily consist of a micro-heater, interdigitated electrodes and a sensing film.
4. Pelvic tilt angle – Medical Textile
Pelvic tilt is considered to be a significant tool to measure pelvic asymmetry which is a distorted alignment of the pelvic bone in the lateral, axial, or anterior/posterior rotational plane. This disorientation is supposed to cause significant complications such as Lower Back Pain (LBP). Conventional silicon-based MEMS accelerometer is considered to be an expensive alternative as a solution to the hazardous radiographic measurement of pelvic tilt angle. A recent research study has proposed a solution of using Silver nanoparticles (AgNPs) as the transducer material to induce piezoresistive effect when stress is applied to the textile. Textile materials are advantageous as low-cost, easily available, lightweight, flexible, and environment-friendly resources for developing sensors that efficiently conform with body contour. [3]
Application of MEMS in Textile : Intelligent Textiles:
Imagine a layer of smart textile material like our skin that can detect change in physical quantities like pressure, temperature and intelligently react towards the environmental stimuli just like our brain. The three main components required for developing such intelligent materials are sensors, actuators, and the controlling units. MEMS sensors play an important role in the research and development of smart textile technology as they sense, control, and can activate mechanical processes on the micro-scale while performing complicated tasks at the macro-scale when integrated as large arrays.
To integrate the MEMS on textile, developing silicon-based flexible skin is a desirable approach. MEMS devices are rigid in general and cannot be bent. But when they are integrated on a flexible silicon wafer consisting of host silicon islands (metals, actuators, sensors), interconnected metal wires to connect processing circuits and polymer layers (sandwiched between silicon islands and metal wires), a flexible silicon sensor skin is developed. These sensors can then be stitched on any textile material and used for developing intelligent textiles.
Some of the interesting possible applications of these intelligent textiles include:
1) Thermally sensitive material: that adapts to the change in temperature. This can be achieved by deriving a textile fibrous material containing bound or cross-linked polymers using different formulations of molecular weight, acid catalysts, and cross-linking raisins. The cross-linked polymer is a phase change material (PCM) that releases or absorbs a significant amount of heat during phase transition and thus helps in temperature adaptability and reversibility. The intelligent thermal memory of these materials can be effectively used to :
a) Increase the wear life of automotive and aerospace components,
b) Healthcare applications like burn therapy and improving skin temperature and circulation in patients.
c) Fabricate remote sensing devices in industrial, agricultural, and horticultural use where detecting this temperature would be useful.
2) Shape-memory polymers: (SMP) are intelligent materials with shape-changing properties that can temporarily fix into a deformed shape and then return back to their original shape on the application of external stimuli. They can sense the change in temperature, pressure, PH, moisture, etc. These polymers find applications in:
a) Developing smart garments that can regulate heat and moisture
b) Wrinkle-free and crease retention fabrics
c) Non-invasive surgeries and technical devices
d) Automotive seat belts that absorb kinetic energy and react with a change in shape.
3) MEMS can also be used to develop intelligent textile material for Chemical/drug-releasing, Photo-sensitive materials, Intelligent coatings.
These are some applications of integration of MEMS technology in textile. With increasing demand for lesser space, low cost and better efficiency, this continues to have a phenomenal scope for research.
Fig-Military Uniforms Fig-Agriculture
Fig-Seat Belt Fig-Burn therapy treatment
References:
- https://www.slideshare.net/Ashishkapoor614Kapoo/mems-sensing-i-textiles
- https://indiantextilejournal.com/articles/FAdetails.asp?id=1742
- https://www.sciencedirect.com/science/article/pii/S1877705812026082
- https://link.springer.com/chapter/10.1007/978-3-642-18293-8_6
- https://www.electronicshub.org/mems-sensors/
- https://www.hitechnectar.com/blogs/different-types-mems/
Authors:
Ms. Sakshi Taori
Mr. Yash Trivedi