Block printing is a technique of decorating fabrics or textiles by using dye powder, thickener and some auxiliary to make the dye fast, where all this process is done by hand. For this study cotton fabric of plain weave was selected. Natural dye source was taken as orange colour stalk of Parijataka flower, its pigment is extracted in the aqueous medium Guar gum thickener was selected for preparation of printing paste .Wooden block of square shape was selected .Printed fabric was allowed to dry for different time scale .Dried samples was treated with the solution of metallic salts ( mordants) such as Feso4, Alum, Al so4, Cuso4 for fixation pigment of Parijataka flowers, colour fastness properties of block printed fabric was tested. It was found that 6- 8 hours drying of block printed samples was found to be effective for transferring of pigment from layer of guar gum thickener and developed bright orange colour on fabric. Selected metallic salts were found to be effective for the dye fixation and also for development various shades dark orange, dry leaf brown, brown and light peseta green. Colour fastness properties were found to be very good to good.
Introduction
Block printing is hand skill, low cost techniques of fabric printing process of surface decoration, beautifying and to attract consumers and also increases the cost of fabric. Printing is also called as application of colour paste on surface of fabric on selected area with machinery or by hand with the use of any devise. Wooden block of carved design of floral and geometrical of any size are now available in market and it also can be prepared as for the requirement of printing article such as pillow cover, table cloth bed sheet and sari and Punjabi dress material. Even after multiple use of wooden block is not spoiled the carved design remain same and care of block is very easy but for each colour separate block is required. Guar is legumes it is also called as cluster bean with the botanical name Cyamopsis tetragonoloba. It is used as vegetable in daily food item in the form of curry. It has also been reported that guar possesses properties which might be useful in warp sizing and in textile finishing operations. The prime function of thickening agent in textile printing is to enable the dyestuff or pigment to be transferred to the fabric at printing stage. Furthermore, the thickening agent must not break down during steaming or any other dye fixation process to such an extent that colour ‘bleeding’ occurs, the thickening agent must be completely removed from the fabric during the washing off treatment given to the printed fabric with dye stuffs. One more further requirement is that the thickening agent must be suitable, compatible with all the other components in the printing paste and it must not be too expensive.( W.Clerk 2004) .An extremely useful feature of modern thickening agents is their ability to be dissolved in cold water with the aid of a high–speed stirrer. In the preparation of thickening agents for use with a particular range of dyestuffs it is often advantageous to incorporate assistants and other chemicals necessary to fix the dye stuff. An additional property of some thickenings is their ability to be coagulated by alkaline solutions particularly where borax is also present. This used to aid dyestuff fixation in two –stage process and prevent dyestuff bleeding or spreading after printing on fabric. Suitable dyes, pigment and thickener selection is very important otherwise effort taken for the printing that spoiled. Therefore for this study natural source of dye , natural thickener , different metallic salts were used to increase the fastness of dye and experiment carried out by considering objective extraction of pigment from orange stalk of parijataka flowers ,optimization different concentration of guar gum, time required for dye transference from gum phase to fabric phase, assessment of handle of printed fabric , effect of mordants on dye fixation and evaluation of colour fastness properties of block printed fabric
Advantage of this study
Synthetic printing thickener is manufacture on chemical base and acrylic paints were used for printing to show the students in the laboratory such as block printing, marble printing, and hand screen printing .The students should be to foot stand and start small scale business for the preparation of hand kerchief , pillow cover, table mats using easy printing techniques ,low cost and more production to earned money .But it was observed that synthetic printing thickener and acrylic paints bottle after used the remaining thickener become hard , not dissolved in any solvent and unable to converts into solution for reutilization for printing. If thick acrylic paints used for the printing spoiled block and miss printing was noticed on fabric. Hence natural thicker “guar gum” was used for hand block printing because it is easily dissolved in water no chemical required for dissolving, if guar gum is dried, it is re dissolved in the normal water for use and easily removed from the surface of the printed fabric by washing. It is advantages as compared to the chemical base printing thickener and easily available in market at low cost.
Materials & methods
Selection thickener
Natural thickening agent guar gum was selected because it is easily dissolved in water and easily removed during washing and it is non toxic it is used in food item in bakery products and it was purchased at the rate of Rs 90/ kilogram
Selection & preparation of fabric
Cotton grey fabric of plain weave 2×1 weave was selected for hand block printing Cotton grey fabric was prepared for printing by desizing, scouring, bleaching and pressed with hot iron for removal of wrinkles to avoid the miss printing .Cut pieces of fabric 10×10 inches in size for conducting block printing trials
Dye source
Orange colour stalk of parijataka flowers were selected because it content orange colour pigment. Botanical name of parijataka is Nyctanthes arbora tristis belonging to the family oleacese parijataka is fabulous plant having high medicinal value. It is commonly known as harsinghar, parijataka in Hindi, night jasmine in English, parijataka flowers white in colour with small size like jasmine of short stalk of orange colour
Collection and preparation of dye source
Flowers of parijataka open in the early morning and dropped down. Flowers collected in the morning ,orange colour stalk was separated from the white petals and the size of stalk is 1 to 1.5 inches and it is tube like with diameter is about 0.15 inch and it was dried in the shade and stored in the plastic tins for further research work.
Extraction of pigment
Dried orange colour stalk of Parijataka flowers were crushed by hand and made in to powder. 50gm of powder was added in the 500 ml of water and allowed to boiled slowly for an about 20 minutes as per the standardized time scale. Extracted pigment was strain and volume of extract was reduced in concentrated form about 150 ml , concentrated extract was allowed to cool in room temperature and used for preparation of printing paste with guar gum.
Mordant
Metallic salt was selected such as alum, aluminum ferrous sulphate, copper sulphate and ferrous sulphate .Post mordanting method was used for dye fixation and as well as for the development of different colour shades.
Printing table
Printing bed is prepared several thickness of blanket are carefully laid on the table, and the hole is covered with sheet of waterproof fabric. The cloth 10 x10 inches was spread out on the table and fixed it tightly by head pinning. Care to be taken that no movement of the cloth occurs during the printing operation.
Selection of wooden block
A flat, smooth surface square shape wooden block of size 3×3 x3 inches and also for uniform application of dye paste on fabric and easy to test of handle & colour fastness properties of printed fabric
Preparation of printing paste pad
Printing paste pad was prepared by using soft old cotton fabric was folded four times and placed in a open mouth bowl of plastic and dye paste of was poured on fabric and dye paste allowed to absorbed completely by the fabric. Wooden block was pressed on printing paste pad & paste was stamp on surface of fabric .
Standardization concentration of guar gum for sharp printing
Selected thickening agent guar gum powder was taken in different concentrations as 4gm, 6gm, 8 gm, 10gm, 12 gm , 14gm in separate beakers and constant amount of 20 ml concentrated extract of parijataka flower pigment was added in each beaker for preparation of printing paste & stirred carefully for avoiding lumps formation & kept for setting. Block printing carried with each concentration of guar gum printing paste and dried samples on place .Evaluation of printed sample for sharp print outline and suitable concentration of guar gum thickener that developed sharp outline after printing was noted.
Printing process & drying of samples
With standardization concentration of guar gum of 8 gm and pigment extract of parijataka 20 ml mixed & printing paste was made and block printing was carried out on selected fabric and allowed to dry on printing table on selected time scale such as 30, 45, 60, 75, 90 and 105 minutes and samples washed to remove gum layer. Correct time scale for transfer of pigment from thickener phase to fabric phase was find out through measurement of colour strength using Tinctometer colour strength rating was noted.
Steaming of block printing samples
The role of steam is to achieve higher colour yield and higher degree of colour fastness. Steaming ensures the adequate amount of penetration of pigment molecules in the fiber of the fabric. For increasing colour fastness of block printed samples was carried out by normal steaming process. A metal strainer was placed over aluminum vessel in which boiling water was boiling and dried printed sample was placed on strainer and steam vapors allow to passing through printed sample. Steaming process was carried out an about 5 to 12 minutes as per the W. Clark (1987).After steaming of printed sample was washed for removal of printing paste layer and surplus unfixed dyestuff and dried in shade.
Evaluation of steam sample
Washed block printed sample were evaluated for colour strength and developed colour on fabric was identified by matching with the shade card and obtained shade was noted.
Dye fixation using mordants
Steam treated block printed samples was mordanted using post mordanting method. Standardized concentration of selected mordants alum (6gm), AlFeso4 (8gm),Feso4 (8 gm)and Cuso4 (6 gm) .Mordants were dissolved in the warm water and printed samples was soaked in the mordant solution for the dye fixation by standardized mordanting time scale 20 minutes. And change in colour shade due to metallic salt treatment was identified by colour match with shade card and colour strength was measured using colour measuring instrument Tinctometer and colour rating was noted.
Evaluation of sample for handle & sharp print
Mordanted and without mordanted samples were evaluated visually for uniformity of colour, sharpness of outlines & overall appearance .Assessment of handle was carried out by sensory evaluation by touch & crumpled sample in hand for soft and stiff in feel and assessment scoring was given as per the grading and rating such as excellent (5), very good (4), Good (3), fair (2) and poor (1) with the panel of 30 judges comprises of textile experts and research scholars.
Testing of colour fastness properties of block printed samples
Mordanted and without mordanted samples were tested for colour fastness properties such as washing, rubbing & friction using Crokometer, hot pressing (hot iron), sunlight fastness & perspiration .Fastness rating was measured as per AATCC (American Association of Textile Chemist & Colourists).Colour fastness rating was express by numerical number as 5 to 1 and grading as excellent to poor respectively.
Results & Discussion
Extraction of pigment from orange stalk of parijataka flowers
Orange stalk of parijataka flowers content orange pigment and it was found that pigment is easily dissolved in water, colour of extract is visible dark orange and in the combination of yellow and red pigment. Colour yield showed by colour strength rating as per the Tinctometer was recorded as 30y10R.Y is indicated as yellow colour &‘R’ indicated red pigment present in extract. Yellow pigment (30) was more as compared to red (10) . Result revealed that 20 minutes time was found to be sufficient for extraction of pigment.
Table.1. Standardized conditions for block printing
S.no | Standardized printing conditions | Colour strength | |
1 | Time for extraction of pigment | 20 minutes | 30y10R |
2 | Standardized quantity of guar gum | 8gm | |
3 | Standardized quantity of extracted pigment | 20ml | |
4 | Standardized time for mordanting | 20 minutes | |
5 | Standardized time for steaming | 10 minutes |
Y- yellow and R- Red
Table.2 Optimization different concentration of guar gum for block printing
S.no | Concentration of guar gum /20ml of extract | Evaluation printed samples for sharp/spreading colour | uniformity of colour | Handle fabric
Soft /stiff |
1 | 4 gm | Colour spreading | Not uniform | Soft handle |
2 | 6gm | Colour spreading | Not uniform | Soft handle |
3 | 8 gm | Sharp printing | uniform | Soft handle |
4 | 10 gm | Sharp printing | uniform | Stiff handle |
5 | 12gm | Colour paste not transferred from block | Not uniform | Stiff and harsh |
6 | 14 gm | Colour paste not transferred from block | Not uniform | Stiff & harsh |
Table.2 illustrates that utilization of different concentrations of guar gum with the pigment of parijataka and block printing carried out on cotton fabric. It was observed that 8gm concentration of guar gum printing paste consistency produced very softly smoothly stamped and transferred of printing paste on the surface of fabric. Result showed that uniformly spread printing paste and visible sharp outlines of block, overall appearance was found to be good & no spreading of printing paste was noted before drying samples. As the concentration of guar gum increases from 10gm to 14gm it was found that colour paste not transferred properly from block to fabric and miss printing was observed because of thick printing paste. At the lower concentration of guar gum 4 gm and 6gm printing paste used for printing ,spreading of colour from the margin of block was noticed because consistency of printing paste was thin and liquidly. Hence it was clear from the table that 8 gm concentration of guar gum was suitable for block printing on cotton fabric.
Table 3. Time required for absorption of pigment in the fiber of fabric
S.no | Concentration of
8 gm guar gum/20ml of extract |
Time needed for drying printed sample | Tinctometrically colour strength rating | Colour shade obtained
& identify matching with the shade card |
1 | 8 gm | 30 | 10Y5R | light yellow |
2 | 8 gm | 45 | 12Y5R | light yellow |
3 | 8 gm | 60 | 13Y5R | dark yellow |
4 | 8 gm | 90 | 15Y8R | orange |
5 | 8 gm | 105 | 15Y8R | orange |
6 | 8 gm | 120 | 15Y8R | orange |
Y- yellow, R-red
Table .3 showed that time required for absorption of pigment in the fiber of fabric. Block printing was done on six sample with optimized concentration of guar gum 8gm and parijataka pigment 20ml and samples get washed after 30 , 45 & 60 minutes and colour of samples evaluated visually changes was noticed in the colour shade from light yellow to dark yellow with colour strength rating as 10Y5R , 12Y 5R and 13Y5Rrespectively.As the time of drying was increased up to 90 minutes, higher colour strength rating 15Y8R was recorded and orange colour was observed. Further it was observed that colour strength rating was found to be constant at time of drying 105 to 120minutes.
Table 4. Dye fixation using of parijataka pigment using selected mordants
S.no | Mordants
(10gm) |
Tinctometrically colour strength rating | Colour shade identify matching with the shade card |
1 | Without mordanted | 15Y5R | Orange |
2 | Alum | 20Y8R | Dark orange |
3 | AlFeso4 | 15Y8R2B | Dry leaf brown |
4 | Feso4 | 25Y15R5B | Brown |
5 | Cuso4 | 10Y8B | light peseta green |
Y- yellow , R-red and B- blue
It was observed from table .4 that colour strength rating of was increased from 15y 5R to 20y8R when alum used for dye fixation colour shade was also noticed as dark orange. AlFeso4 mordant was found to be effective & changed the dark orange colour in to dry leaf brown colour with colour strength rating 15Y8R2B and Feso4 mordant used fixation of pigment of parijataka flowers record higher colour strength rating as 25Y15R5B and obtained brown colour .When copper sulphate used for mordanting (dye fixation) developed light peseta green colour with colour strength rating was noticed as 10y8B. It can be concluded that all the selected mordants was found to be suitable for development of various colour shades.
Table .5 Testing of colour fastness properties of cotton fabric block printed with parijataka
pigment
S.no | Colour fastness rating | |||||
Mordants/ | Washing | Sunlight | Hot pressing | Perspiration | Rubbing
|
|
1 | Without mordanted | 2 | 2 | 2 | 2 | 2 |
2 | Alum | 4 | 4 | 4 | 4 | 4 |
3 | AlFeso4 | 5 | 5 | 5 | 5 | 5 |
4 | Feso4 | 5 | 5 | 5 | 5 | 5 |
5 | Cuso4 | 1 | 1 | 1 | 1 | 1 |
Excellent-5, Very good-4, good-3 , fair-2, poor-1
It was observed from table 5 that colour fastness properties of parijataka pigment block printed sample of without mordanted samples exhibited fair colour fastness with fastness rating 2. It was observed that alum, aluminum ferrous sulphate and Feso4 mordanted sample colour fastness properties was found to be excellent to good with colour fastness rating as 5 to 4 respectively . Copper sulphate mordant used for dye fixation developed light peseta green colour and fastness properties was found to be poor with colour fastness rating 1. It was clear from the result that alum, AlFeso4 and Feso4 mordants (metallic salts) were found to be effective to make the colour permanent of parijataka pigment and also for development of different colour shade
Conclusion
It can be concluded from the study that guar gum is cheapest thickener and has high viscosity. It was clear from the result that lower concentration of guar gum thickener found to be good for transferring of dye particles from gum phase to fabric phase and on higher concentration of guar gum showed miss printing. It is suitable for block printing because not react with natural pigment nor with cotton fabric. Pigment of parijataka easily dissolved in water, non toxic have medicinal value, and pigment easily penetrate in the fiber of fabric and developed attractive orange colour shade. All selected mordants alum, AlFeso4 and Feso4 was found to be effective for dye fixation and also developed attractive colour shades as dark orange, dry leaf brown and brown respectively .Parijataka flowers are the west material available in free of cost and suitable for block printing on cotton with natural thickening agent guar gum.
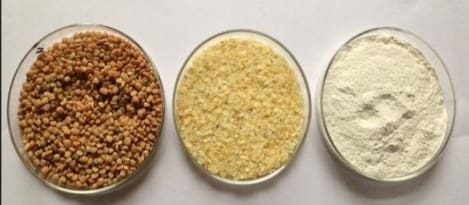
Seeds of guar, Guar gum
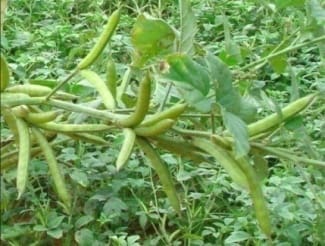
Legumes of guar
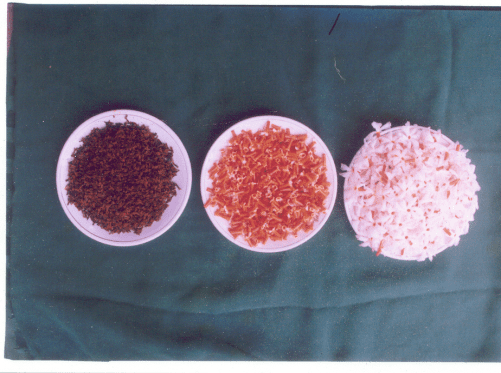
Dry & fresh orange stalk of parijataka flowers
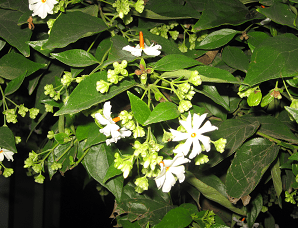
Flowers of parijataka
Mordants used | Colour shade developed |
Alum | ![]() |
AlFeso4 | ![]() |
Feso4 | ![]() |
Cuso4 | ![]() |
References
- Irfana Siddiqui etal (2002) Standardization of Mordants Concentration on Cotton &Silk Fabrics Dyed with Selected Flower Pigments. Journal Dairying Food &Home Science Sadar Karnal Haryana 21(1) 1:7
- Irfana Siddiqui etal (2003) Extraction of Pigments from Parijataka Palas & Cosmos Flowers And Its Utilization In Dyeing Silk & Cotton Fabrics. Journal Dairying Food &Home Science Sadar Karnal Haryana 52:58
- Irfana Siddiqui (2006) Dyeing of silk fabric with cotton flowers (Gossypium Hirsutum) ,Indian silk ,45(4): 17-18 Banglor
- Irfana Siddiqui (2007) Physical properties of cotton & silk fabric dyed with the pigment of flowers of parijataka ( Nyctanthes arbora) , Man Made Textiles in India,Mumbai,XIIX (7): 274 -278. ,45(4):
- Irfana Siddiqui (2007) Cosmos -Natural Dyes for silk fabric, Indian silk , Mumbai,45(12): 20-23
- Pant (1999) Natural Dyeing of wool, Indian Textile Journal 109(7), 50-53
- Dedai (1992) Ecological and Toxical properties of dyestuffs , Colourage 39,12: 51-54
- Susan Paul, Ms Ekta Grover& Ms. Anshu Sharma (2003) Application of natural dye Berberis Vulgaries on wool and its colour fastness, Man Made Textile of India vol- XLVI No.-8, 311-316
- Clark (2004) An Introduction to Textile Printing, A practical manual for Use in Laboratories College & school of Art, Wood Head Publishing Limited, Cambridge England
- Kale D G (1976): Principles of Cotton Printing, 2nd Ed, Mahajan Brother Publication.Ahmadabad. 128-139.
- Narkar R K (1991): Perspective in Printing with Reactive Dyes, Colourage, Supplement of September Issue.38, 2 : 39-42.
- Shenai V A (1999): Technology of Printing, 4th Ed, Mumbai Sevek Publication, 64-75 .
- Sonja S I, Ostar T and Schneider R (2000): Printing Properties of a High Substituted Guar Gum and its Mixture with Alginate Ecology and Colour Science,5. Indian Journal of Fiber and Textile Research, vol.36(2):132–146
- ISI Hand Book of Textile Testing, (1982) Indian Standards institution, New Delhi, 538- 539, 571- 572.
- Featured Image: Flickr
Author:
Dr. Irfana Siddiqui & Md Uzam Quadri
Assistant Professor & Students ( B.C S)
Department of Textiles & Apparel Designing
College of Community Science
VNMKV Parbhani, 431402