Abstract
Mechanical yarn stretch (%) in sizing process is amongst one of the process control parameters affecting warp yarn breakages in looms. For assessing the level of significance of the treatment factor on the response, ANOVA analysis including analysis of sum of squares, degree of freedoms and mean square analysis is done. Experimentation is done in Bahir Dar Textile Sh. Company weaving mill using cotton yarn of 20s for making of 20s x 20s / 60 x 60 fabric particulars or bed sheet article. The 4 different weavers’ beams prepared using the stated yarns are prepared in 4 different mechanical yarn stretch percentages but having same size pick-up, concentration and moisture content percentages and made to be run on the loom at the same speed of 500RPM. A single factor experiment with 4 levels of the factor and 3 replicates, i.e 12 runs has been made. Using significance level of α = 0.05, the experimentation shows mechanical yarn stretch % in sizing process significantly affects the warp yarn breakages (warp cmpx) in looms, so process optimization and linear regression model development has been conducted. Thus, the two unknown coefficients βo& β1 have been calculated to be -1.6092 & 4.21689, and the linear regression model is computed as; y = -1.6092+4.2169X1
Key words: Mechanical yarn stretch%, Warp yarn cmpx, Cotton yarn of 20s, ANOVA analysis, linear regression model.
Introduction
The most critical issue in sizing is to control the yarn stretch. As yarns pass through the long path from creel to head stock, the tension applied in the process will tend to elongate it. If this elongation is not controlled, the deformation so introduced will be permanently set in the yarn.
The control of yarn elongation (stretch) between the squeezing rolls of the size box and the first drying cylinder is critical, since the wet yarns under high heat, undergo stretching even at low tensions. This must be controlled by proper selection of the drive system, such as digital or variable speed differential transmission between the size box and the drying unit.
The tension develops when the yarn is passed through the drying cylinders for ensuring proper drying. The surface speeds of all the drying cylinders should be controlled and if they are uniform, no stretch will develop in the drying zone. A uniform stretch from section beam to section beam throughout the warp must be maintained.For sizing machines, which the stretch control % is clearly shown on the machine’s control panel, we can directly take the figure as mechanical yarn stretch %. But suppose the machine is old model and no control panel is there, we have to calculate the mechanical yarn stretch % in sizing as per the SOP (standard operating procedure) stated below:
SOP to check the stretch %
Purpose: to reduce elongation loss %
Back meter counter must be fixed at back of the sow box,
At starting of the beam set the front machine counter at ‘0’
At the same time set the back meter counter also at ‘0’
At the time of completion of the beam note & record the reading of the front machine counter,
At the same time note & record the reading of the back meter counters,
The stretch % to be calculated as follows:
Stretch %=Front counter reading-back counter reading/back counter reading
Materials and methods
Materials
The experiment is conducted in Bahir Dar textile factory with the use of cotton yarn having the following details stated in table 1: [3]
Table 1 Sample cotton yarn details
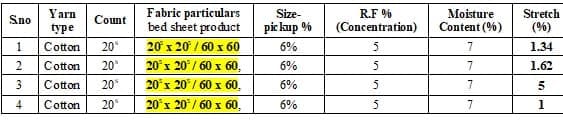
As it is stated in the above table, throughout the experiment cotton yarn of 20s has been used with the same size concentration (%age), moisture content (%age) and size pick-up (%age). Keeping the stated parameters the same, mechanical yarn stretch (%) has been varied for experimentation. So in this research, the effect of stretch on warp yarn breakage (warp cmpx) in picanol air-jet looms of same weaver group has been assigned. Here, all the 4 weavers’ beams have been loaded on 4 Picanol air-jet looms operated by same weaver-group and all the looms were running at 500 RPM.
Results and discussions
A single factor experiment with a= 4 levels of the factor and n = 3 replicates, i.e 12 runs of experimentation are conducted and in table 2 results are shown:
Table 2 Data showing observations vs. sources of variations
Stretch (%) | Observations (Warp cmpx) | Total, yi.. | Average, yi.. | ||
1 | 2.3 | 4.0 | 3.1 | 9.4 | 3.13 |
1.34 | 3.2 | 3.5 | 2.4 | 9.1 | 3.03 |
1.62 | 5.6 | 7.2 | 4.5 | 17.3 | 5.77 |
5 | 25.1 | 25.2 | 8.5 | 58.8 | 19.6 |
94.6 | 7.8825 |
Total, yi.. = 9.4+9.1+17.3+58.8 = 94.6
Average, yi.. = (3.13+3.03+5.77+19.6)/4 = 7.8825
Analysis of sum of squares
SST = 2.32+4.02+………..+8.52 – 94.62/12
= 754.14……..…… (1)
SSTreatments= 1/3 [9.42+……….+58.82]-94.62/12
= 563.54……..…… (2)
SSError= SST – SSTreatments…………..………..…. (3)
= 754.14-563.54 = 190.6
Analysis of degree of freedom (DF)
Table 3 Analysis of degree of freedom (DF)
DF | |
Between treatments | a-1, 4-1=3 |
Error (within treatments) | N-a, 12-4=8 |
Total | N-1, 12-1=11 |
Analysis of mean squares
MSTreatments= SSTreatments/a-1] = 563.54/3
= 187.85…… (4)
MSError= SSError/N-a = 190.6/8
= 23.825 ….. (5)
Fo= MSTreatments/MSError = 187.85/23.825
= 7.8845 … (6)
Suppose we select α = 0.05, the probability of reaching the correct decision on any single comparison is 0.95.
Now we compare Fo with the distribution table at α = 0.05 significance level. We get F0.05,3,8= 4.07.
Fo= 7.8845>4.07, so we reject Ho (null hypothesis), which tells: µ1=µ2=….µa and accept H1, which tells µi≠µj for at least one pair and conclude that the treatment means differ; that is mechanical yarn stretch % in sizing process significantly affects the warp yarn breakages (warp cmpx) in looms. Since it is known that the process parameter significantly affects the warp cmpx, process optimization and regression model development is needed.
Now we compute the p-distribution:
P0.01,3,8= 7.59, because Fo>7.59, we can conclude that an upper bound for the P-value is 0.01; that is P<0.01.
Table 4 ANOVA for warp yarn breakage (warp cmpx) experiment
Source of variation | Sum of squares | Degrees of freedom | Mean square | Fo | P-value |
Mechanical yarn stretch % | 563.54 | 3 | 187.85 | 7.8845 | <0.01 |
Error | 190.6 | 8 | 23.825 | ||
Total | 754.14 | 11 |
Computation of R2
R2 = SSTreatments/SST…………. (7)
=563.54/754.14
Thus, in this experiment, the factor ‘mechanical yarn stretch’ explains about 74.7 percent of the variability in warp yarn breakage (warp cmpx).
Process optimization and linear regression model development [1]
y = βo+β1X1+€…………..… (8)
β = (X’X)-1X’y……………… (9)
So from the data achieved based on the experimentation done, we have:
X= 1 1 | y= 3.13 |
1 1.34 | 3.03 |
1 1.62 | 5.77 |
1 5 | 19.6 |
X’X= 1*1+1*1+1*1+1*1=4, 1*1+1*1.34+1*1.62+1*5=8.96
= 1*1+1.342+1.622+52= 30.42
X’X = 4 8.96 | X’y= 31.53 |
8.96 30.42 | 114.54 |
X’y= 1*3.13+1*3
03+1*5.77+1*19.6= 31.53
=1*3.13+1.34*3.03+1.62*5.77+5*19.6= 114.54
β = (X’X)-1X’y…………. (10)
(X’X)-1= 1/ [(4*30.42) -(8.96)2] * 30.42 -8.96 -8.96 4 | = 0.73 -0.215 -0.215 0.096 |
Now we can compute β= (X’X)-1X’y as:
βo= (0.73*31.53) + (-0.215*114.54) = -1.6092
β1= (-0.215*31.53) + (0.096*114.54) = 4.21689
So the linear regression model and the scatter diagram showing the relationship between mechanical yarn stretch (%) in sizing and warp yarn breakage (warp cmpx) in looms can be computed and shown in fig.1 as:
Fig. 1 Scatter diagram and linear regression model
y = βo+β1X1+€…………………… (8)
y = -1.6092+4.2169X1
Where y, is warp yarn breakage (warp cmpx),
X’=
X’= 1 1 1 1 |
1 1.34 1.62 5 |
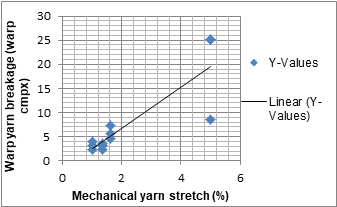
X1, is mechanical yarn stretch (%) in sizing,
Conclusion
The experiment is done in Bahir Dar textile sh. Company weaving mill with the use of cotton yarn of 20s with same size pick-up, concentration and moisture content percentages has been used for assessing the effects of variation of mechanical yarn stretch percentage on warp yarn breakages (warp cmpx) in Picanol air-jet looms of same weaver group running at the speed of 500 RPM. Using a single factor experiment of 4 levels of the factor and 3 replicates, i.e 12 replicates has been made for computing ANOVA analysis which has been discussed in table 4 and showing: analysis of sum of squares, degree of freedoms and mean squares. With the use of 0.05 significance level (α=0.05), it is proved that mechanical yarn stretch (%) significantly affects the warp yarn breakage (cmpx). Since this is the case, process optimization and linear regression model development has been conducted. For drawing the linear regression model,
0.73 -0.215 * | 31.53 |
-0.215 0.096 | 114.54 |
The two unknown coefficients βo& β1 have been calculated to be -1.6092 & 4.21689, and the linear regression model is computed as;
y = -1.6092+4.2169X1. The scatter diagram and linear regression model development has been shown in fig. 1.Computation of R2 has been done to find 0.747, showing the factor ‘mechanical yarn stretch’ explains about 74.7 percent of the variability in warp yarn breakage (warp cmpx).
References
[1] Douglas C. Montgomery, ‘Design and analysis of experiments’ Eighth edition, John Wiley & Sons, Inc.2012,
[2] K.L. Gandhi, ‘Woven textiles principles, developments and applications,’ Wood head publishing series in Textiles: Number 125, 2012,
[3] Bahir Dar textile factory, Weaving preparatory & loomshed section data,
By-
Neway Seboka
Ethiopian Textile Industry Development Institute
MENTORED BY TEXCOMS TEXTILE SOLUTIONS