A revolutionary technology addressing environmental concerns of conventional fabric dyeing
By removing the requirement of water at the point of colour application, Air-Dye technology creates a significant opportunity to localize production for regions of the globe that lack the water resources traditional methods require.
Textile wet processing Industry is one of the highest water-consuming industries. 17-20% of today’s industrial pollution is the result of the textile coloring treatment, contributing to 72 toxic chemicals in water supplies, 30 of which are permanent processes. To reduce these water contaminations, a new technology called “Air-Dyeing” has been introduced.
The Air-Dyeing uses 95% less water and 86% less energy than conventional fabric dyeing processes. While 10% of the conventionally-dyed fabric is damaged during the production process, only 1% of Air-Dyed fabrics are damaged during air-dyeing and no post-treatment or finishing is required. This reduces the industry’s share of global warming by 84%.
The key factor of this technology is airflow with air being a perfectly suitable transport medium. The jet dyeing machines use air instead of dyed liquor as a transport medium for piece goods and this reduces consumption of chemicals and water to a great extent. Air Dye process is 2-sided and the hand feel of the finished fabric is luxurious and clean. Air Dyeing is a revolutionary method of dying that causes minimum harm to the environment.
Introduction
Water is used in everything from irrigation to raising livestock, to dyeing textiles for the clothing we wear. But the textile industry is one of the most villainous sectors when it comes to depleting and polluting fresh water sources.
Discontinuous processing of textile substrates requires more water and energy compared to continuous processes. However, for a long time efforts are undertaken to optimize discontinuous processes with respect to productivity, efficiency and also to minimize energy and water consumption effectively.
The World Bank estimates that 17-20% of today’s industrial pollution is the result of the textile colouring and treatment, contributing to 72 toxic chemicals in water supplies, 30 of which are permanent.
Machine GmbH’s Airflow dyeing concept was invented by Wilhelm Christ and subsequently patented in 1978 by then, which produced the first prototype. It was developed and patented by Colorep, a California-based sustainable technology company. The company that patented this technology claimed after conducting an independent assessment that ‘air dyeing’ the fabric reduces water consumption by 95% and energy use by 86% depending upon the type of dyeing and fabric used. This reduces the industry’s share of global warming by 84%. The key factor of this technology is airflow with air being a perfectly suitable transport medium. The jet dyeing machines use air instead of dyed liquor as a transport medium for piece goods and this reduces consumption of chemicals and water to a great extent.
Principle of Air-dyeing
In airflow dyeing machine, dyeing liquor is first atomized, then mixed with high-pressure airflow, finally sprayed on fabric to be dyed. Because water just serves as a solvent of dyeing liquor and the dye chemicals directly contacts the fabric, only a little water is consumed. Compared with overflow dyeing machines, airflow dyeing machine has the merits of high efficiency, energy-saving, and environmental protection.
The basic principle underlying the aero-dynamic system is that the fabric passes through an air-steam mixture emitted from a blower. This means that contrary to a hydraulic dyeing machine, neither a dye bath nor an aqueous medium is needed for fabric transport. In other words, the fabric passage is possible without liquor. The material is in constant motion from feeding to the end of the process, as well as during drainage and filling procedures.
Figure 1 shows the air suction pipe, which has been designed as a filter, in the center of the dyestuff vessel. The blower and the airline, which leads to the transport nozzle, can be seen in the background. The fabric skein is drawn off from the dyestuff vessel by the winder, fed to the nozzle line and then returned to the storage chamber via the cutter.
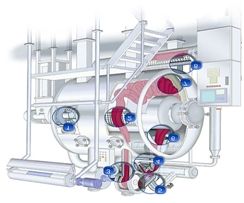
The storage chamber is fitted with PTFE rods (Figure 2). PTFE, which is familiar under the brand name Teflon, offers very good non-adherence characteristics with the result that the surface of the fabric is well protected. There is no dyeing liquor in the dyestuff.

To achieve very low Liquor Ratios ranging from 1:3 to 1:4.5, within the machine (jet), the fabric is moved by moisturized air or a mixture of steam and air only (no liquid) along with a winch. The prepared solutions of dyestuffs, auxiliaries and basic chemicals are injected into the gas stream. The bath level is always below the level of processed textiles in order to maintain low LR. Rinsing is carried in a continuous manner.
During the whole rinsing process, the bottom valve is open and rinsing water is discharged without additional contact with the fabric (which is the case in conventional machines). This also allows the discharge of hot bath liquors after high-temperature dyeing at 130°C. Thus, in addition to time-saving, optimum heat recovery can be performed. The fabric itself is processed with low tension and crease formation is minimized.
Reference: https://www.textileschool.com/5234/air-flow-dyeing-an-eco-friendly-water-preserving-fabric-dyeing-technology/