Innovative process belt designs as reliable protection against electrostatics and material adhesion
Technical weaving operation GKD – Gebr. Kufferath AG (GKD) will once again be showcasing its integrative consulting and engineering expertise for the nonwovens industry at INDEX in Geneva, the world’s largest nonwovens exhibition. In keeping with the corporate vision of only creating products and solutions that make the world healthier, safer, and cleaner, GKD will be presenting a comprehensive range of mesh and spiral fabric belts for forming, drying, and bonding of nonwovens here. The company’s presence at the exhibition will focus on two pioneering developments: CONDUCTO® 7690 with metallic multifilaments, and glass hybrid fabric belts with anti-stick coating. The exhibition appearance will be rounded off with tailor-made metal fabric filter media, which have been proven to set new standards in the central filters, spinning beams, and blower screens used for polymer filtration. The GKD experts, boasting many years of experience, will be on hand at the INDEX event for more detailed discussions on all topics.
Achieving maximum process reliability and system availability is crucial in securing production efficiency and the success of products in the nonwovens industry. Conveyor and process belts from GKD perform a key task here thanks to their system-specific and product-specific mesh design and the materials used in their construction.
Spunlaid nonwoven forming: Metallic dissipation also for hygiene products
With CONDUCTO® 7690, a fabric design comprising polyester monofilaments and metallic multifilaments, GKD has succeeded in preparing electrostatic dissipative metal in such a way that it can also be used for sophisticated medical and hygiene products without any risks. This latest addition to the CONDUCTO® range facilitates between one and ten times greater dissipation of electrostatic charges than conventional belts. The metal fibers that are woven into the back of the belt do not come into contact with the product. The flexible yarn produced from stainless steel fibers does not suffer from corrosion or bending fatigue and is also rugged. At the same time, it optimizes dissipation of electrostatic charges with unprecedented efficiency. The new fabric design combines these properties with the familiar benefits of all CONDUCTO® forming belts: excellent traction, homogeneous web formation, optimum nonwoven removal, and easy cleaning.
Web bonding and drying: Years of service without any material adhesion
The glass hybrid fabric belts with anti-stick coating from GKD have a proven track record of significantly increasing process efficiency. Used as upper and lower belts in real-world applications over multiple years, they have far surpassed the high expectations in terms of process performance and product quality in exacting thermal bonding processes with highly adhesive products. The single-ply fabric design, comprising metal weft wires and fiberglass strands as the warp, makes the belts energy-efficient lightweights. A service life of multiple years, minimized cleaning intervals, and high production speed underline their efficiency. The glass hybrid fabric belts also impress with excellent transverse stability and running characteristics, even when used with large working widths and strong product shrinking forces. Their complete, high-grade PFA coating protects wires, strands, and intersections from any kind of material adhesion, even when processing highly adhesive products or using bicomponent fibers. Glass hybrid fabric belts are temperature resistant up to 250°C and do not stretch.
Converting: Field-proven and high-performance alternative
Custom spiral fabric belts, produced in-house to customer specifications, complement GKD’s portfolio of tried-and-tested process belts. These spiral fabric belts often represent an attractive alternative, particularly when using very wide or high-speed systems for production of hygiene products. Featuring high air permeability and excellent dimensional stability, they once again serve to underline GKD’s integrative process and conveyor belt expertise.
Polymer filtration: Long service life, precise filtration
Multi-layer metal fabric screens, designed and produced by GKD for specific processes, ensure a long service life of the screen changers in central filters. The filter discs or cartridges, produced from up to six layers of optimized dutch weave, impress due to their high dirt holding capacity, fine filtration rates, and low clogging tendency. In the spinning beam, media designed for specific applications optimize filtration of the fusion flow in long filters or long screens, while also extending the service life of the spinnerets. Blower screens produced from honeycomb supporting plates, employing specially pretreated fabric designs on both sides, guarantee an even fiber flow thanks to a homogenized stream.
Visit
GKD – Gebr. Kufferath AG
at INDEX in Geneva
March 31 – April 3, 2020
Stand 2180
GKD – WORLD WIDE WEAVE
As a privately owned technical weaver, GKD – Gebr. Kufferath AG is the world market leader in metal, synthetic and spiral mesh solutions. Four independent business divisions bundle their expertise under one roof: Industrial Mesh (woven metal mesh and filter solutions), Process Belts (belts made of mesh and spirals), Architectural meshes (façades, safety and interior design made of metal fabrics) and Mediamesh® (Transparent media façades). With its headquarter in Germany and five other facilities in the US, South Africa, China, India and Chile – as well as its branches in France, Spain, Dubai and worldwide representatives, GKD is close to markets anywhere in the world.
GKD at INDEX 2020
Innovative process belt designs as reliable protection against electrostatics and material adhesion
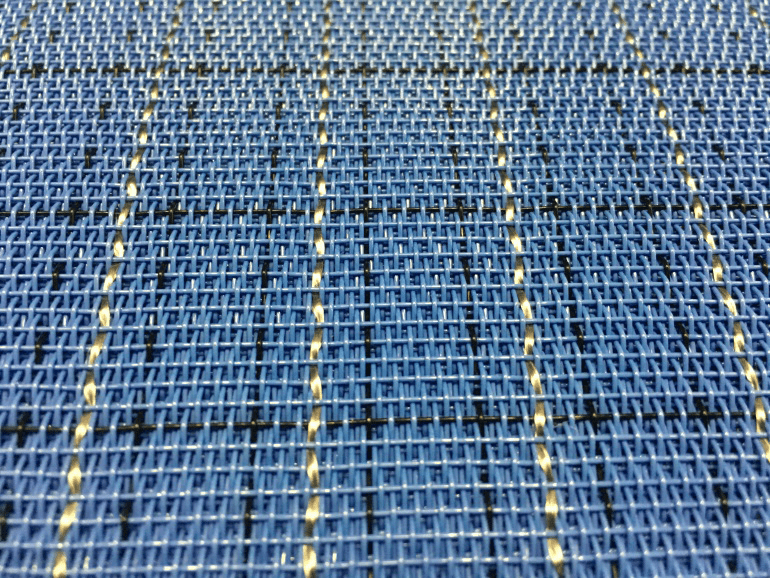
facilitates between one and ten times greater dissipation of electrostatic charges than conventional belts.



GKD – Gebr. Kufferath AG
Responding to global needs through creative leadership in technology With its commitment to devising exceptional solutions for industry and architecture, GKD – Gebr. Kufferath AG (GKD) has been developing wire mesh structures that contribute to a more healthy, cleaner and safer world for more than 90 years. Whether filtration and separation processes in mechanical process engineering, key process belt functions in a multitude of industrial applications or tasks in and around building optimization: the technical weaver’suniquely broad spectrum of expertise has helped it secure a world- leading position as a high-tech service provider for demanding nichemarkets. Thanks to its global presence, innovative technologies and future-driven business models, GKD consistently translates market requirements into Sustainable success for its customers. As such, the company, which is now in its third generation of ownership by the Kufferath family, is regularly setting new standards worldwide with its leading competence and a passion for design. A long-term mentality and a responsible corporate culture make the independent medium- sized weaver a reliable partner even in times of dynamic change.
The traditional drivers of GKD’s success are the development and manufacturing of high-performance, application-specific mesh structures coupled with proximity to the market and customer focus. Agility, curiosity and the ability to recognize changed market needs at an early stage made the family company the global market leader in numerous niche markets. Since its foundation in 1925 – long before the term “megatrend” was coined – the technical weaving company has focused on growing fields that influence all areas of society and the economy. Today, GKD is working
more than ever before on responding to global needs – water, nourishment, protection of the environment and resources, mobility and health – with a
range of products and applications. The company fills this mission with life
by combining pioneering manufacturing technologies with decades of evolved, cross-sector problem-solving expertise and global production capacities.
Customer perspective as a driver of growth
The basis for this is the culture of the family company: a wealth of experience gathered over three generations, a great capacity for innovation applied on a consistent basis and a focus on the sustainability of the solutions, relationships and processes. Crucial strategic moves made by GKD at regular intervals have turned the traditional art of weaving into a key technology for numerous industries. Special weaving machines developed in-house, cleanroom production, a broad spectrum of tools, automation, simulation and camera inspection as well as close cooperation
with renowned research institutions have given the technical weaver a leading role as a solutions provider. Constant large-scale investments in new technologies continue to secure this strong market position. At the same time, the sophisticated multi-platform strategy with identical, certified quality standards applied throughout the Group enables the development of complex delivery chains that are specifically tailored to customer needs. GKD resolutely drives forward the digitalization of business processes in order to further enhance the advantage the company enjoys through innovative, perfect-fit product service systems and globally networke knowledge management. Through this continuous focus of all processes on customer value, the medium-sized company underlines its declared goal of achieving long-term and sustained success for our customers through innovation.
Key technology for central challenges
Leading companies worldwide from the automotive, electronics, life sciences, aviation, paper, textile, food and beverage industries,from the fields of wood processing, raw material extraction and environmental technology as well as building owners place their trust in this expertise.
The wide range of water treatment technologies is just one example of the decades of expertise that today make the technical weaver an internationally sought-after solutions partner for global requirements. Process belts from GKD have been an established standard in belt presses for sewage sludge disposal since 1967. Today, the high-tech meshes also regularly set new standards in drinking water, waste water and ballast water treatment as well as in sewage sludge drying. In the food and beverage industry, woven solutions from GKD take on key functions in cooking oil filtration, food production and fruit juice production. Moreover, the products of the medium-sized company are used extensively in energy and raw materials production, oil and gas extraction as well as in key components of electromobility. Metal mesh contributes to health, safety and well-being by optimizing the energy balance or acoustics of buildings, by functioning as fall guard protection or providing protection from lightning, explosions or noise and in a variety of applications relating to the production of hygiene articles. In the MEDIAMESH® transparent media façade system, GKD combines visually aesthetic, functional and ecological product properties with the possibilities offered by state-of-the-art digital media.
Sustainability as an overall strategy
However, GKD not only lives its promise of sustainability through long-term customer relationships and the consistent orientation of its product portfolio toward a healthy, clean and safe world. Environmentally friendly production processes, careful management of raw materials, the use of virtually fully recyclable stainless steel, responsible and honest dealings with customers and employees and strict compliance with regulations are also traditionally anchored in the company strategy and company-wide standards. With six plants – in the USA, South Africa, China, India and Chile alongside the main headquarters in Germany – and subsidiaries in France, Spain and Dubai as well as representative offices across the globe, GKD is close to
markets anywhere in the world. After all, local presence is a prerequisite for further growth through tapping new markets.